Casting Buyer Series 3 - Die Casting After Treatment A
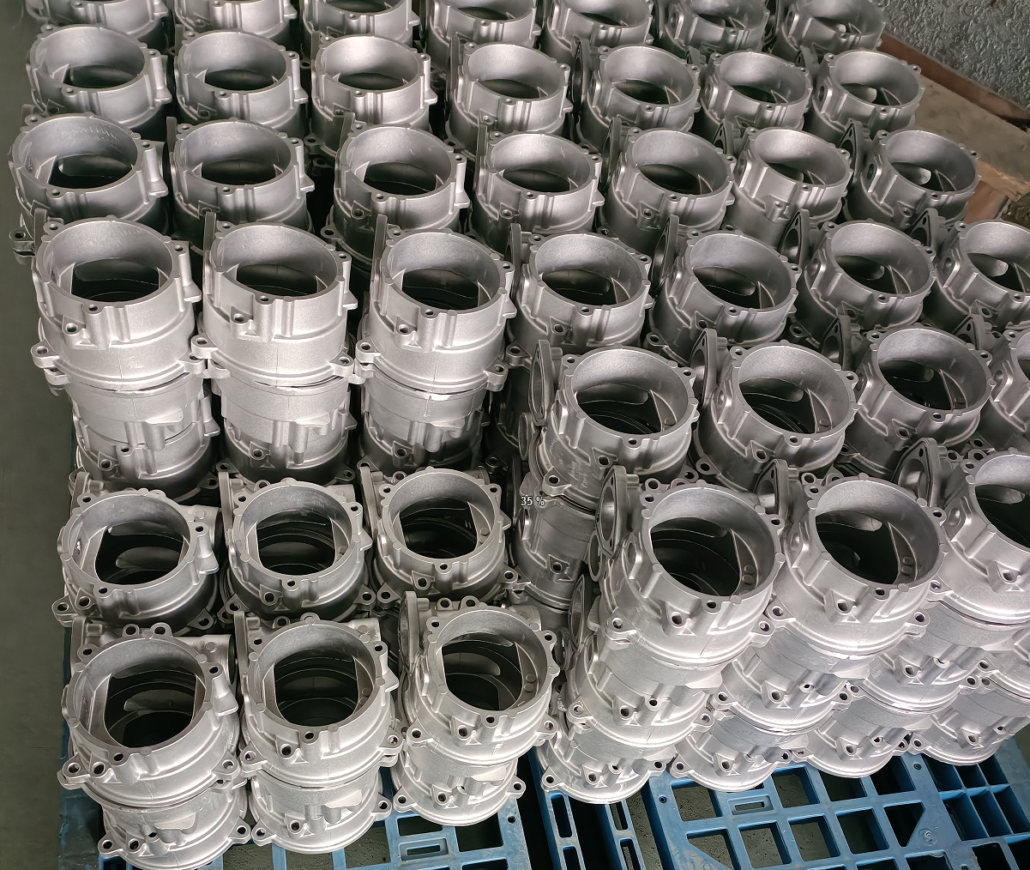
After the die-casting, we take the die-casting parts out of the machine and need multiple processes before they can be used. These processes include:
- Removal of runners, overflows, flash
- Removal of burrs
- Clean the surface
- Machining
- Infiltration
- Heat Treatment
- May require surface treatment such as shot blasting, plastic spraying, painting, electroplating, oxidation
After these processes, the die casting becomes the final product and is fit for delivery to customers.
1.Trimming
Deburring has now become a more critical link in die casting. Deburring requires a lot of labor, and now personnel wages are getting higher and higher. However, deburring is also developing in the direction of automation.
After removing the die casting from the machine, the first step is to remove the gates, runners, overflows, and flash. You can do this manually or with a trim press.
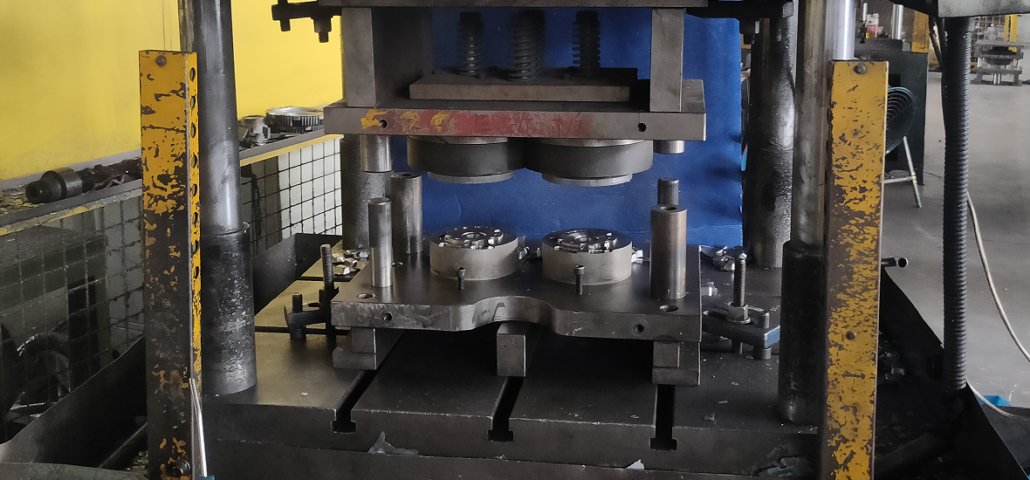
The trimming machine is a kind of hydraulic press, which is usually divided according to the tonnage. The larger the tonnage, the larger the machine size. Usually, the trimmer is between 10 tons and 300 tons.
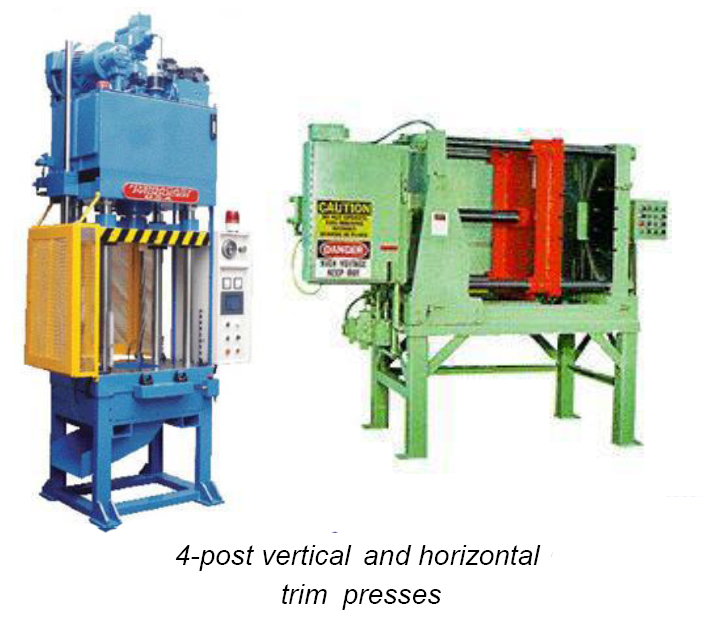
There are two types of edge trimmers: vertical and horizontal. The typical vertical type is shown in the figure below, with four columns and a workbench.
There is an oil cylinder on the top of the machine, and the oil cylinder controls the upper plate to move up and down to provide power for trimming. T-slots or holes are arranged on the table to hold the trim mold.
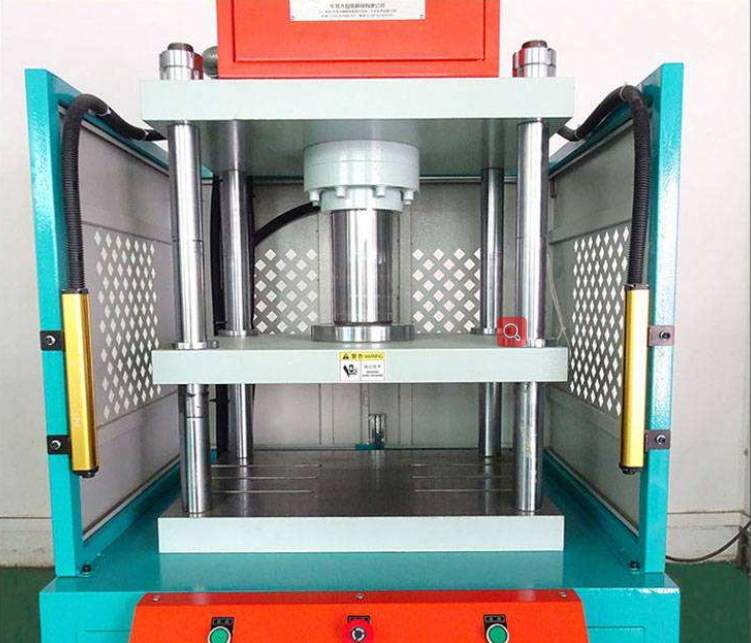
Trimming dies of die casting products are similar to punching dies and are used to cut gates, runners, and slag bags of die castings. After conventional edge trimming, the product needs to be taken out of the mold after edge trimming. It can also be designed to fall from under the mold into a collection bin or conveyor.
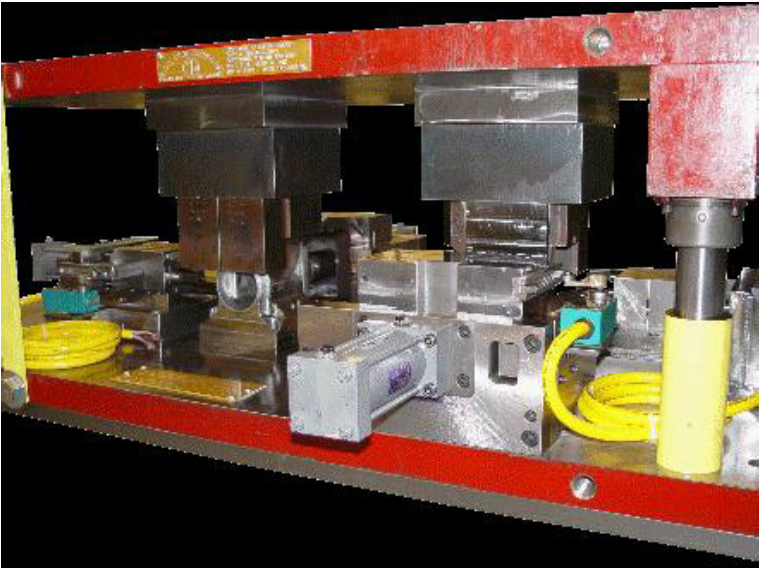
The trimming die can also be multi-cavity. For example, use multiple slides to punch the cored holes inside the casting. You can also combine other post-processing steps with trimming, such as punching, reaming, drilling, etc.
Advantages of edge trimmers:
The edge trimmers have the following advantages.
- Can improve the consistency of the product (consistent);
- Reduce labor costs;
- Reduce waste due to poor flash removal
- A short production cycle reduce product accumulation
- Casting quality check is possible with a built-in function
Disadvantages of edge trimmers:
- Increased costs, including the cost of the trimming machine and the cost of the trimming die
- Regular maintenance of trimmers and trimming dies are required, which also increases costs
Automatic trimming
The die-casting parts can be put into the trimming machine by the robot and then taken out after cutting. Advantages of using robots include further reduction of labor costs more consistent product trimming.
Disadvantages of using robots
- Robot-friendly automated trimming dies are more expensive
- Automatic trimming die will increase the failure rate
- The accuracy of parts will deteriorate after long-term use of the automated cell
- Some delicate parts may be damaged
Defects of poor trimming
When performing the trimming operation, it’s best to do it appropriately. Otherwise, it will lead to some defects. For example, see some of the defects below.
- There is material left in the trimming die, which will cause concave damage to the casting during the subsequent trimming
- Circular holes are shaped, or the outer surface is bruised
- Residual waste in the punching hole
- Casting bent or chipped
2.Shot Peening
Shot blasting is a process that uses high-speed moving projectiles to impact the surface of the casting continuously and implants compressive stress on the surface of the casting to improve the fatigue strength of the casting.
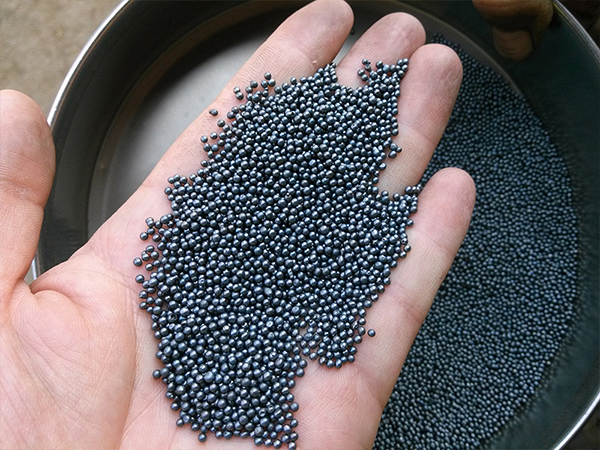
Why use shot peening?
- Shot peening can remove some small flash and burrs on the casting
- Can remove blemishes and micro-cracks on the casting surface to ensure a good casting appearance
- Shot peening can enhance surface adhesion and assist subsequent painting or plastic spraying processes
There are generally two ways to accelerate projectiles. One uses centrifugal force to accelerate projectiles, also known as wheel blasting. Shot blasting is widely used for surface treatment of die castings, and the cost is very low. The second is the use of compressed air to accelerate the projectile, often called shot peening or sandblasting.
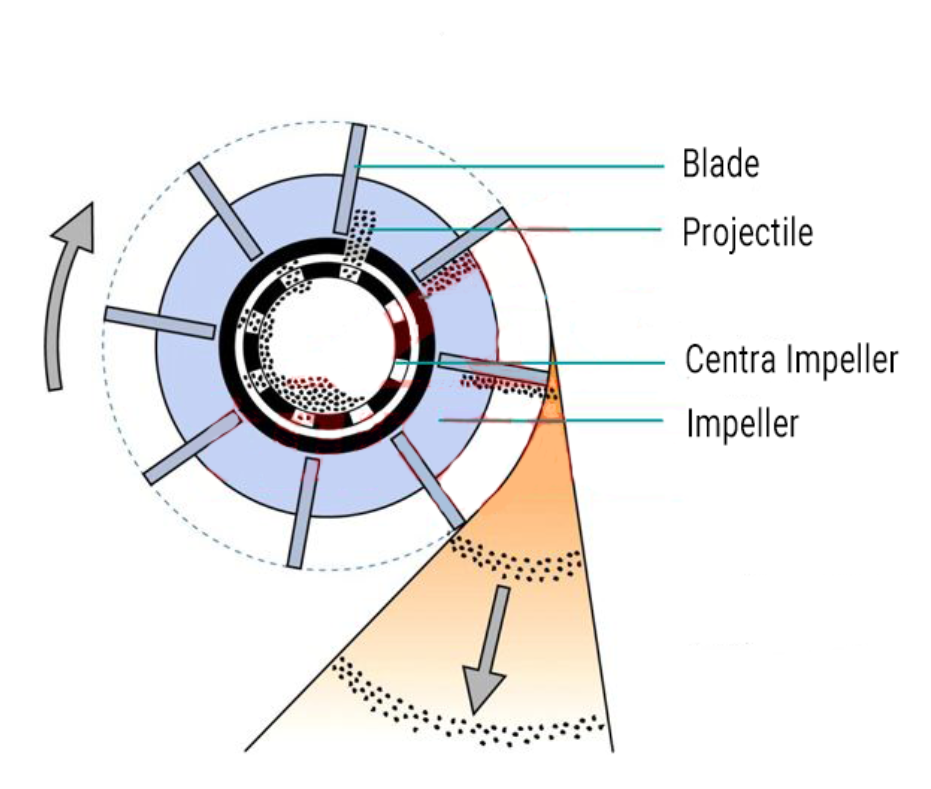
The principle of shot blasting
There is a high-speed rotating impeller in the shot blasting machine, and there are many blades on the impeller. The projectile enters the center of the impeller through the feed port. Driven by the blade, the projectile is thrown out of the blade at high speed and hits the surface of the casting.
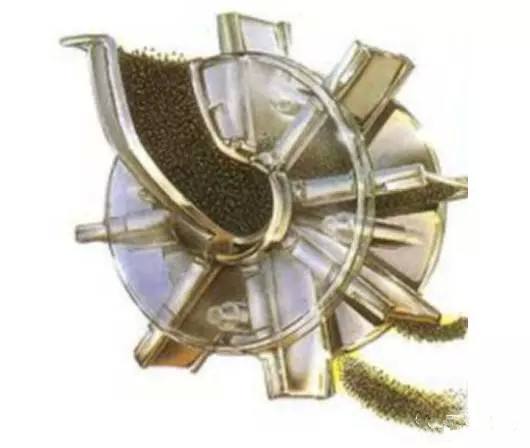
Advantages of shot blasting
- Short shot blasting time, suitable for mass production
- Shot blasting does not require compressed air, saving energy.
- The speed of the impeller can be adjusted to control the projectile’s speed to achieve different surface treatment effects.
- Projectiles can use ferrous materials, but non-ferrous materials are not suitable.
Mesh belt machines
Mesh belt machines are a commonly used shot blasting method for die castings. It uses a continuous metal mesh conveyor belt to feed castings into the machine continuously. There are 4-8 shot blasting ports in the machine’s center. After the casting has been shot blasted, the product can be collected at the export.
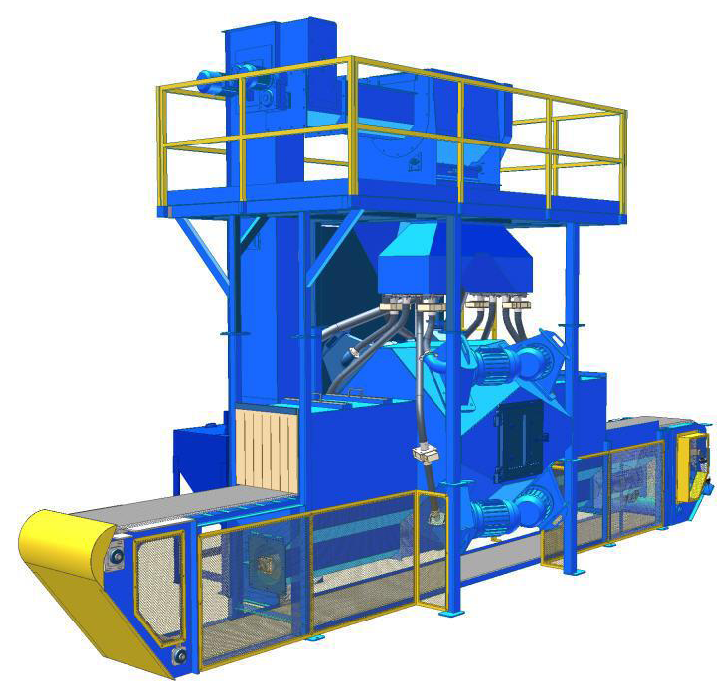
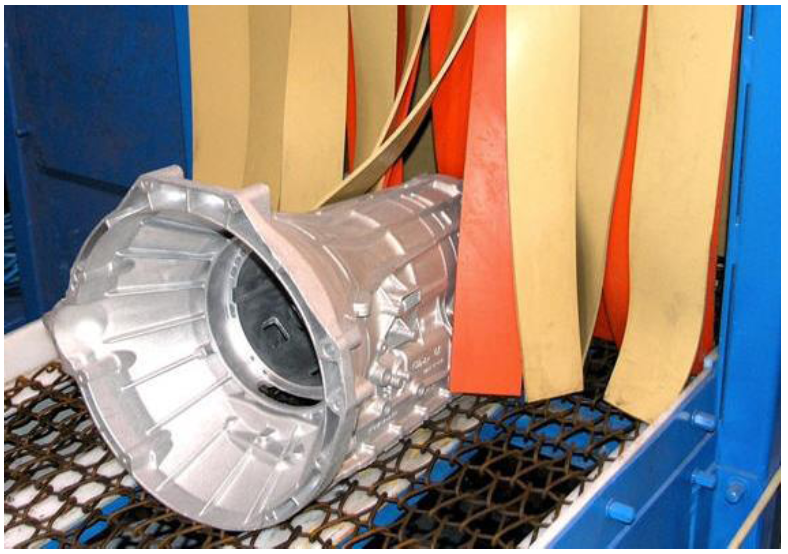
Drum type shot blasting machine
There is a drum device in the shot blasting machine, the product rotates continuously in the drum, and the high-speed moving projectile hits the surface of the workpiece. The continuously rotating drum can make the casting surface evenly impacted by the projectile.
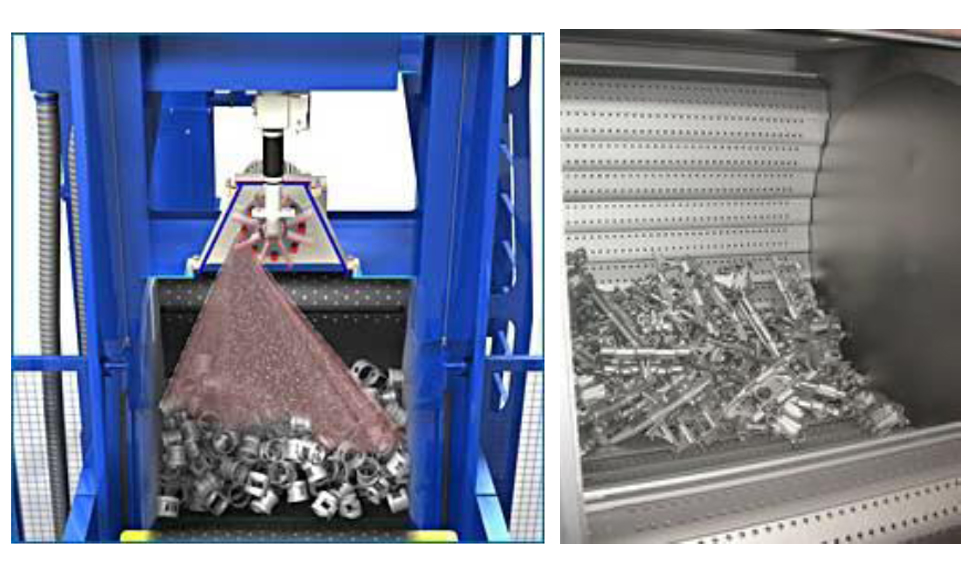
Vertical hook shot blasting machine
Vertical hook shot blasting machine is also a commonly used shot blasting equipment. The parts are hung up by hook hangers and put into the machine for tile blasting operation. Again, a computer can control the angle and speed of projectile projection, and the production efficiency is very high.
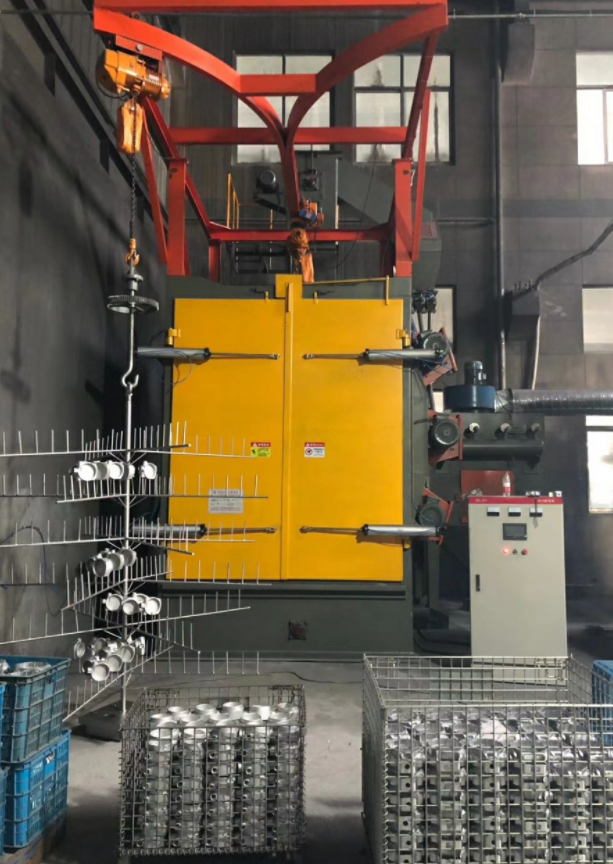
3.Vibratory finishing
The working principle of vibration grinding
The workpiece and the grinding medium are put into the circular vibration plate of the grinding machine together. The vibration motor generates a strong exciting force, and the vibration spring makes the workpiece and the abrasive move in which direction. The movement is, up and down vibration, Flip from the inside out, spiral clockwise. For this reason, some manufacturers of vibrating grinders are also called helical vibrating grinders or helical vibrating finishing machines.
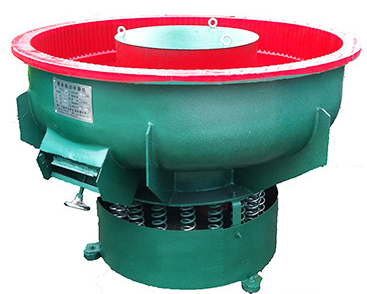
Features of vibration grinding
- It can process a large number of castings at the same time
- Multiple grinding materials can be placed in the same container, e.g., product, grinding media, water, abrasives
- The grinding vibration is very large, which not only makes the casting and the grinding medium rub against each other but also causes friction between the castings
- The workpiece after vibration grinding has a very uniform surface
Grinding media generally come in many types, such as ceramics, plastics, and metals, and come in a variety of shapes and sizes. For example, aluminum alloy and zinc alloy castings generally use plastics and a small amount of ceramics as grinding media. The shape of the medium is usually circular.
However, some castings are more complex in shape, and some surfaces are not easily accessible, so it is necessary to use a medium with sharp edges as an abrasive. The larger size media removes burrs faster, but the surface of the casting is rougher.
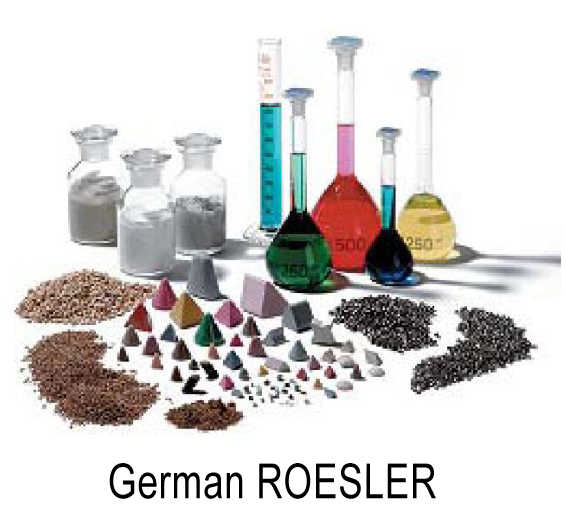
The medium with a smaller size has more contact with the casting surface, and the surface of the casting is smoother after treatment, but the treatment time is longer.
Water and abrasives are usually added during grinding. Abrasives can achieve different functions according to different formulations. Common functions include cleaning, anti-corrosion, degreasing, acid polishing, etc.
There are many kinds of vibratory grinding equipment that can process products in batches or continuously process products like an assembly line. The shape of the device is cylindrical or rectangular. The most common is the barrel-shaped vibrating grinder.
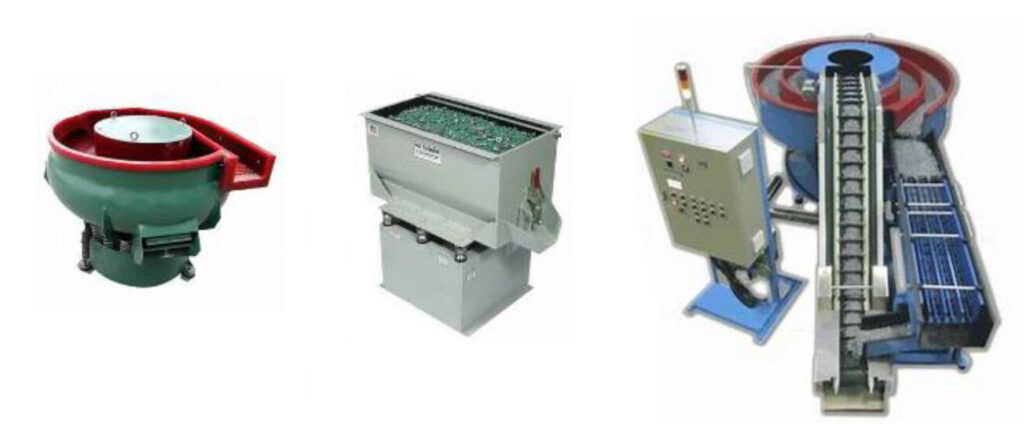
Comparison of shot peening and vibration grinding:
- Generally, the surface treatment effect of vibration grinding is not as good as that of shot peening. Some hot cracks on the product can be eliminated by shot peening, but not necessarily by vibration grinding.
- After the shot peening is finished, it is necessary to remove the dust on the casting by cleaning, which increases the cost of shot peening. During the vibration grinding process, the casting gets a “free cleaning,” saving the time of secondary cleaning
- Vibration grinding Although the casting surface is not as beautiful as shot peening, the vibration grinding is cleaner