Basic Parameters Of Die Casting Process
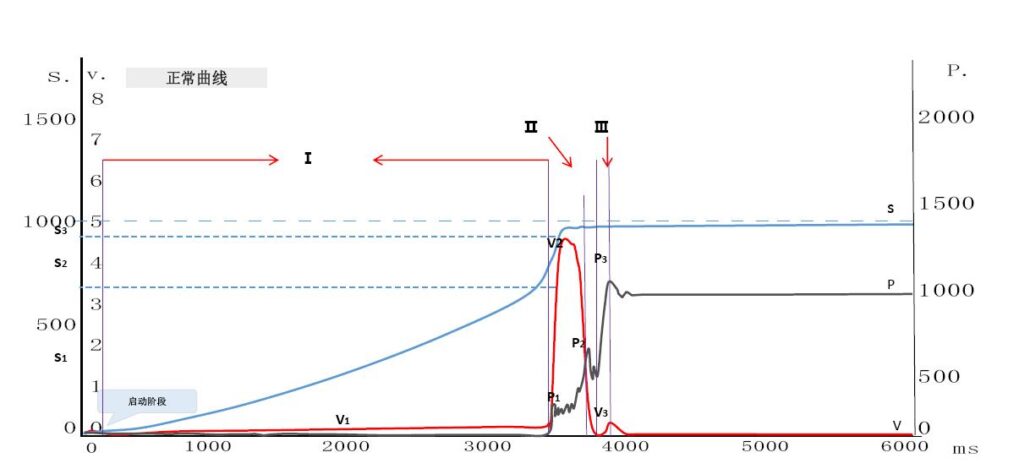
The die-casting process organically combines and applies the three major mold elements, the die-casting machine and the alloy’s characteristics.
Therefore, it is necessary to analyze and study the die casting process’s nature, characteristics, and regularity. The most important process in die casting production is the process of a liquid metal filling, which is a process in which many factors work together.
The main factors affecting filling are pressure, speed, temperature, and time. Each process factor affects and restricts the other. Therefore, when a process factor is adjusted, the corresponding process factor will inevitably change, which may, in turn, affect the adjusted process factor.
Therefore, selecting, controlling, and adjusting these process parameters is necessary. As a result, each process parameter is coordinated in a better state to meet the needs of die casting production to produce qualified die castings.
1.Pressure Parameters
Pressure is an essential factor in making the die-casting parts dense and clear. It is provided by the die-casting machine, and its size depends on the structure and power of the die-casting machine. There are two types of pressure representation: injection force and injection pressure.
In order to improve the density of castings, it is undoubtedly effective to increase the specific pressure of injection. However, if the injection specific pressure is too high, the cavity will be washed by the molten metal, the mold sticking tendency will be severe, and the service life of the mold will be reduced;
Therefore, the appropriate injection-specific pressure should be selected according to the characteristics of the casting and the different alloys. The die-casting machine can provide a wide range of injection ratio, 13 ~ 120MPaₒ
The injection pressure ratio required for different alloy castings is shown in the figure below
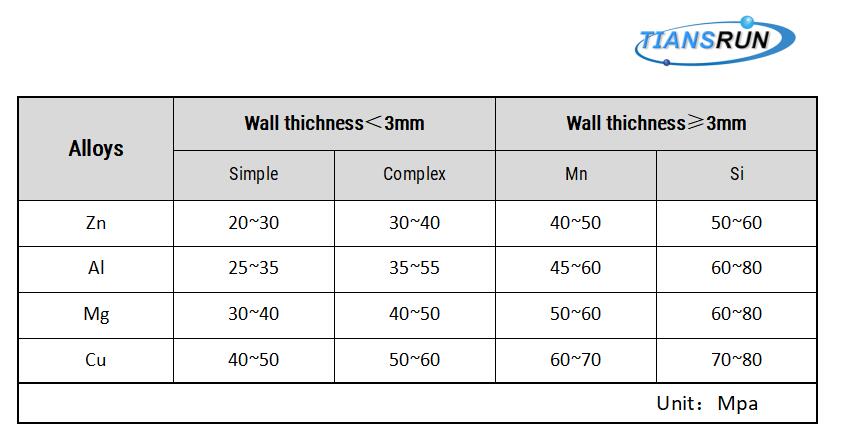
2.Speed Parameters
There are two forms of speed in die casting: injection speed and filling speed. The injection speed refers to the moving speed of the injection punch, and the filling speed refers to the linear speed of the molten metal flowing through the runner in the mold.
The filling speed and injection ratio pressure play a key role in the casting’s intrinsic quality, surface quality, and contour definition. The internal relationship between the filling speed and the specific pressure of injection can be expressed by the principle of fluid mechanics as follows:
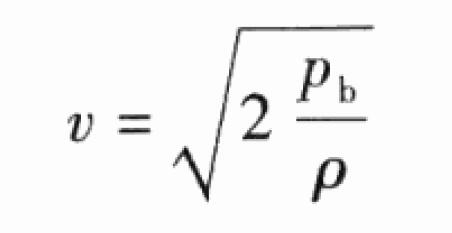
Due to the viscosity of liquid metal and the loss of kinetic energy due to friction when flowing through the mold gating system, the above equation should be rewritten as:

In the formula,
V – the filling speed of the molten metal flowing through the inner runner (m/s);
Pb – the injection specific pressure (Pa) applied to the molten metal;
ρ – density of molten metal (kg/m³);
Cd – resistance coefficient (or gate coefficient).
The choice of filling speed should be related to the casting size, complexity, alloy type, and injection pressure. For castings with simple thick walls or high internal quality requirements, low filling speed, high injection pressure, and large gate area can be selected due to the ease of filling.
On the other hand, for complex thin-walled or high surface quality requirements, castings requiring rapid filling, high filling speed, and high injection pressure should be selected. The commonly used filling speed is 20 ~ 90m/s. By adjusting the injection force of the die casting machine, the specific pressure of injection can be changed, and then the filling speed can be changed. The die-casting filling speed required for different castings is shown in the figure below.
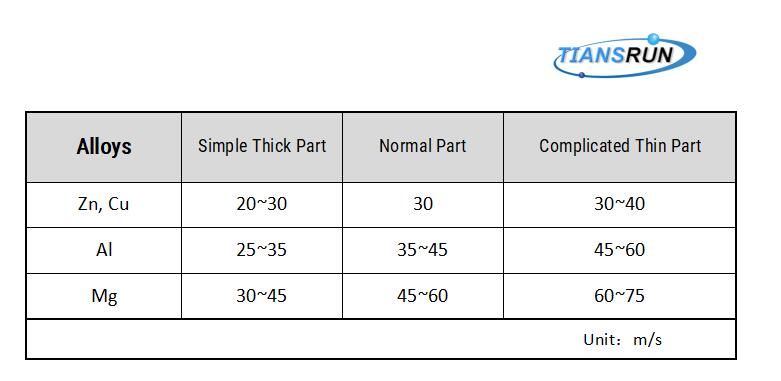
3.Time Parameter
The die-casting time includes the filling time, the holding time, and the time that the die-casting part stays in the die-casting mold. It is the combined effect of pressure, velocity, temperature, molten metal properties, casting structure (mainly wall thickness and volume), and mold structure (especially gating and overflow systems).
The time required for the liquid metal to enter the die-casting mold cavity and fill the cavity is called the filling time. The filling time is mostly between 0.01 ~ 0.2s. The length of the filling time depends on the size and complexity of the casting: for large and straightforward castings, the filling time is relatively long; for complex and thin-walled castings, the filling time is shorter.
The practice has proved that the filling time of small and medium-sized aluminum alloy die castings is about 0.2s. Therefore, the adjustment method of filling time is similar to the adjustment method of filling speed.
When the material and volume of the casting are determined, the filling time t is inversely proportional to the filling flow Qv, which is the product of the filling speed V and the cross-sectional area of the gate An. When a significant filling speed is used, it may still require a long filling time due to the small cross-sectional area of the ingate.
On the contrary, when the cross-sectional area of the inner gate is large, even if a low filling speed is used, It is also possible to shorten the filling time. Therefore, it cannot be said in isolation that the higher the filling speed, the shorter the filling time required.
The following formula can calculate the filling time t:
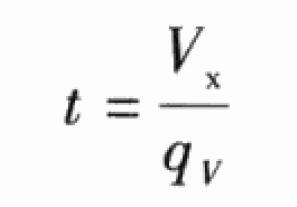
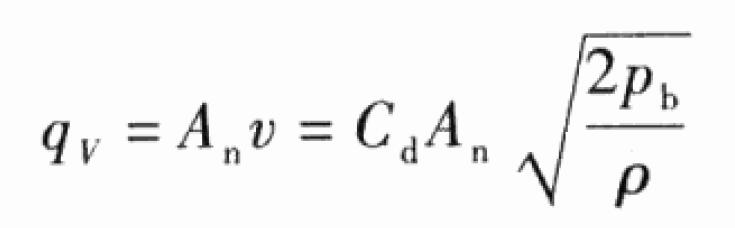
In the formula,
Vx – the volume of the mold cavity (cm³);
t – filling time (ms);
qv – flow rate of molten metal through the inner runner (L/s);
An – the cross-sectional area of the gate (mm²);
v – filling speed (m/s);
Cd – flow coefficient; for aluminum alloy, magnesium alloy = 0.5, for zinc alloy, copper alloy = 0.6;
ρ – metal liquid density (kg/m³);
Pb – Injection specific pressure (MPa) applied to the molten metal.
When considering the influence of the cross-sectional area of the inner gate on the filling time, it must be considered in relation to its thickness and shape. For example, if the cross-sectional area of the inner gate is large but thin because the metal is viscous during die casting, the thin resistance of the inner gate is substantial, which will prolong the filling time.
The too-thin inner gate will prolong the filling time, cause excessive loss of pressure and convert it into heat energy, which will cause local overheating at the inner gate and may cause mold sticking. The figure below shows the filling time required for castings with different wall thicknesses.
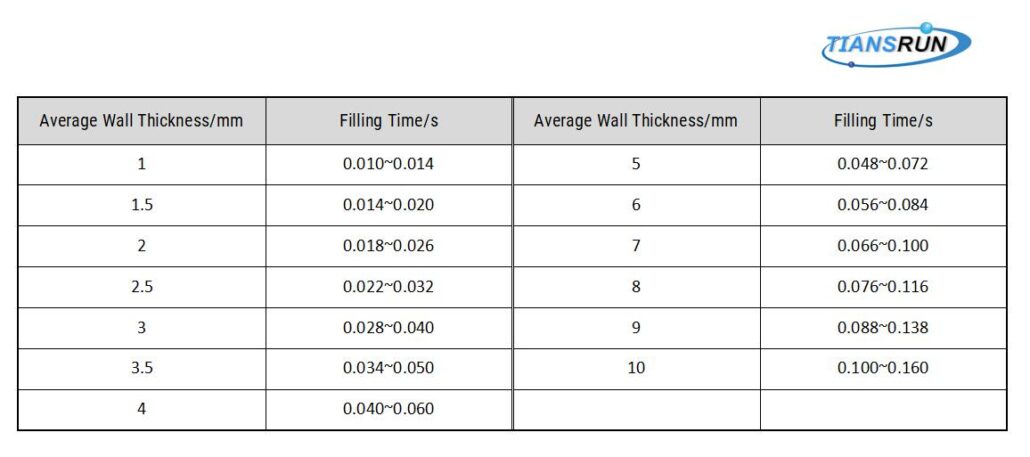
The duration from the liquid metal filling the cavity to the complete solidification of the inner gate, which continues under the action of the injection punch, is called the holding time. The function of the holding pressure time is to give the injection punch enough time to transfer the pressure to the metal that has not solidified, ensure that the casting crystallizes and solidifies under pressure, and strengthen the feeding to obtain a dense structure.
The holding time should be longer for castings with high melting points, large crystallization temperature ranges, and thick-walled castings; otherwise, the holding time may be shorter. When the holding time is insufficient, shrinkage is likely to occur; however, if it is too long (continue to hold the pressure after the solidification is completed), it will not have a significant effect.
For vertical die-casting machines, it will also cause difficulty in removing excess material. Generally, the holding time is 1~2s. However, for castings with an extensive crystallization temperature range and thick walls, the holding time is 2~3s.
Sometimes castings are often found to have cavities at the gate after removing the gate. This is not entirely caused by the inner gate’s inappropriate position or the inner gate or the cross-sectional area of the inner gate.
It is often caused by the insufficient pressure holding time and the reflow of the incompletely solidified molten metal. This phenomenon is more likely to occur for alloys with a large wall thickness or crystallization temperature range castings.
The time from the end of injection to the opening of the die-casting mold is called cooling time. Sufficient cooling time can give the casting a specific strength in the mold and not deform or crack when the mold is opened and ejected.
The length of cooling time is related to the ejection temperature of the casting. If the cooling time is short, the casting will be demolded when the strength is still low and easy to deform. For alloys with low strength, surface bubbles may be generated due to the expansion of internal pores.
However, if the cooling time is too long, the casting temperature will be too low, and the shrinkage will be large, which will increase the resistance of core pulling and ejection of the casting. Generally, the cooling time is calculated according to the 1mm wall thickness of the casting and 3s and is determined after adjustment by the test. You can also refer to the following selection.
Opening time required for different casting wall thicknesses (unit: s)
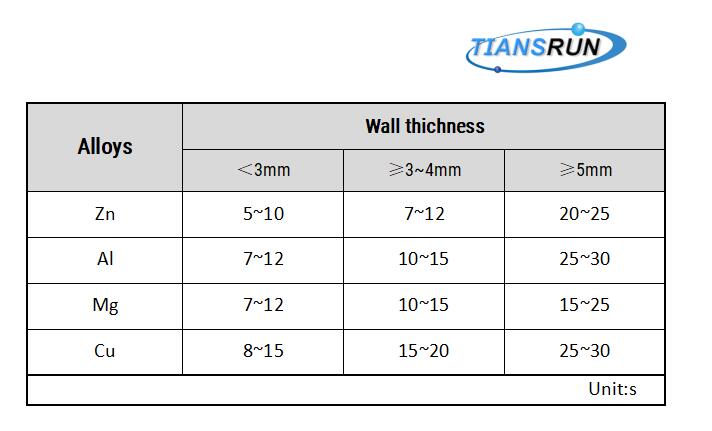
4.Temperature Parameters
The pouring temperature of the molten metal and the working temperature of the mold are the thermal factors in the die casting process. They are one of the primary process parameters for obtaining qualified castings. It is related to the casting structure, wall thickness, filling pressure, speed, and alloy type. In order to ensure good filling conditions, it is necessary to control and maintain this parameter at a reasonable level and stabilize it within a specific range.
If the pouring temperature is too high, you’ll notice the following;
- The shrinkage is large
- The casting is prone to cracks
- The grains are coarse
- The mechanical properties are decreased
- Mold sticking
- The life of the mold will be reduced.
Therefore, the pouring temperature should be considered simultaneously as the pressure, the temperature of the die casting mold, and the filling speed. Thus, the die casting filling temperature of different alloys is shown in the table.
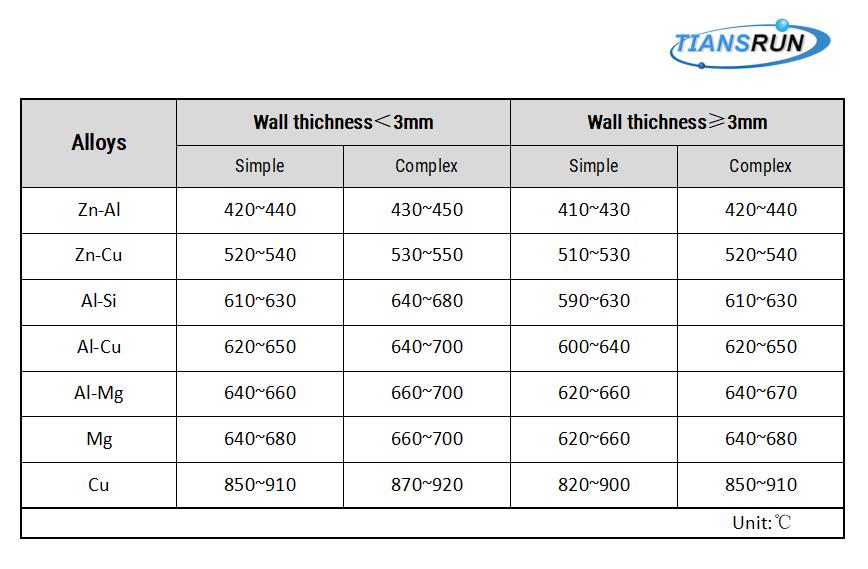
In general, the pouring temperature should be reduced as much as possible under high-pressure conditions, and even the liquid metal can be die-cast in a vicious “semi-liquid” condition. This can reduce the temperature fluctuation of the cavity surface and the scouring of the mold cavity by the liquid metal flow, prolong the service life of the mold, reduce the possibility of gas involvement and eddy current generation, reduce the volume shrinkage during solidification, and reduce shrinkage and porosity.
However, for aluminum alloys with high silicon content, if the temperature is too low, the phenomenon of free silicon precipitation will occur, deteriorating the processing performance. In addition, as the pouring temperature of molten metal decreases, its fluidity decreases correspondingly, but the pressure of die casting will increase the fluidity.
Therefore, within a certain range, the fluidity of the molten metal itself does not play a decisive role in die casting. The main factors affecting the fluidity of die casting are pressure and injection speed.
It should be noted that the higher the filling speed, the higher the temperature of the liquid metal due to friction. When the filling speed is 40m/s, the temperature of the aluminum alloy entering the cavity will increase by 8 °C, so when the filling speed is large, the pouring temperature can be appropriately reduced to ensure the quality of the casting.
The temperature of the die-casting mold refers to the working temperature of the die-casting mold. The die-casting mold should be fully preheated before use and kept within the calculated temperature range in the following formula:
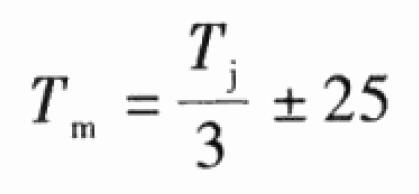
In the formula,
Tm – the working temperature of the die-casting mold (℃);
Tj – liquid metal pouring temperature (°C).
In the cycle of die-casting production, the heat balance when the heat absorbed by the die-casting mold from the liquid metal and the heat transferred to the outside world is equal, which is called the heat balance of the die-casting mold.
For small and medium-sized die-casting molds, the heat absorbed by the die-casting mold always enters the next cycle before it can be dissipated to the outside world. Therefore, a cooling device needs to be installed in the die-casting mold to adjust the heat balance of the die-casting mold.
Due to the large volume, large heat capacity, and long cycle time, the die-casting mold heats up slowly for large die-casting molds. At this time, there can be no cooling channels near the cavity, but only cooling channels are provided around the sprue sleeve to achieve a thermal balance of the die-casting mold.
Sometimes the cavity is complex, and the temperature difference between different parts is large, so the die-casting mold is provided with cooling channels and heating channels, thus forming a cooling-heating system to adjust the thermal balance of the die-casting mold. At this time, oil is used as a heating medium.