Casting Evaluation - Rib
Ribs are a vital part of the design of die castings. A die casting design that involves the reasonable and clever use of ribs can greatly improve the mechanical properties of die-casting parts. It also reduces the use of materials and provides a measure of convenience for die-casting production.
Therefore evaluating ribs should not be neglected for a successful die casting process. In a bid to convey the significance of ribs for die casting, we will section this article into six parts:
- Ribs can reduce the use of materials
- Ribs can increase the strength of die castings
- Ribs can improve fluidity
- The usage of ribs to set the inner gate
- The usage of ribs for heat dissipation
- The regular size of ribs
1.Ribs Can Reduce the Use of Materials
The use of thin walls and ribs can reduce the weight of parts, make the product lighter, and reduce the possibility of defects. If you want to double the stiffness of the part, consider increasing the thickness, and the material has to increase by 25%. If you rely on stiffeners, the material will only increase by 7%.
When the original design wall thickness is 36mm, and the improved wall thickness is 7mm, the improvement is beautiful and reduces the weight of the product.
2.Ribs can increase the strength of the casting
When designing our castings, we need to avoid the flat design, increase the castings’ strength, and reduce the castings’ deformation utilizing reinforcing ribs.
Case one
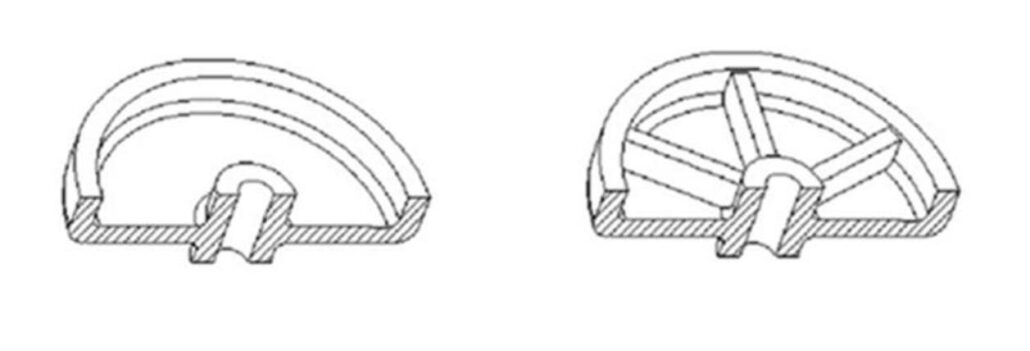
Case two
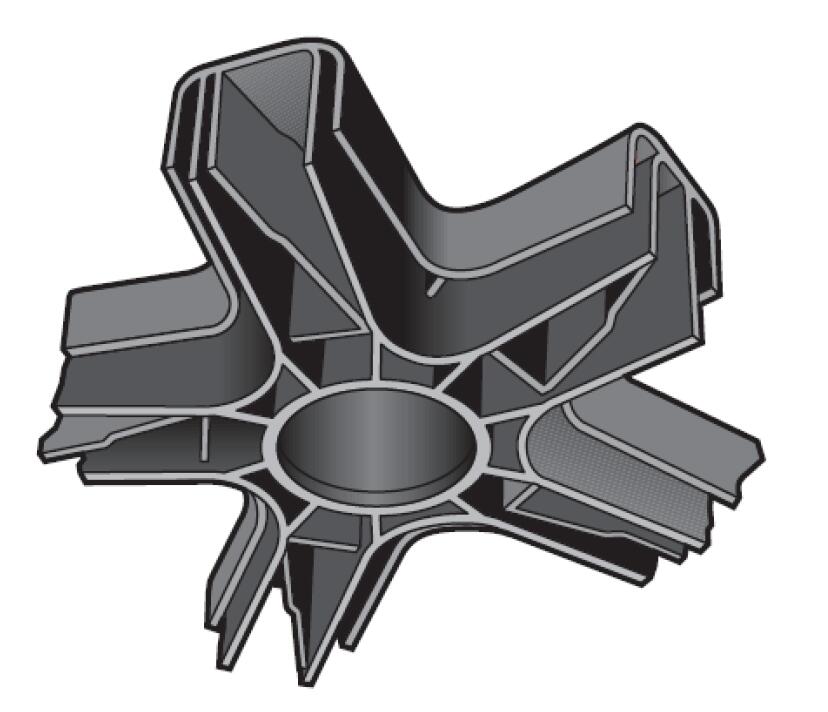
The U-shaped cross-section design and auxiliary diagonal reinforcement ribs significantly increase the rigidity of the product.
Case three
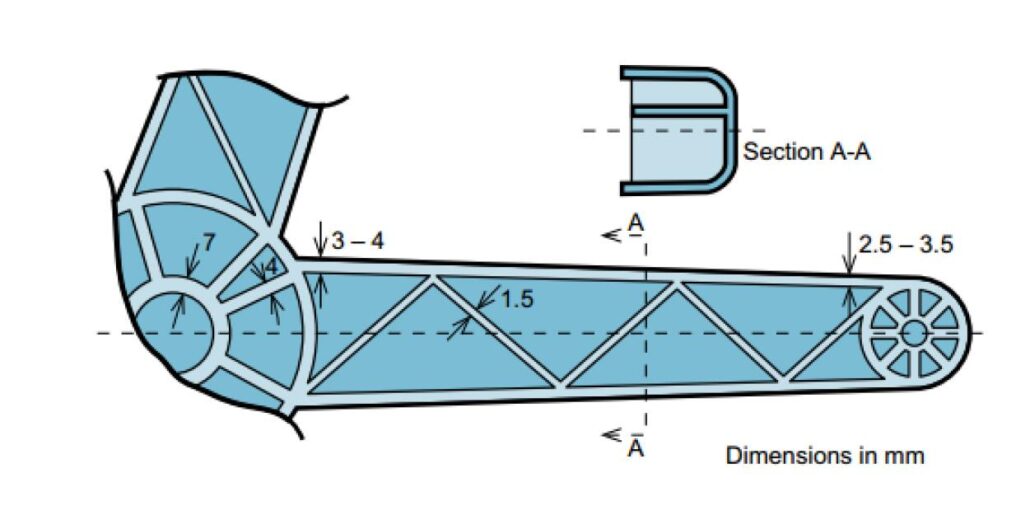
Many beams that require high rigidity will have their design fit into this structure.
Case four
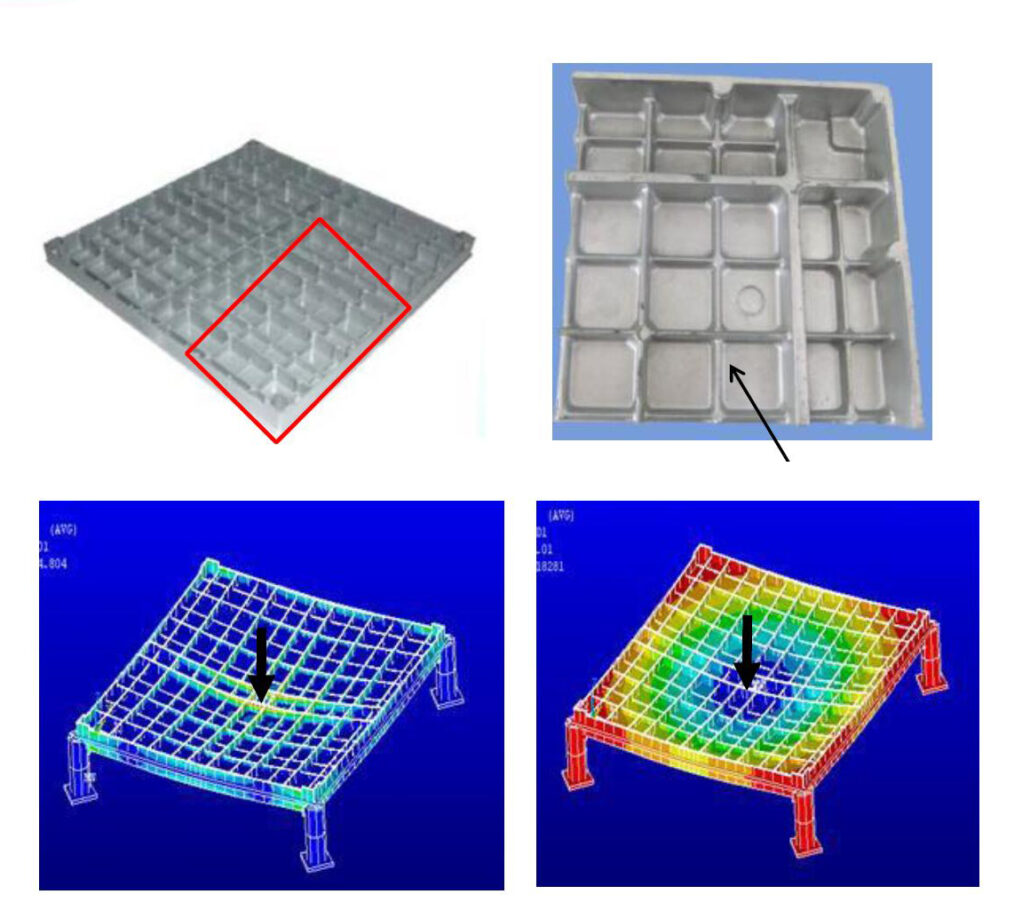
This is an aluminum alloy floor tile manufactured by die-casting. This kind of floor tile requires that the amount of deformation generated under external force is as small as possible. It also requires a higher limit load.
Stiffeners cover this product, and the stiffeners are cross-distributed in a square or rectangular shape. It is now evident that the rigidity of rectangle and square is the best.
Case five
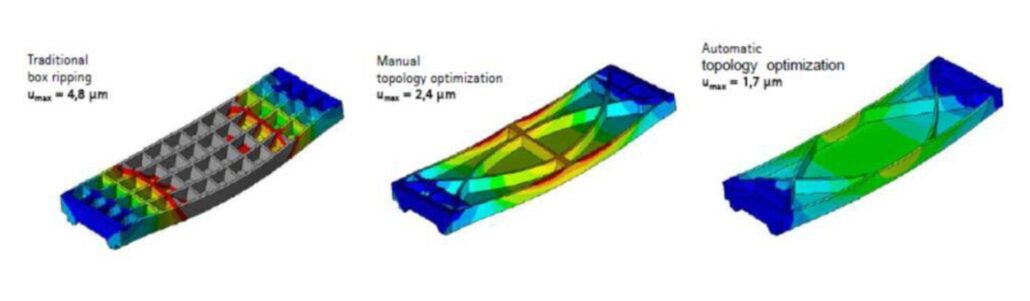
Some castings have very high flatness requirements. In order to improve the flatness of the castings, it is the best plan to install stiffeners on the die castings.
There are various designs of stiffeners, such as squares, rectangles, and intersections at multiple angles, and the final flatness is different.
As shown in the figure, large, intersecting ribs can provide better flatness.
Case six

This is the car battery box designed by the German BMW company:
- Many stiffener structure designs are used on the outside of the box;
- At the junction of many ribs, one employs the ring structure for connection, which cleverly avoids the problem of uneven wall thickness.
Please refer to the figure below to analyze the red model for details. The ribs are connected, and the wall thickness is uneven. The design of the blue model avoids this problem.
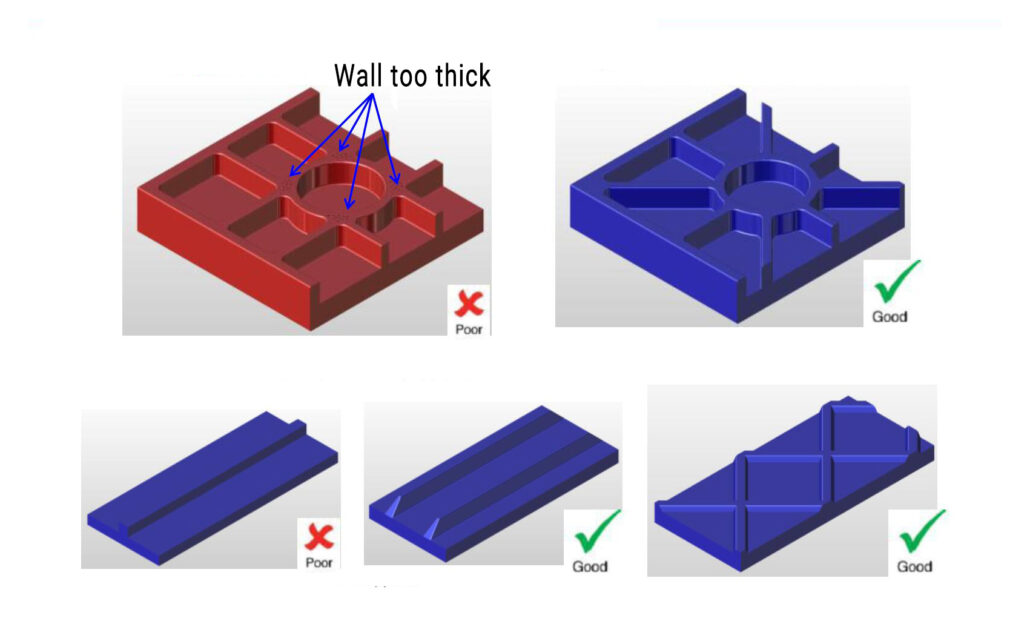
Avoid sharp right angles for the corners of the sidewall ribs, and use oblique angles instead.
Case seven :
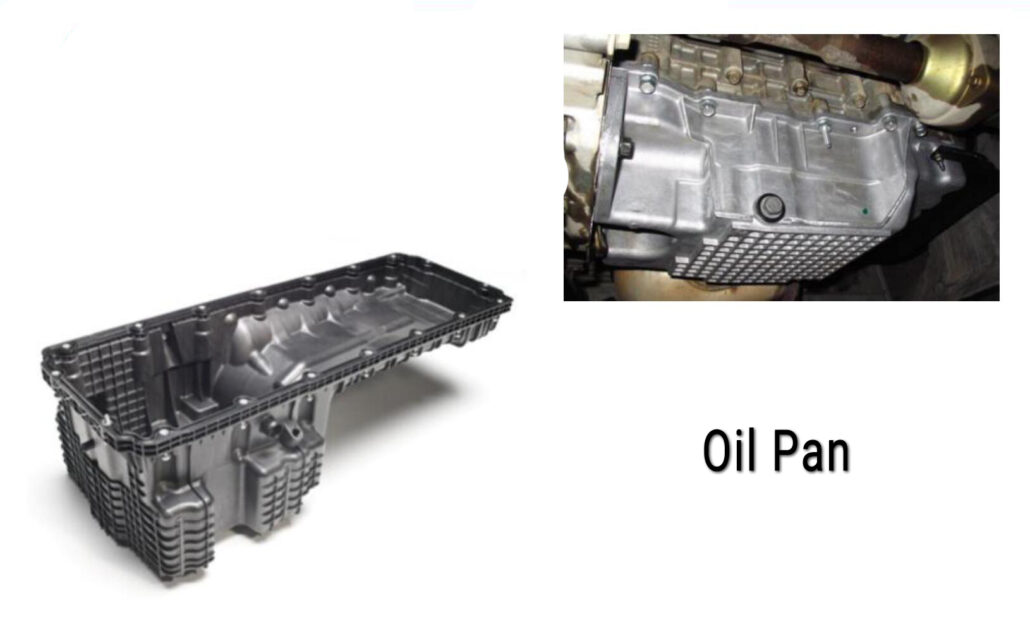
The oil sump is located at the bottom of the vehicle and should have sufficient strength and rigidity in the design of the mechanism. As a whole, the design adopts the structure of auxiliary ribs of the box body, which considers the needs of strength and heat dissipation.
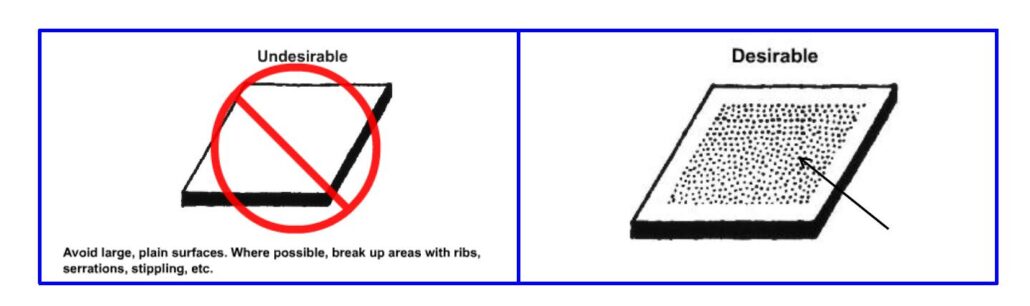
In the design of die-casting parts, it is necessary to avoid the design as a complete plane. Instead, increase some ribs, design some high and low bumps, and make the large flat surface of the die-casting part rough, thereby improving the fluidity of the molten metal.
3.Ribs Can Improve Fluidity.
Case one
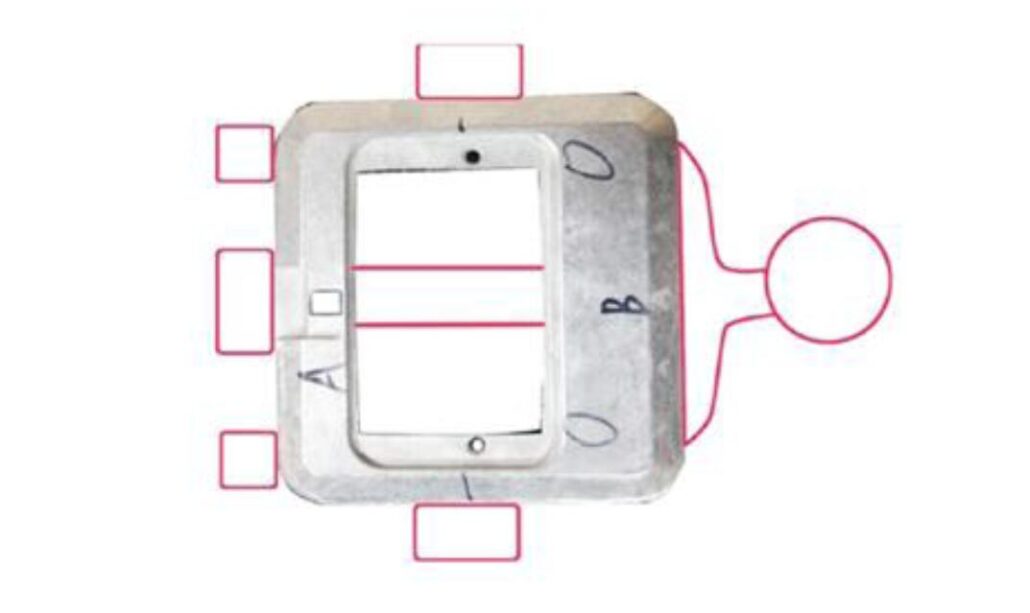
In the first die-casting production, the casting is always not good at the top and middle areas. This is because there are many cold barriers and shrinkage holes.
After communicating with the customer, we see that the middle area of the casting does not belong to the functional area; hence we can add a rib. Use ribs to improve the fluidity of molten metal, and then the problem is solved.
Case two: Platform plus boss column
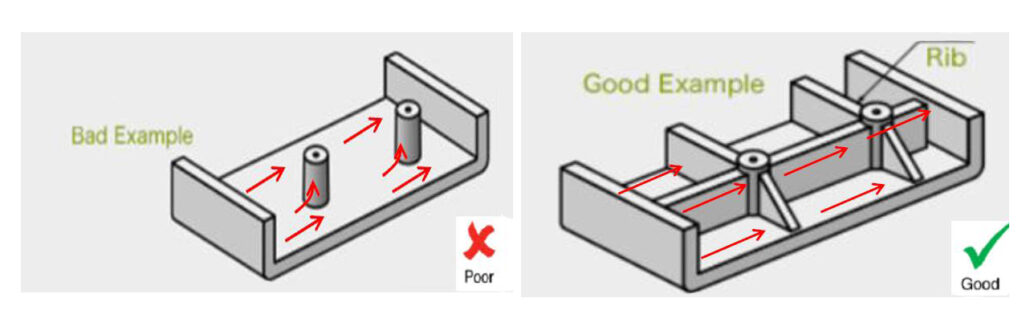
What is the filling problem with this product?
During the filling process, the molten metal flows along the plane. The molten metal is filled from the bottom to the top when filling the boss. The air inside the boss is compressed on its top; then the boss head becomes the end of the metal filling, which is the place where the defect occurs.
Improvements:
As shown in the figure, design ribs on the boss so that while the molten metal is filled smoothly, the air inside the boss goes out easily.
But there is also a particular disadvantage: hot spots are easy to form at the position of the boss post.
The direction of the ribs is generally set along the filling direction of the molten metal to assist the flow of the metal broth.
Case three
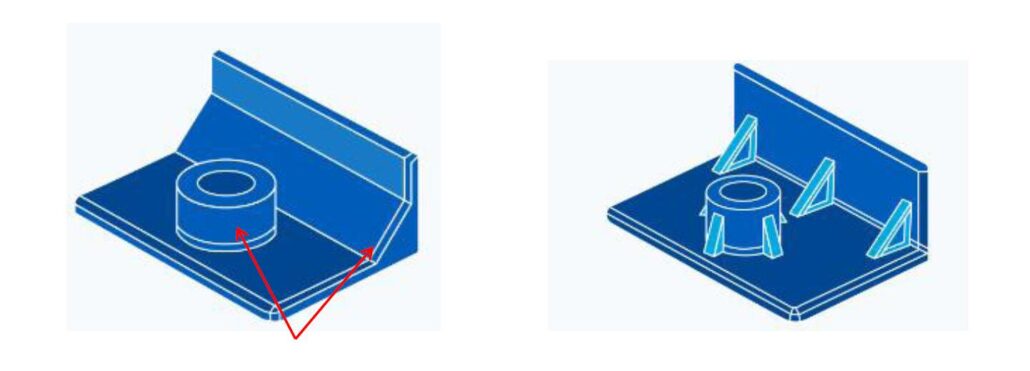
Poor design, the wall thickness of the right angle is too thick, and I want to rely on increasing the thickness to increase the strength, which is a waste of material.
Moreover, the boss is set separately; the filling effect is poor, but the strength is not high.
The picture on the right shows the improved model. A lot of material can be saved by adding ribs on the right angles to increase the strength of the die-casting parts. In addition, the increase of ribs on the boss can improve the filling performance of the molten metal and increase the boss’s strength.
Case four
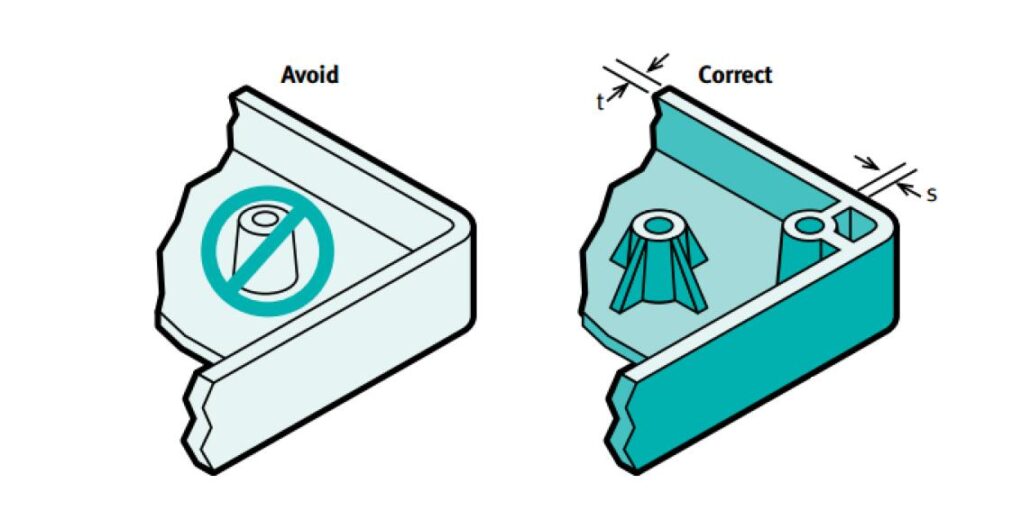
Increased ribs on the corner bosses are also to improve fluidity.
In the process of casting structure analysis, attention is crucial to the design of these structures, and one should point out the non-conformities in time. Otherwise, it won’t be easy to modify in the production stage. Therefore, the evaluation of the casting structure should be cautious and meticulous.
Case five
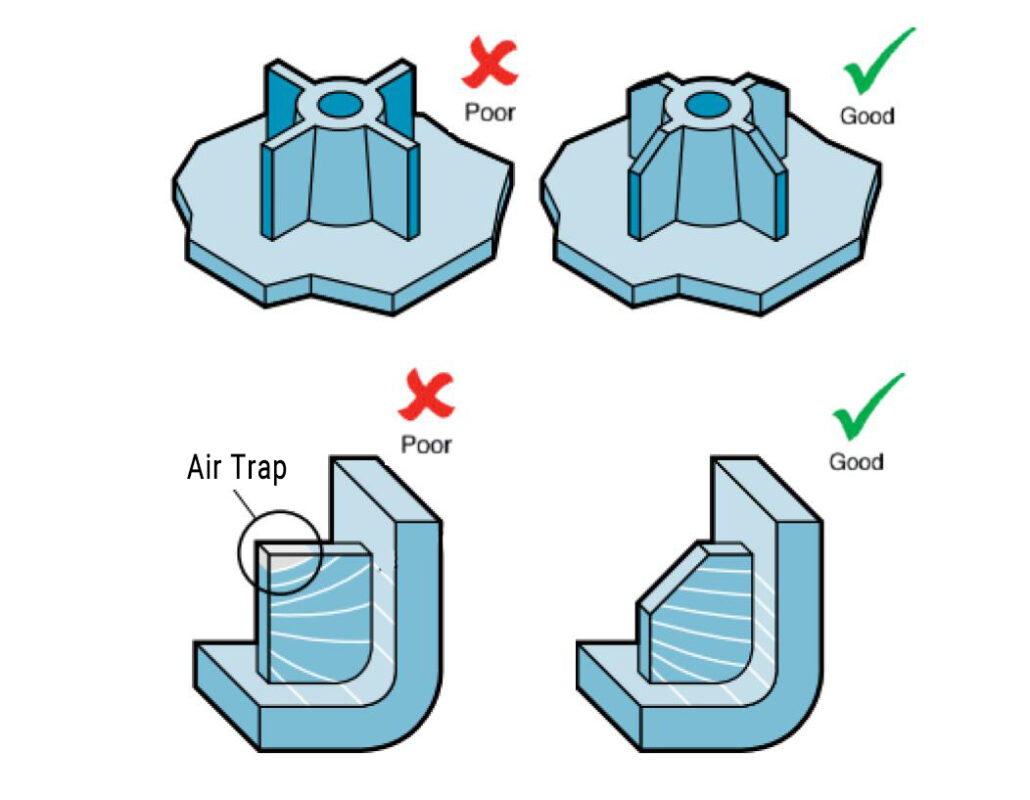
When designing the shape of the rib, generally avoid generating right angles, the corners will entrap air and lead to defects. The common practice is to make a chamfer, as shown in the figure.
Case six
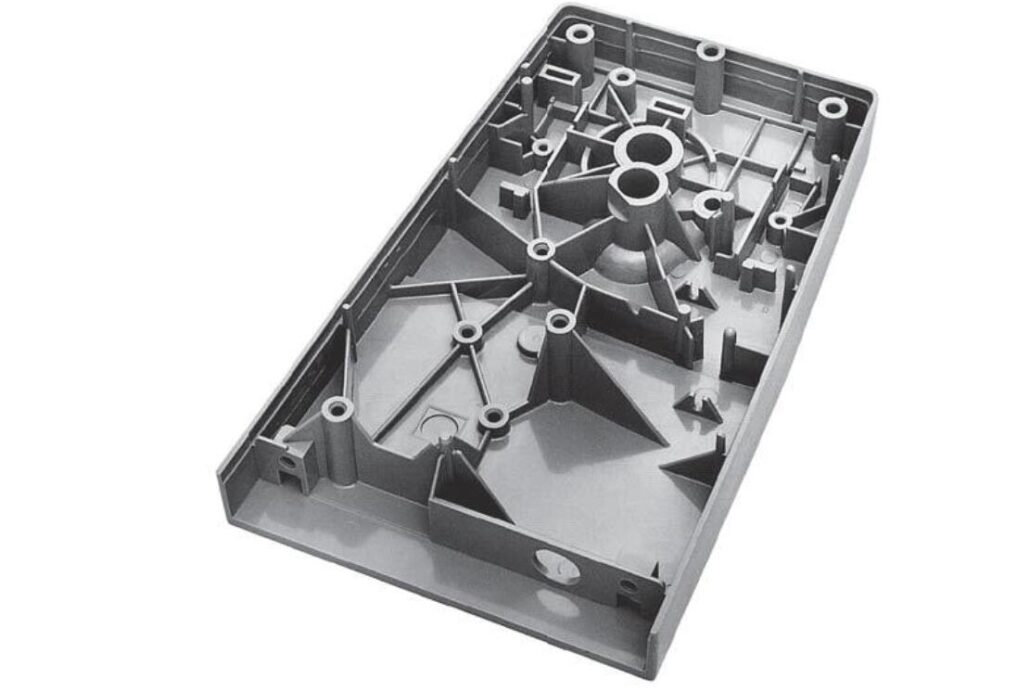
This is a die-cast part of a notebook computer, and the structural design of the ribs can is clearly visible.
Case seven
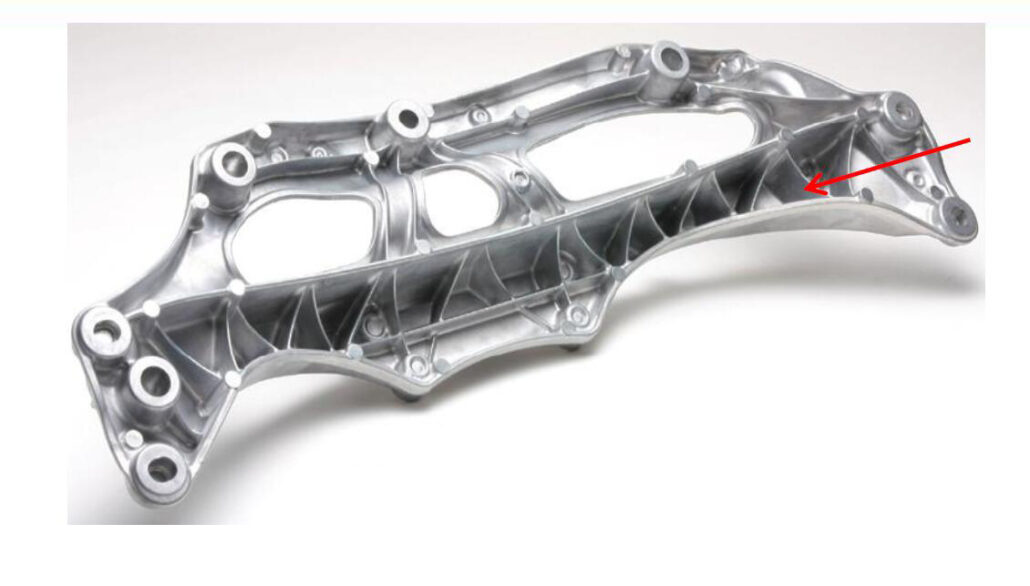
The picture shows the bracket of a car engine, in which the ribs are designed and used very well. These stiffeners increase the strength of the entire bracket and fill channels for molten metal during the molding process of casting. Therefore, we must pay attention to the design of stiffeners, including structure, location, direction, etc.
Case eight
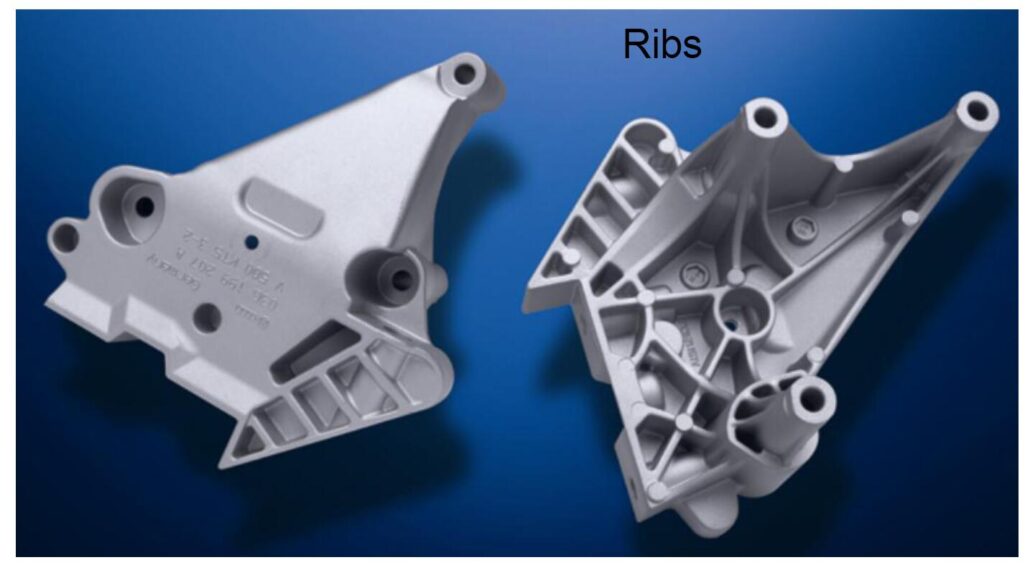
Design of Reinforcing Ribs for Vibration Loaded Castings
Case nine
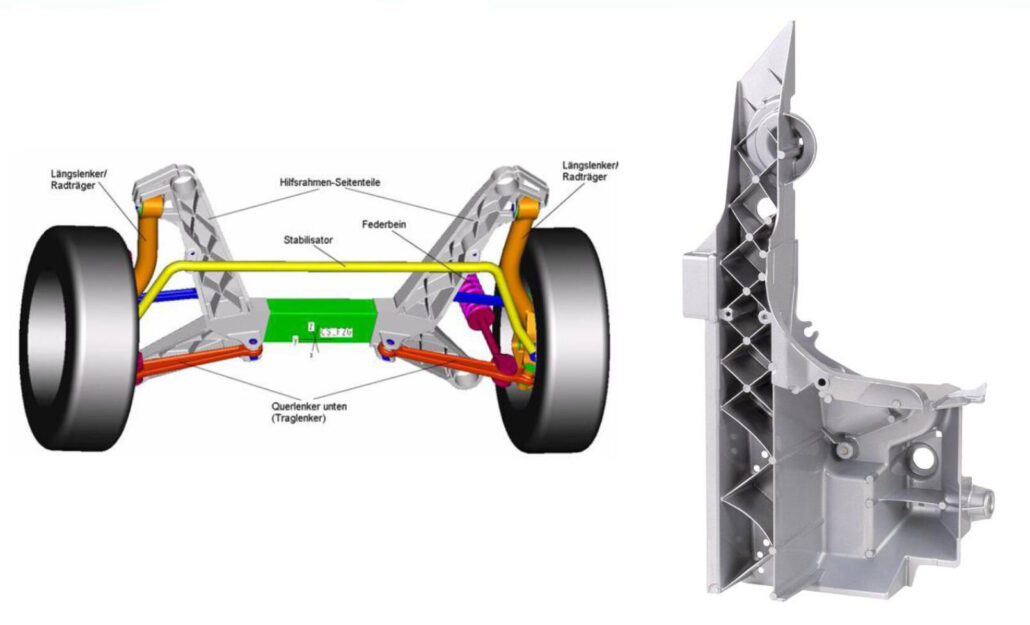
Reinforcing rib structure of impact load casting
Case ten
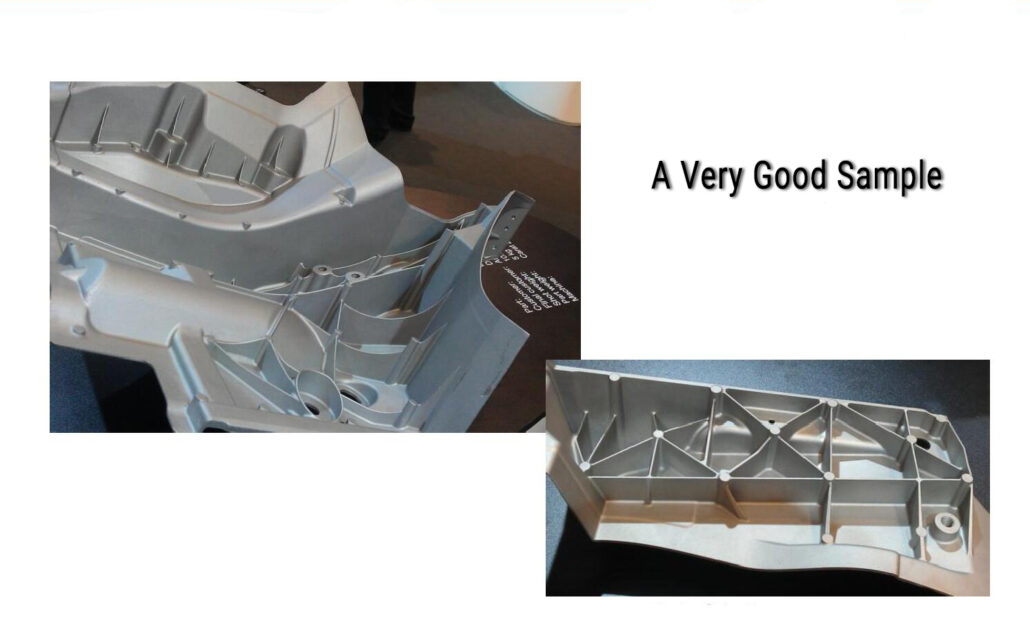
This is a large thin-walled casting produced by a German die-casting company. Its structural feature is that the overall wall thickness is very thin, between 2.5 and 3 mm. There are many changes in the plane, and the rib structure is mostly used, and the rib changes in multiple shapes with the shape of the die-casting part.
This die-casting part plays a good role in the reinforcement structure and is a model for design and structure evaluation personnel to learn.
4.The Usage of Ribs to Set the Inner Gate
For this cylindrical product, the gate was initially designed at the bottom, but the effect was not good. The inner gate is set from the cylindrical surface of the product. When the inner gate is cut, the product’s surface will be damaged. It is recommended to add a rib on the side as an inner gate. It is not only convenient for filling molten metal but also more beautiful.
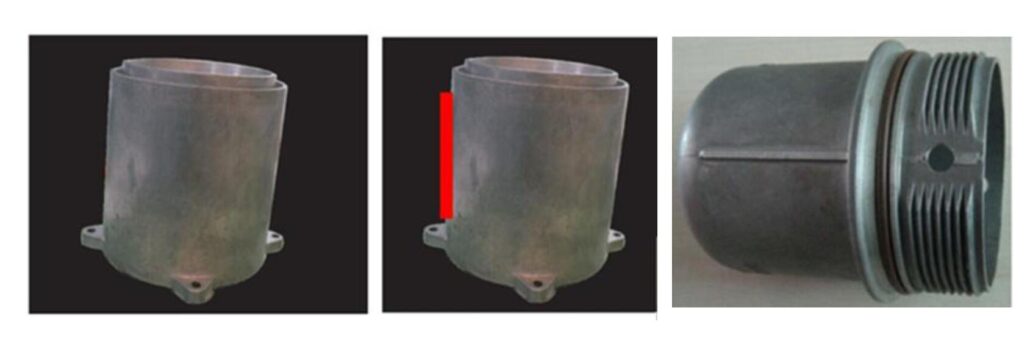
5.The Usage of Ribs for heat dissipation
Many products work in a high-temperature environment, and usually, some ribs can be added to the surface of the product to realize the heat dissipation function.
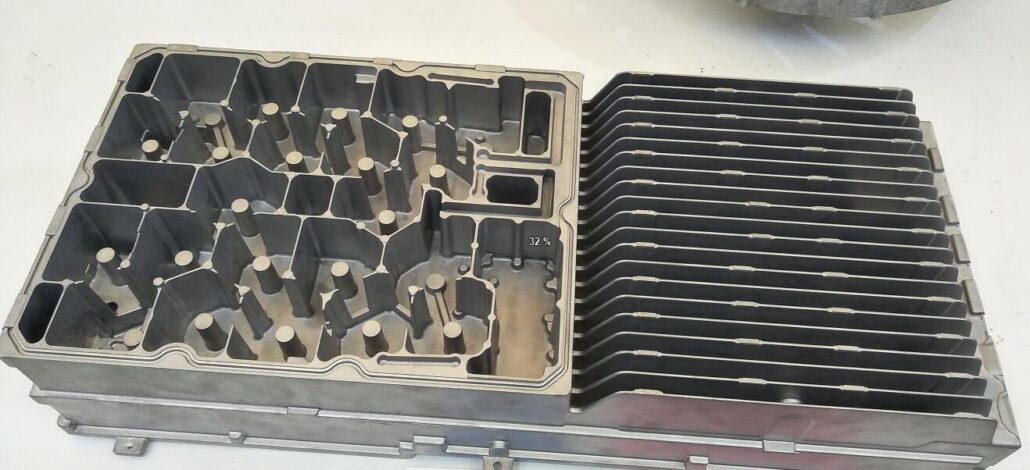
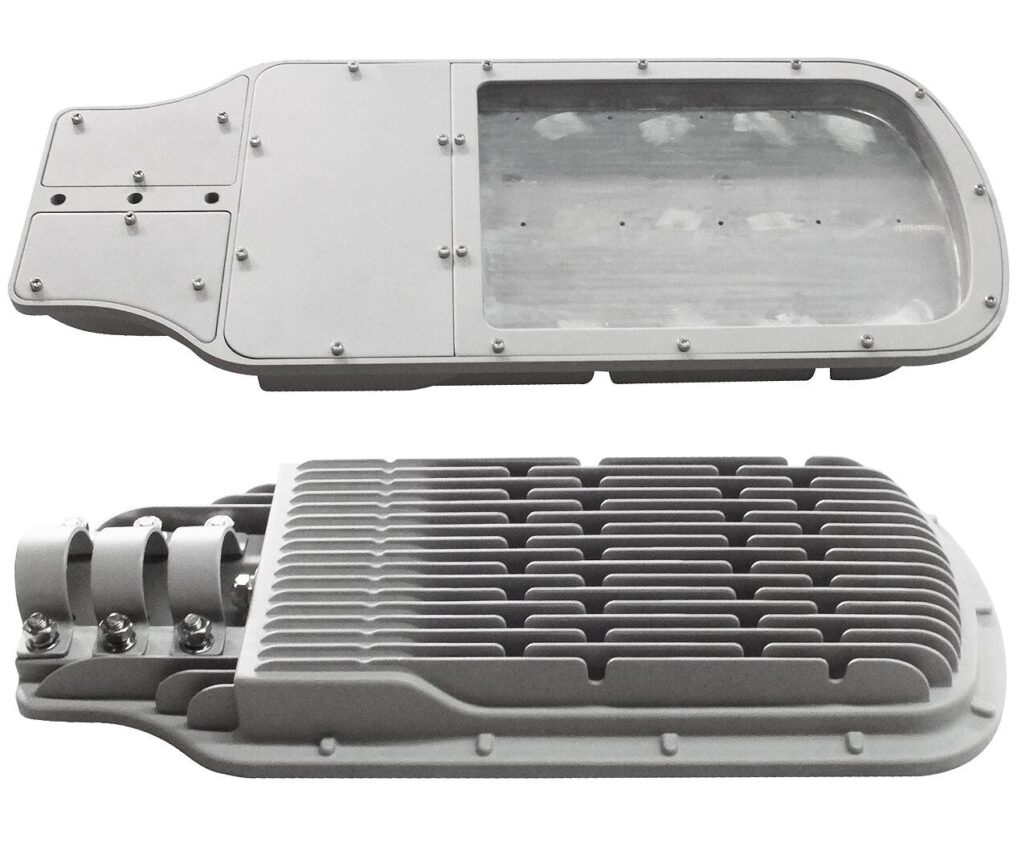
6.The Regular Size of Ribs
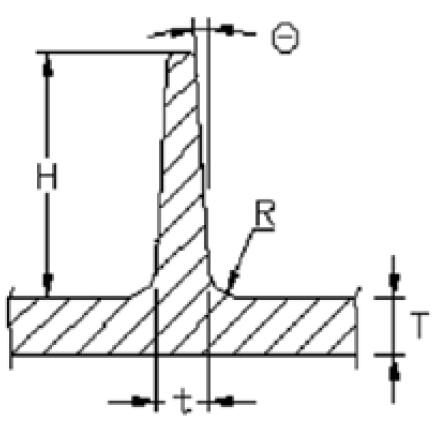
- The thickness of the root of the rib is generally not greater than the wall thickness here, generally between three-half to four-thirds of the wall thickness
- The demolding angle of the ribs is 1°~3°
- The roots of the ribs should be rounded to avoid sharp changes in the cross-section of the parts, and at the same time, assist the flow of molten metal, reduce the stress concentration at the roots of the ribs, and improve the strength of the parts. The size of the fillet is generally close to the wall thickness here.
- The height of the stiffener generally does not exceed five times the thickness of the stiffener.