Casting Buyer Series- Die Casting After Treatment B
Our previous blog discussed die casting after treatment A. Now we will launch into the second phase of this concept.
1.Machining Die Castings
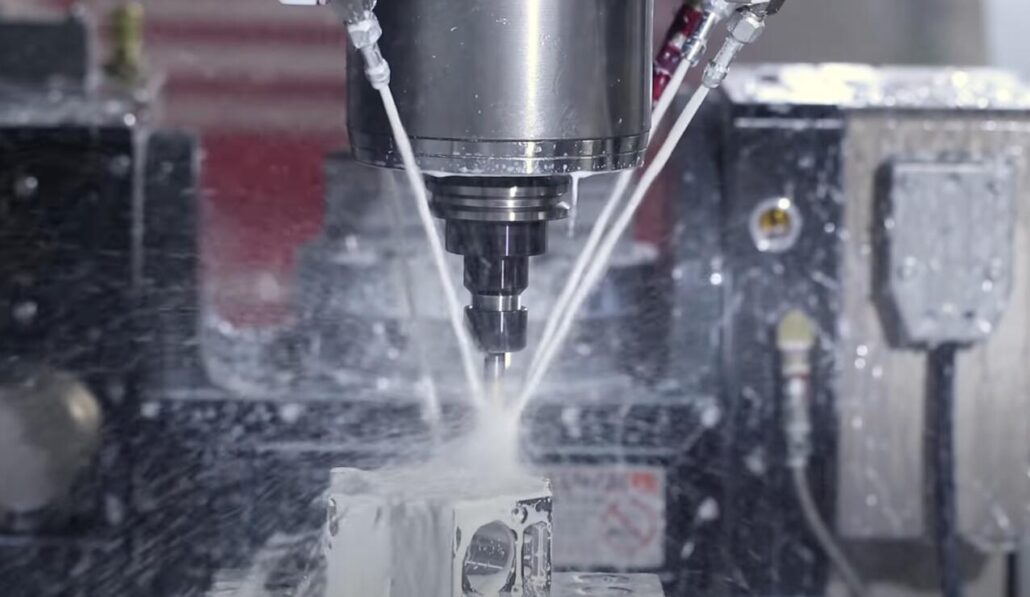
Die castings can be designed very close to the final part. As a result, many castings can even be used without further processing. When designing die castings, we also seek to reduce processing as much as possible to save costs.
Whether machining is required depends on:
- The casting level of die casting enterprises. Some companies have very good mold and die casting skills and can produce very complex castings. Use the mold to form the casting’s topographical features as much as possible, thereby reducing machining. Friends who know injection molds know that the structure of some injection molds can be very cleverly designed. These are all determined by the level of the engineer.
- Selection of alloys. Some alloys can be made with very thin wall thicknesses and very small holes, which reduces the need for machining.
- Are there functional requirements such as assembly and sealing? Areas with general functional requirements require machining to ensure dimensional accuracy and excellent surface finish.
- Economics of production. Die casting is not necessarily economical for some parts, such as small and deep holes, which are not suitable for die casting. Therefore, it is better to use the machining method.
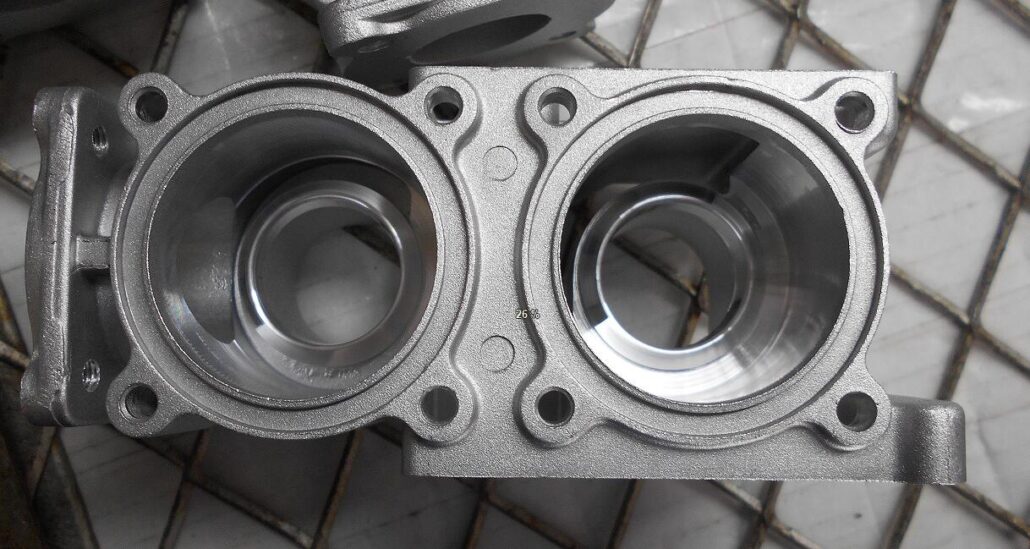
During the casting design stage, the design engineer should maintain close communication with the die casting engineer. The die casting engineer should confirm which parts need to be machined and the specific machining requirements.
Minimize machining allowances for surfaces to be machined. Excessive machining will expose internal pores and cause leaks. In addition, some parts can be formed by sliding blocks, thus avoiding machining.
NADAC Data on Machining
We will discuss this aspect in three sections: Die-cast aluminum alloy, Die-cast magnesium alloy, and Die-cast zinc alloy.
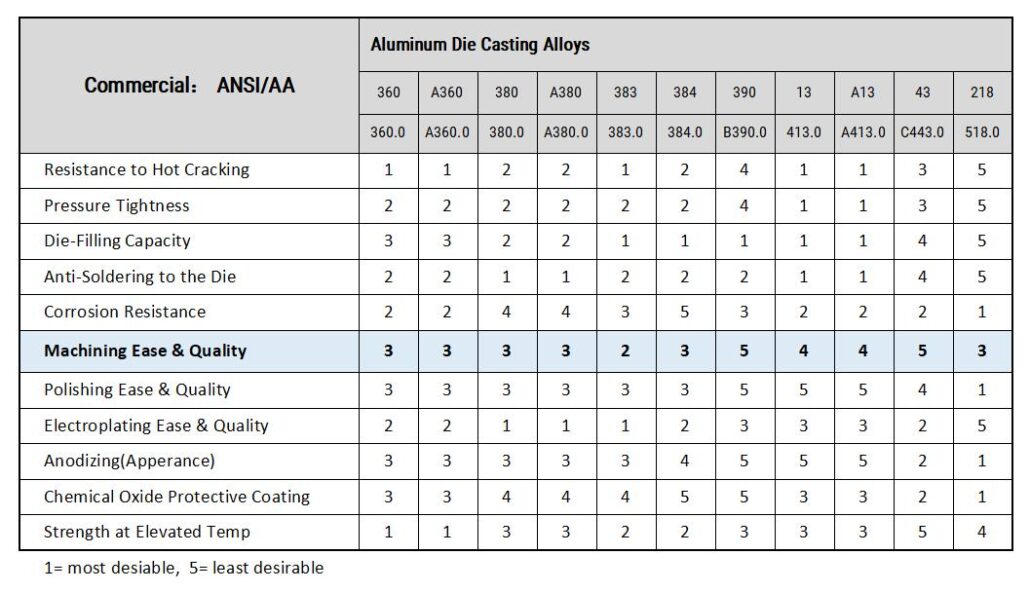
Die-cast aluminum alloy:
- Machinability is much better than iron, steel, titanium alloys
- 383-grade aluminum alloy is the best
- 390-grade aluminum alloy has the worst cutting performance
- General castings require two machining operations (roughing and finishing)
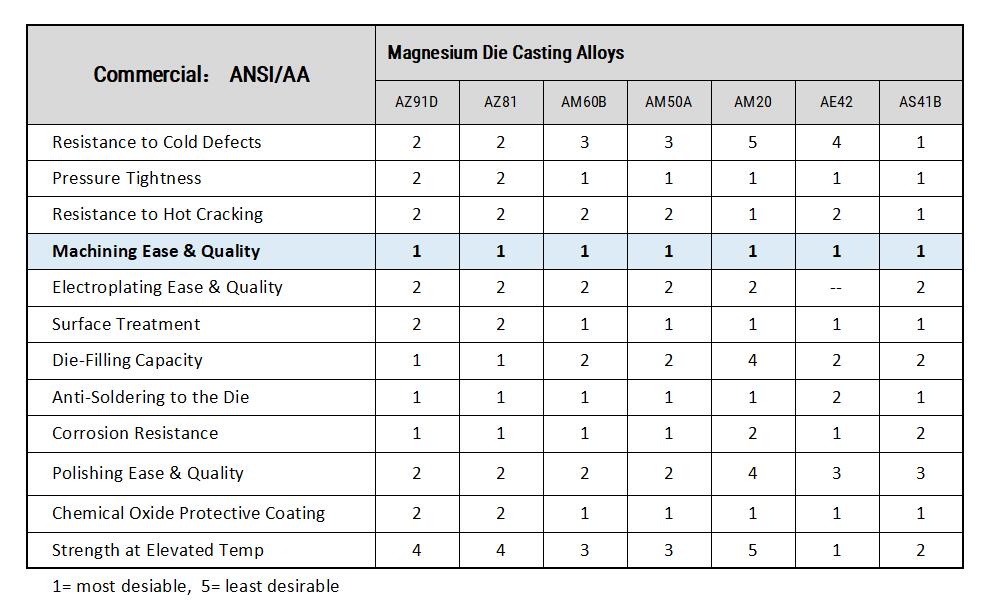
Die-cast magnesium alloy:
- Magnesium alloy has the best cutting performance among all die casting alloys.
- Generally, only one processing is required.
- Magnesium alloy chips require special storage and proper disposal to avoid fire. Whether magnesium alloys are die-casting or post-processing, each process requires special safety considerations. A little carelessness can cause the magnesium alloy to burn or even explode. Therefore, extra attention to safety is required.
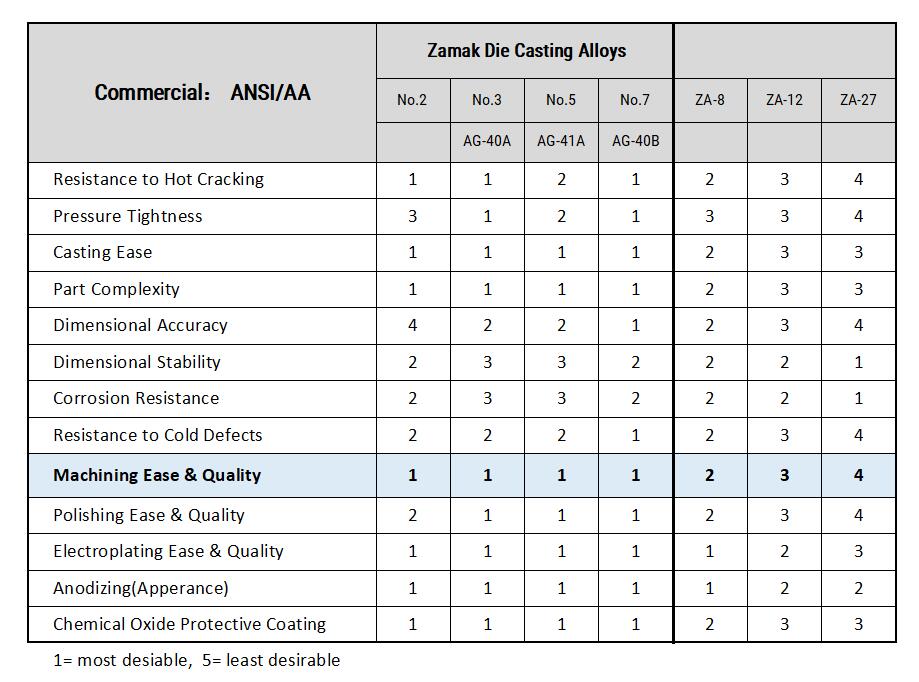
Die-cast zinc alloy:
- Excellent machining performance
- Due to the immense heat generation, it is recommended to use cutting fluid
2.Heat Treatment of Die Castings
Why heat treatment of die castings, and what is the purpose? Heat treatment is the best way to improve the mechanical properties of castings.
- Greatly improved mechanical strength
- Improve fatigue strength
- Sometimes increases elongation
- Improve impact strength
- Improve dimensional stability
The heat treatment of die castings is generally divided into three stages, but not necessarily every heat treatment must include these three stages:
- Solution heat treatment: The die casting needs to be heated to 537°C (1000°F) within 2~3 hours.
- Quenching
- Aging: Heat the die casting to approximately 176°C (350°F) within 2 to 6 hours.
Heat treatment aims to re-diffusion and recombines supersaturated solid solutions in the aluminum alloy, such as CuAl2 or Mg2Si.
But most die castings cannot be heat treated!
Since heat treatment has so many benefits, why can’t die casting be heat treated? Because the heat treatment will make the surface of the die casting blistering.
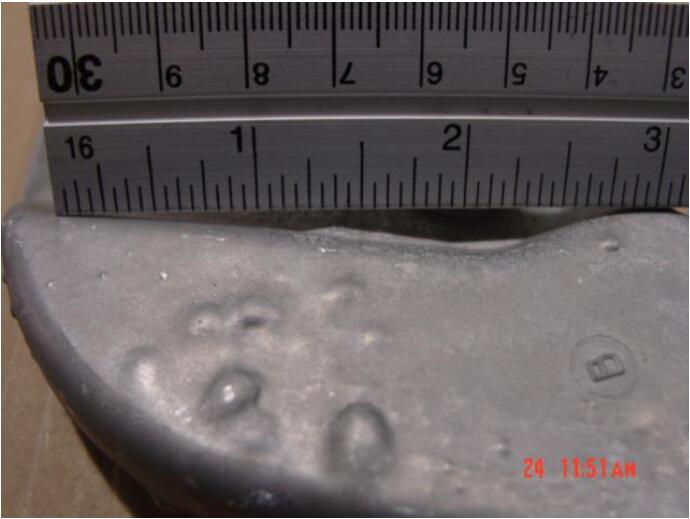
Why is it bubbling?
First of all, there should be defects under the die casting surface, with air bubbles or pores generated by the release agent. The pressure during the production of die castings is very high, reaching 40Mpa~140Mpa.
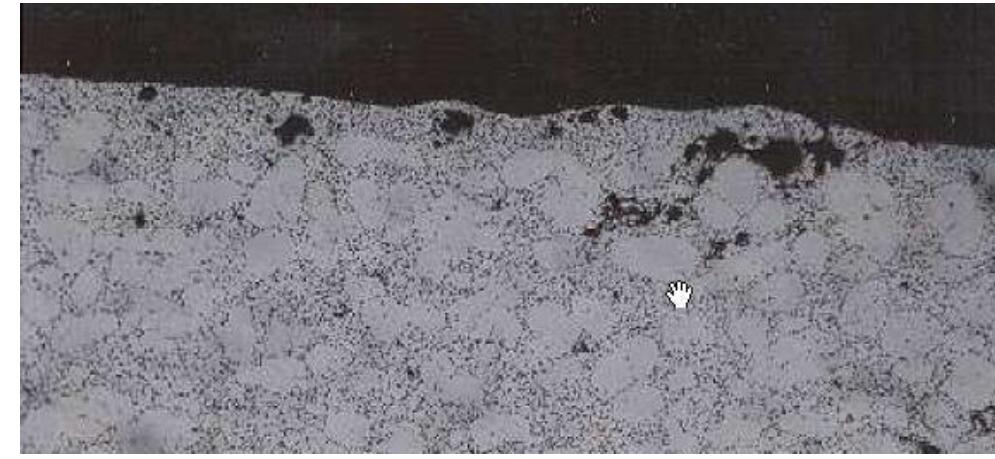
So there is the same pressure in the pores below the surface. During solution treatment, as the temperature increases, the pressure of the pores inside the casting increases rapidly. When the pressure exceeds the strength of the casting, blistering occurs on the surface of the casting.
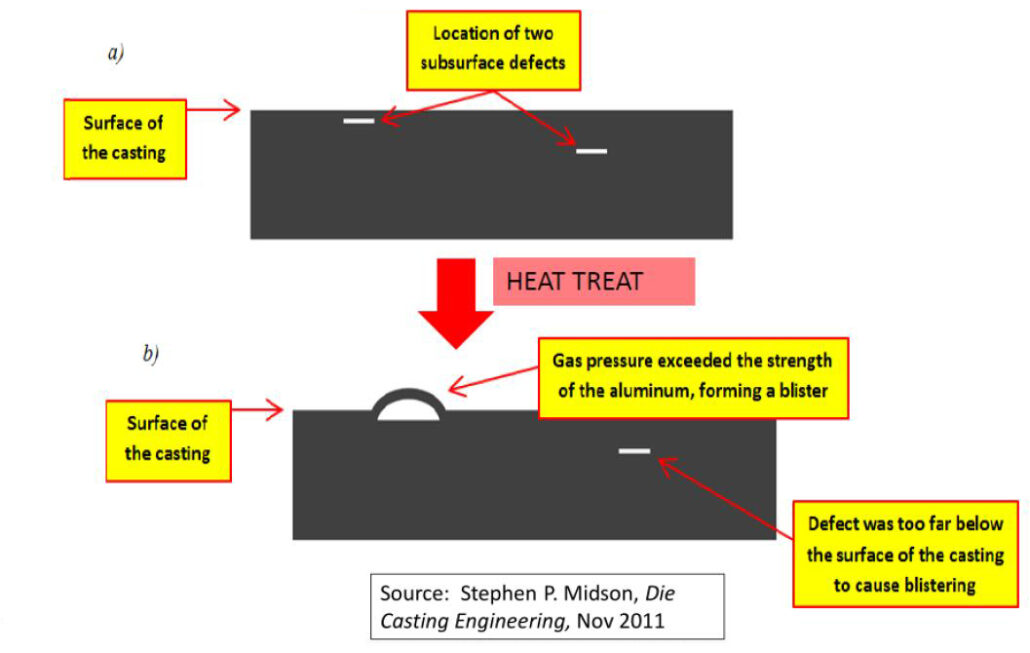
How can I reduce foaming?
A study in Australia shows that by reducing the solution temperature to 430 ℃ ~ 480 ℃ and the solution time to 15 minutes; then you can avoid bubbles. In this way, the die casting can also avoid blistering. In addition, the quenching and aging treatment process are the same as the original, so traditional die castings can also be heat treated.
Common heat treatment methods
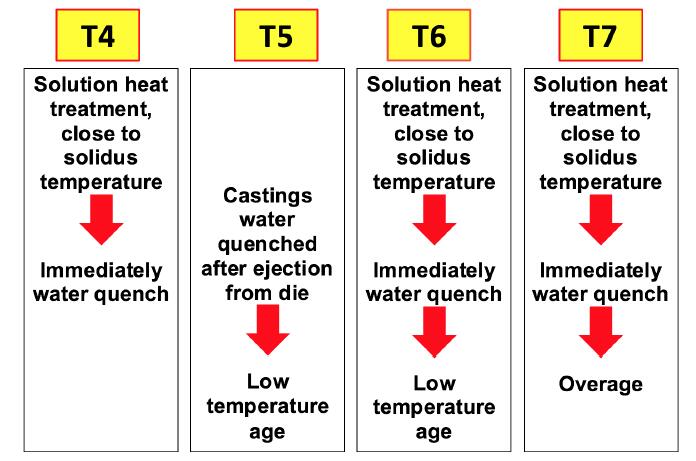
T4 heat treatment has no aging treatment procedure, and T5 heat treatment has no solid solution procedure. Different heat treatment methods can improve the mechanical properties of castings in different directions. It does not say which heat treatment method is the best but chooses the appropriate heat treatment method according to the actual needs.
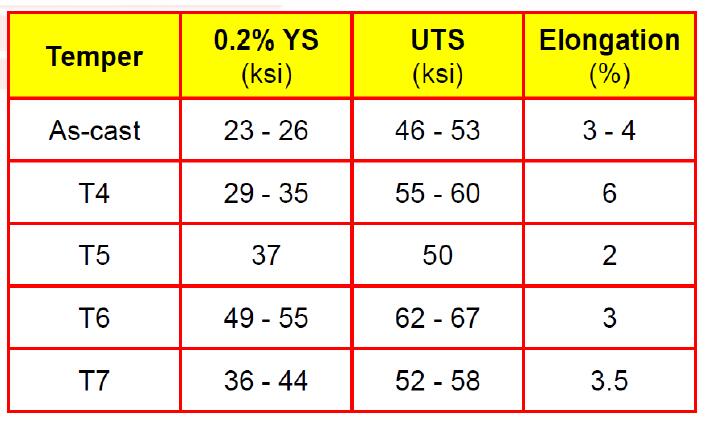
The elongation of the casting before heat treatment is 3~4%, and it can reach 6% after T4 heat treatment. But after T5 heat treatment, the elongation decreased instead. Therefore, according to your own needs, choose the appropriate heat-treatment process.
3.Coatings on Die Castings
Generally speaking, although the corrosion resistance of die castings is relatively good, some follow-up surface coating is usually done under the requirements of some special functions. Surface coating can achieve:
- Provides a protective coating for castings in extreme environments
- Provide surface decoration effect for castings
- Impregnation treatment is used to fill the surface and subcutaneous layers of the casting with paint so that the die-casting has a sealing effect
- Increase the wear resistance of die castings
- Prevents galvanic corrosion of die castings such as rust and mildew
Zinc alloy products, in particular, are often given a decorative finish. For example, bathroom products are mostly made of zinc alloy.
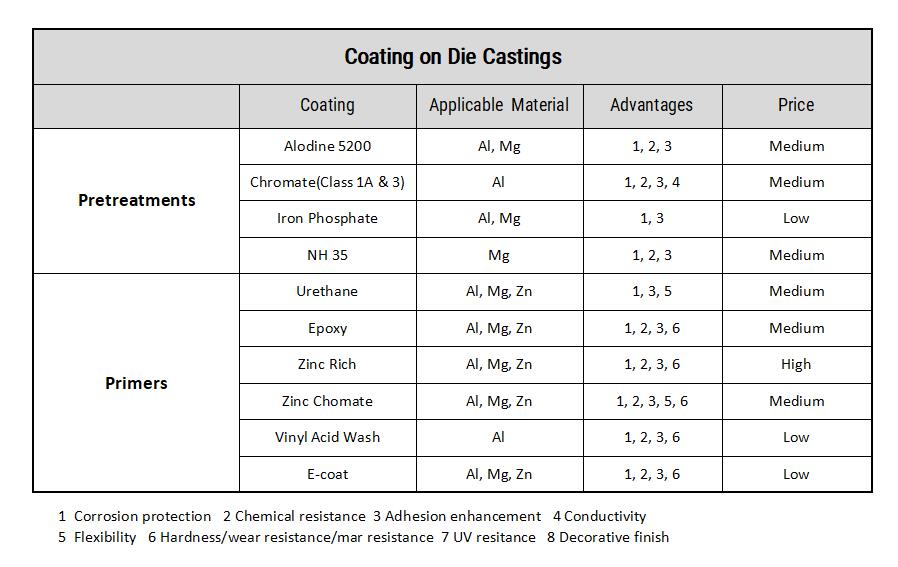
The charts show different coatings, the material they support, their advantages, and prices. The coatings are divided into the following;
- Pretreatments: Alodine 5200, chromate(class 1A & 3), Iron phosphate, NH35.
- Primers: urethane, epoxy,zinc-rich, zinc chromate, vinyl acid wash, and E-coat.
From the chart,
- Alodine: it is applicable for aluminum and magnesium. Its price is average. Then it protects against corrosion, enhances adhesion, and possesses good chemical resistance.
- Chromate (class 1A & 3): it is applicable for aluminum. It has good conductivity, protects against corrosion, enhances adhesion, and resists chemicals.
- Iron phosphate: it is applicable for aluminum and magnesium. Then it protects against corrosion and enhances adhesion.
- NH35: it applies to magnesium. Its price is average. Then it protects against corrosion, enhances adhesion, and possesses good chemical resistance
- Epoxy, zinc-rich, and E-coat are all applicable to aluminum, magnesium, and zinc. Then it protects against corrosion, enhances adhesion, and possesses good chemical resistance. They also exhibit good wear resistance.
- Urethane: it is applicable to aluminum, magnesium, and zinc—good performance in terms of corrosion, adhesion, and flexibility.
- Zinc chromate: it is applicable to aluminum, magnesium, and zinc. It has good performance in terms of corrosion, adhesion, flexibility, chemical resistance, conductivity, and hardness.
- Vinyl acid wash: it is applicable for aluminum. Then it protects against corrosion, enhances adhesion, and possesses good chemical resistance. They also exhibit good wear resistance.
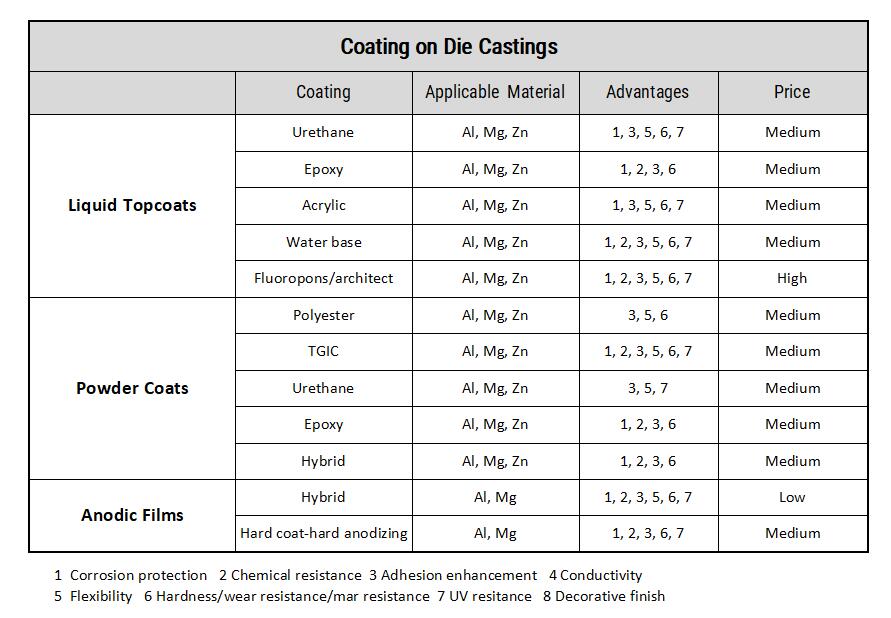
Liquid Topcoats
This includes urethane, epoxy, acrylic, water base, and fluoropons. Each of them is suitable for aluminum, magnesium, and zinc. They have their respective tags showing their properties (1 to 6). See the table as it shows what each number represents.
Powder Coats
This includes polyester, TGIC, urethane, epoxy, and hybrid. Each of them is suitable for aluminum, magnesium, and zinc. They have their respective tags showing their properties (1 to 6). See the table as it shows what each number represents
Anodic Films
The hard coat-hard anodizing and anodize are the element here. They are applicable to aluminum and magnesium. They have their respective tags showing their properties (1 to 6). See the table as it shows what each number represents
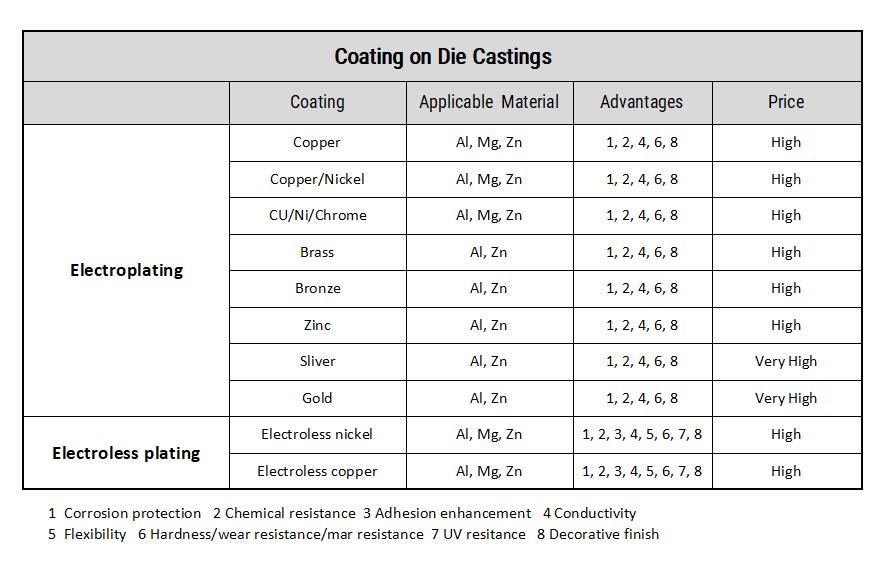
From the chart, the elements are divided into the following categories;
Electroplating
This includes copper, CU/Ni/Chrome, gold, zinc, silver, bronze, brass, copper/nickel.
Electroless plating
This includes electroless nickel and electroless copper.
The second column shows the applicable material for each element, and the next column indicates their properties (1-8). The legend that explains the property numbers is outside the chart. The last column indicates the price of each element.
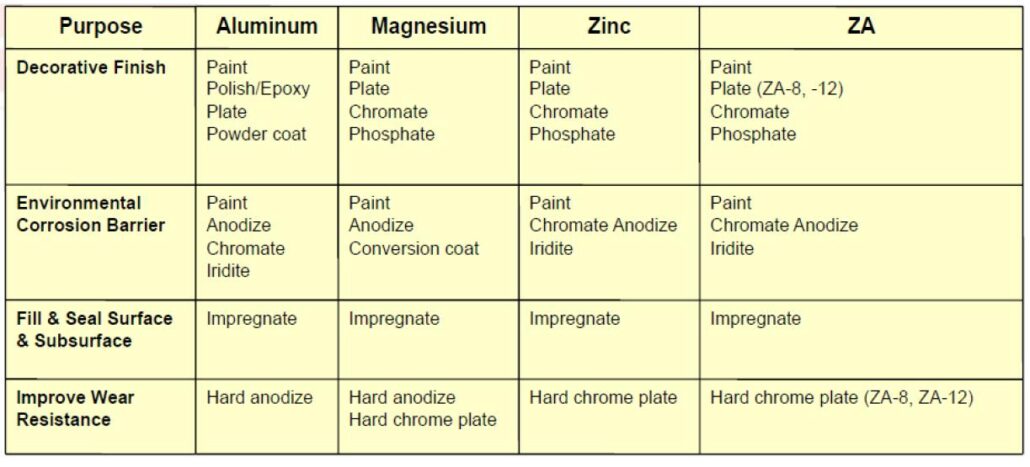
The chart above shows the purpose of aluminum, magnesium, zinc, and zirconium. Each of these purposes is explained in the following sections;
- Decorative finish
- Environmental corrosion barrier
- Fill and seal surface and subsurface
- Wear resistance
The second column talks about aluminum’s purpose under the sections mentioned above. It follows suit with magnesium, zinc, and zirconium.