Evaluation of Die Casting Product
When we develop a product for a customer, we need to conduct a preliminary product evaluation. But the question is, why is an evaluation necessary?
The issue is this, some casting designers have a better understanding of the die-casting process and even have some experience in the actual die-casting production. But other designers may not have a perfect knowledge of the die-casting process.
Therefore, it is necessary for us to pass the evaluation and communicate with the casting designers to make the designed castings more in line with the requirements of the production process. The assessment of die castings is a necessary process for high-quality manufacturing products.
Today we evaluate the basic information of die castings. But subsequently, we will continue to update the blog to evaluate the rationality of the die casting design from different angles.
Top 14 Die Casting Information For Evaluation
The primary assessment of castings mainly includes 14 items of information, so let’s see what they entail:
1. Casting customer and name
Explain and classify the customer of the casting and the name of the casting. For example, the customer and name of the casting in the picture below
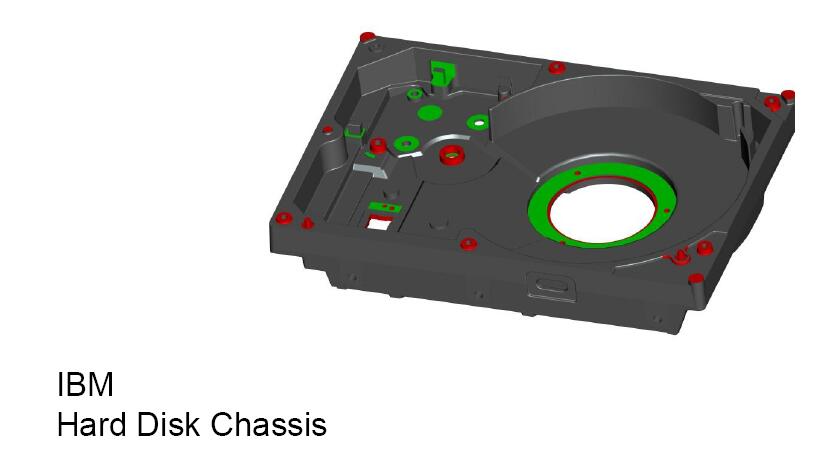
2. Overall dimensions of castings
Measure and record the maximum size of the casting outline, length, width, and height, marked in millimeters(mm).
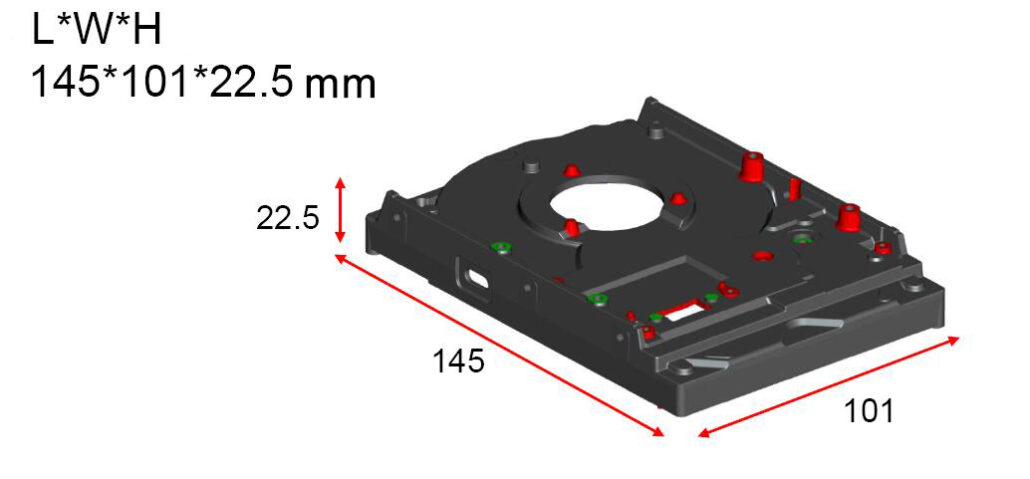
3. The material of the casting
Explain the material of the product. Then, evaluate according to the commonly used materials produced in the company.
If it is a new material, you need to pay special attention. Ask the right questions such as; for the new material, do we have the corresponding production capacity?
Check out a few materials that feature in the production.
- Commonly used aluminum alloy grades, ADC12, A380
- Zinc alloy No. 3 No. 5 No. 7
- Magnesium alloy AZ91D AM60
The material of this casting is ADC12
4. Calculation of casting weight
If the casting has a sample, the sample can be weighed and measured directly.
If the casting has a 3D drawing file, we can calculate the 3D mass of the product, and the unit of mass is generally in gram (g).
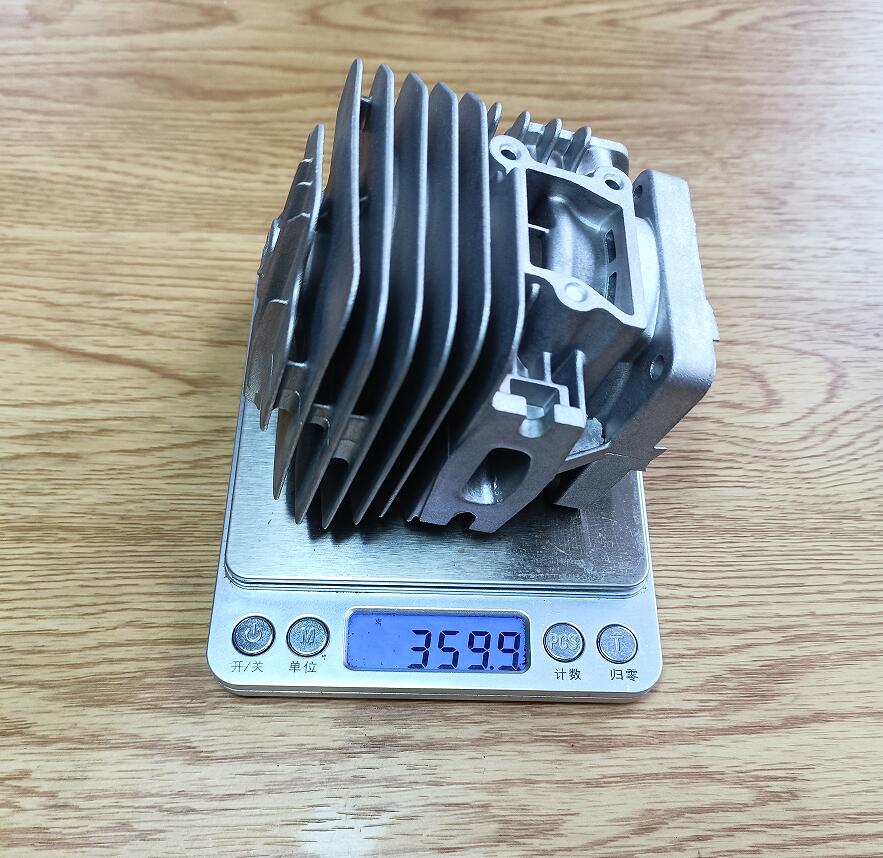
5. Die casting machine suitable for casting molding
The following are insights to help your selection of die casting machine
- Type of die casting machine: hot chamber die casting machine, or cold chamber die casting machine
- Tonnage selection of die casting machine: in this concept, you evaluate according to the requirements of product clamping force. According to the specific needs of castings, a comprehensive evaluation is crucial.
- The position of the injection center: Evaluate whether the injection position of the die-casting machine meets the requirements.
- Casting weight: Evaluate whether the maximum injection weight of the die-casting machine meets the requirements.
- Machine size: the machine size is vital, as it aids the installation of molds in the machine.
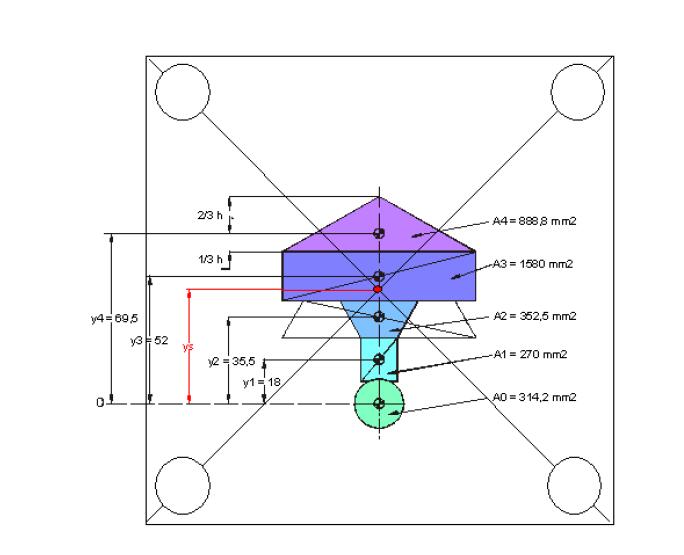
6. Recommended number of cavities for casting molding
If the machine capacity permits, it is necessary to evaluate the number of product cavities. This is a more sensitive issue. Generally speaking, an increase in the number of mold cavities can significantly increase productivity, but the failure rate of synchronous molds increases geometrically.
It becomes more crucial in the case of molds with sliders and hydraulic cylinders. Therefore, it is necessary to be cautious when evaluating, comprehensively considering economic and production stability.
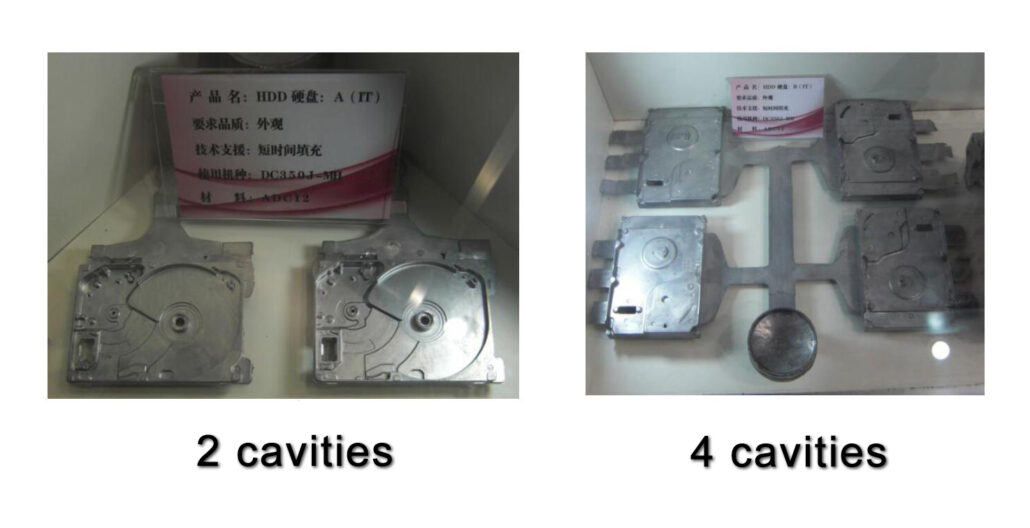
7. Average wall thickness of die castings
The average wall thickness of the die casting determines the setting of the die casting filling time, so this is critical data.
The wall thickness analysis of die-casting parts needs to be analyzed and completed with the help of software.
Generally speaking, the local wall thickness of magnesium alloy should not be less than 0.4mm. The actual thickness also depends on the distribution position and the size of the area.
Zinc alloy has good fluidity, hence suitable for products with small wall thickness, but if the product’s wall thickness is too small, it is easy to form the air in the thick wall.
The recommended wall thickness data is as shown below
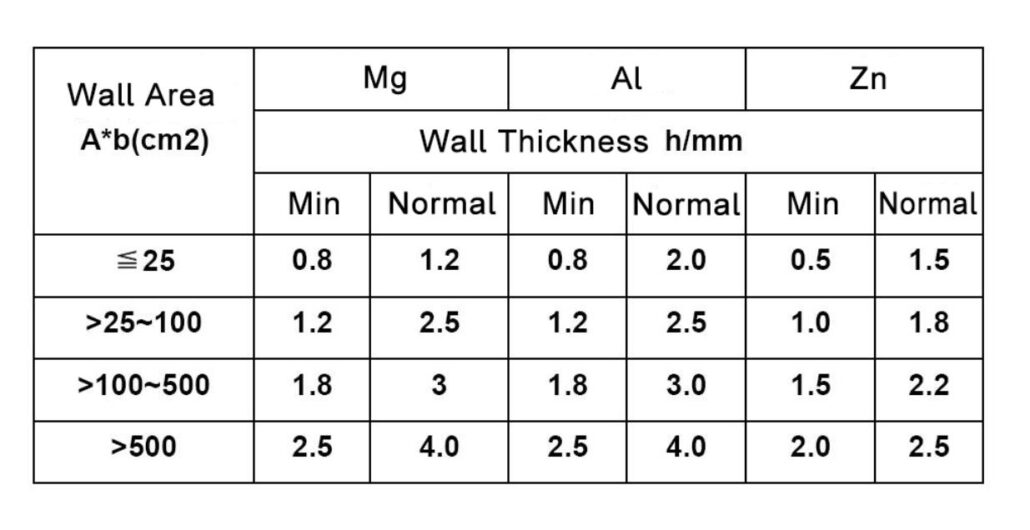
8. Minimum wall thickness of castings
The average wall thickness and minimum wall thickness of the casting will determine the filling time of the casting. Therefore, the minimum value of the casting wall thickness and the associated area’s size is critical, requiring special attention when evaluating the casting.
The minimum wall thickness area needs to consider its filling performance to select the appropriate die-casting parameters. For challenging areas to fill, you need to communicate with the designer. If the wall thickness of casting is in uniformity, it will improve the quality and production efficiency of the casting.
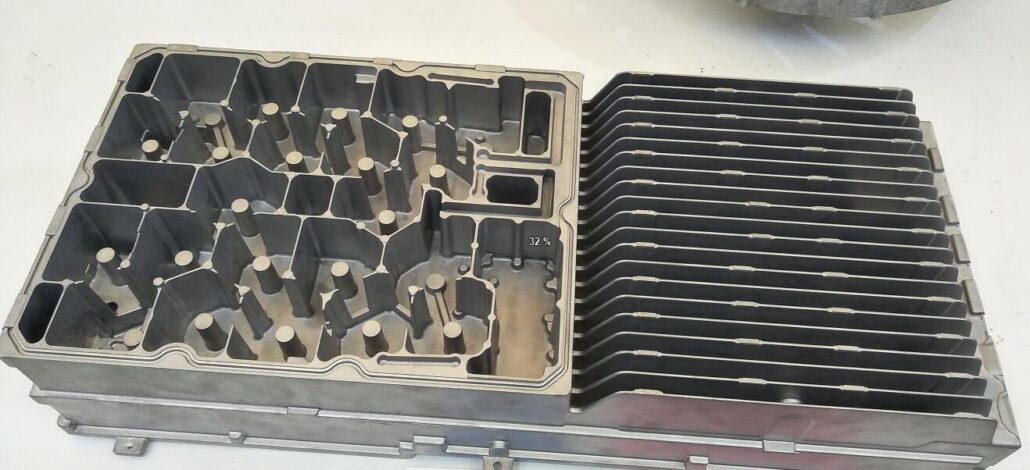
9. The movable mold side and the fixed mold side of the casting
For most castings, you can clearly determine which side is the movable mold side and which side is the fixed mold side. However, some castings are more complicated or have appearance requirements, such as whether the position of the ejector pin affects the appearance, which needs confirmation from the customer.
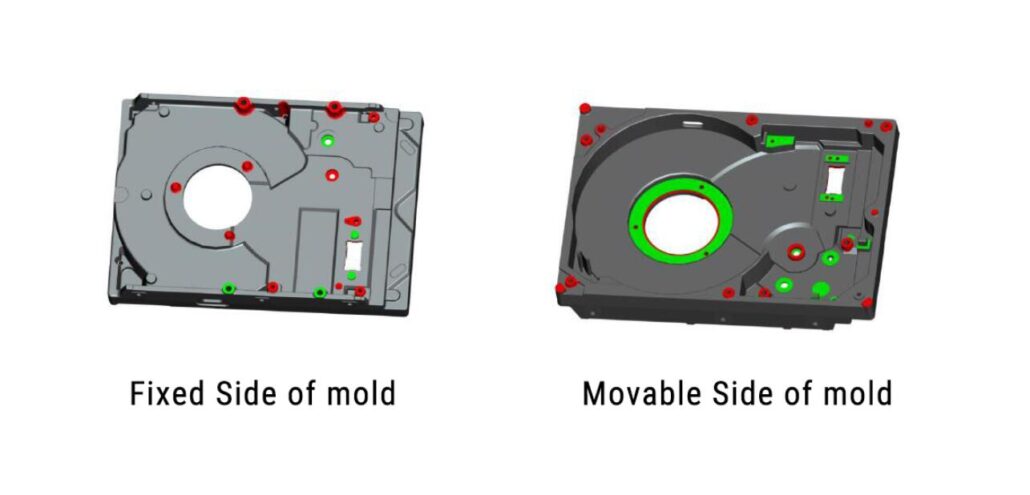
10. Flatness requirements of castings
The flatness requirements of castings often require significant attention, such as the flatness requirements of a mobile phone or notebook casting.
Or the flatness requirements of a large thin-walled part of an automobile need to be carefully considered. If the flatness is out of tolerance, it will directly affect the assembly. Therefore, in the process of die casting evaluation, the flatness requirements are generally communicated with the designer in detail.
In terms of the flatness of the casting, three distant points on an infinite plane help establish a measurement datum plane. The flatness measurement method and reference plane must be evaluated and communicated during design.
The figure shows the standard tolerance of flatness of all alloy castings.
Design guidelines that help achieve flatness include;
- All draft angles (faces, protrusions, ribs, grooves, and bottom plane slopes) should meet the standard slope or have a larger slope.
- Large bosses and cross-sections will cause shrinkage or deformation, so it’s best to avoid setting them directly on the plane.
- The change of the section should be gentle, and there should be a suitable transition of the fillet to avoid stress concentration and shrinkage deformation
- In a bid to obtain good flatness, uniform wall thickness is critical. Changes in wall thickness such as ribs and bosses will affect flatness.
11. Whether the casting has appearance requirements
Confirm whether the casting has appearance requirements and the size of the appearance area. Also, confirm the coating type of the appearance surface of the casting. The ability of different coating types to cover surface flaws varies greatly.
Confirm the casting surface roughness requirements, especially the surface roughness of the sealing surface. This requirement is closely related to the size of the mold life. The higher the roughness requirement, the shorter the life of the mold.
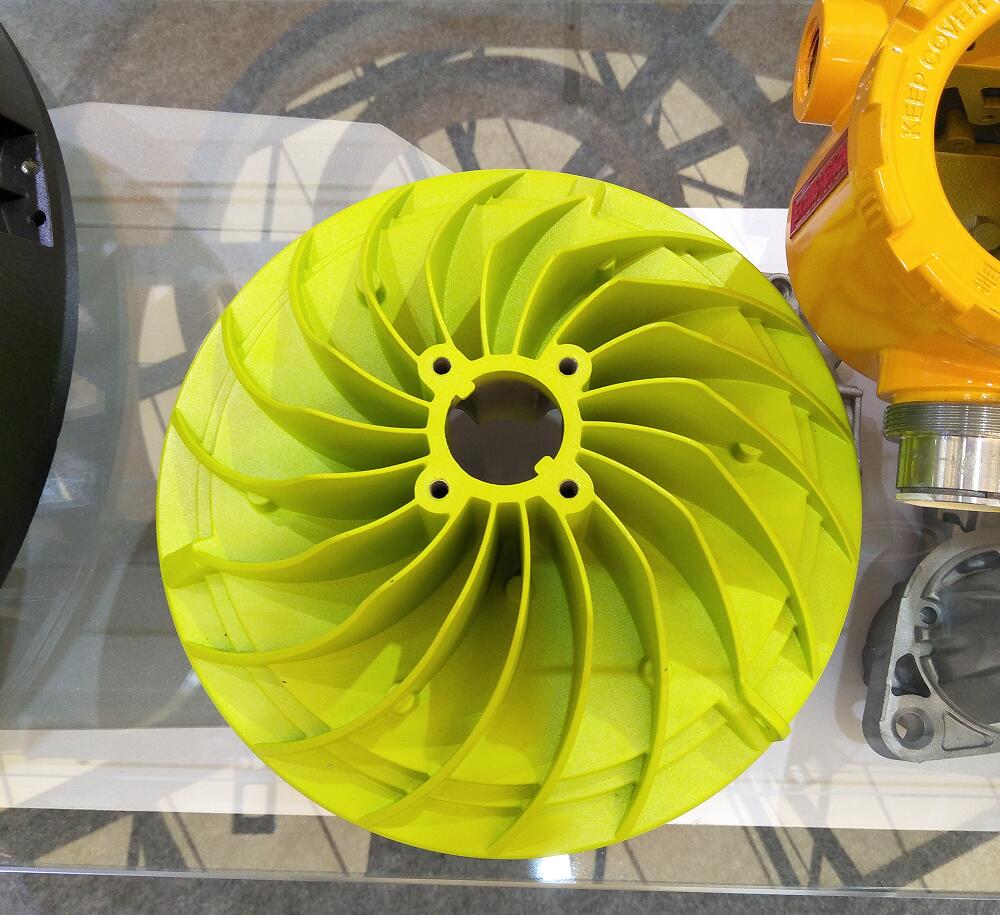
12. Mechanical performance requirements of castings
The tensile strength, yield strength, ductility, and grain size of the casting after heat treatment determine the mechanical performance of the casting. Some auto parts have detailed mechanical performance requirements, and we need to consider whether the existing process flow can meet these requirements. Correspondingly, the higher the general mechanical performance requirements, the higher the porosity requirements of castings.
13. Requirements for leakage of castings
General airtight castings, such as gearboxes, oil pans, engine housings, battery packs, and other die-casting parts will require leakage testing.
We need to pay attention to casting leakage requirements to evaluate the overall yield of castings. Under the specified gas pressure, the amount of gas leakage per unit time. The side leakage pressure is 0.3bar, the leakage volume is 40ml/min, and the ambient temperature is 20°. We inspect all castings.
It’s best to use a dedicated side leakage checker suitable for both dry and wet purposes.
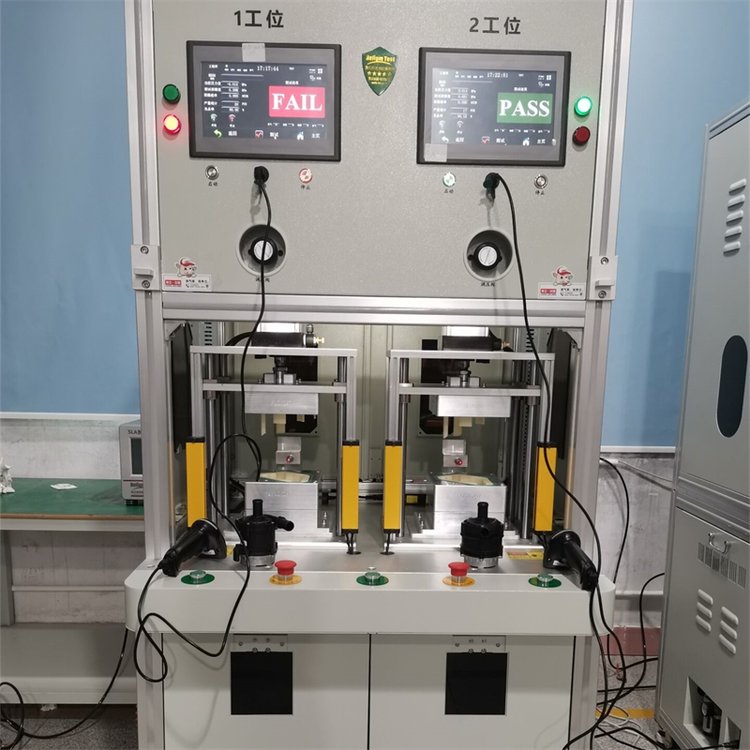
14. Cleanliness requirements
Some die castings have cleanliness requirements, such as the cleanliness of the shell surface. Let’s see a few things to note.
- Pollution degree shall not exceed 5mg/1000cm2, or 1.5mg/kg
- The particle size of any debris shall not exceed 600um, and the particle size area shall not exceed 0.4mm2
- You need to remove all residues after processing.