Casting Buyer Series - Die-Casting Machine and Mold
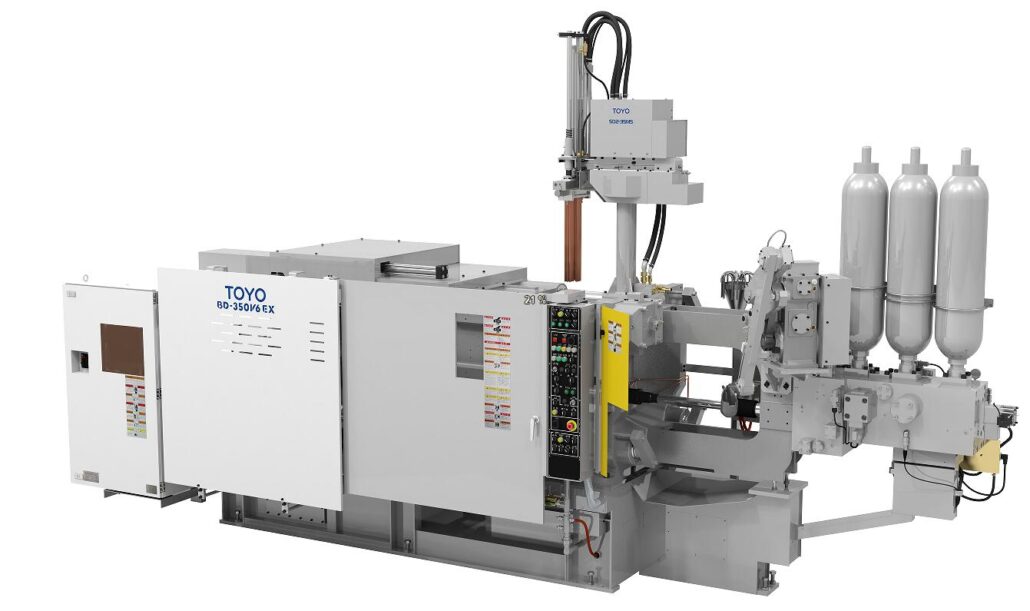
The die-casting machine is the most basic equipment for die-casting production, and it is also the guarantee for obtaining high-quality die-casting parts. Therefore, we should first select a suitable die-casting machine when designing a die-casting mold.
In order to ensure the standard progress of die-casting production and obtain high-quality castings, the technical specifications and performance of the selected die-casting machine must meet the objective requirements of die-casting parts.
On the contrary, if the die-casting machine is predetermined, the designed die-casting mold must meet the specifications and performance requirements of the die-casting machine.
1.Classification Of Die Casting Machines
Standard die casting machines are divided into hot chamber die casting machines, and cold chamber die casting machines.
Then, the cold chamber die casting machines are divided into vertical cold chamber die casting machines and horizontal cold chamber die casting machines.
Cold Chamber Die Casting Machine
Vertical Cold Chamber Die Casting Machine
The pressure chamber and injection mechanism of the vertical cold chamber die casting machine are vertical. Therefore, the center of the pressure chamber is perpendicular to the direction of movement of the mold.
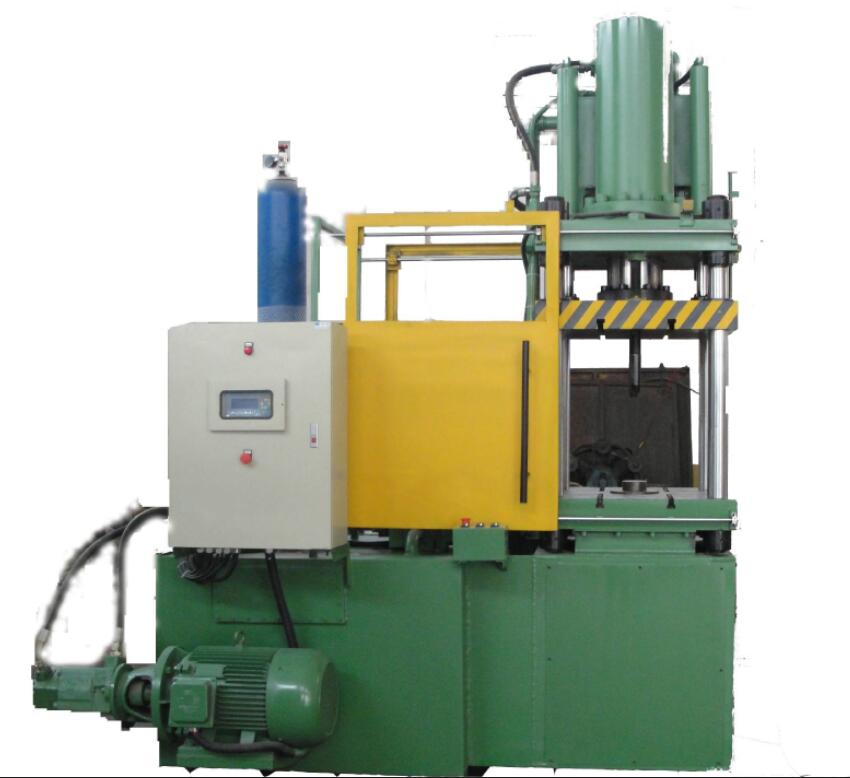
Features of vertical cold chamber die casting machine:
- The punch seals the nozzle hole before injection, which is beneficial to prevent impurities from entering the cavity.
- Mold suitable for design center feeding
- The injection mechanism is upright, and the machine occupies a small area
- When the molten metal enters the mold cavity, it goes through a turning point, and the pressure loss is large
- Due to the addition of the anti-material mechanism, the structure of the machine is complex, the operation and maintenance are inconvenient, and the production efficiency is affected
- Commonly used in die casting of aluminum, magnesium, and copper alloys
Since vertical cold chamber die casting machines are rarely used, we will not introduce them too much.
Horizontal Cold Chamber Die Casting Machine
The pressure chamber and injection mechanism of the horizontal cold chamber die casting machine are in a horizontal position, and the center of the pressure chamber is parallel to the direction of movement of the mold
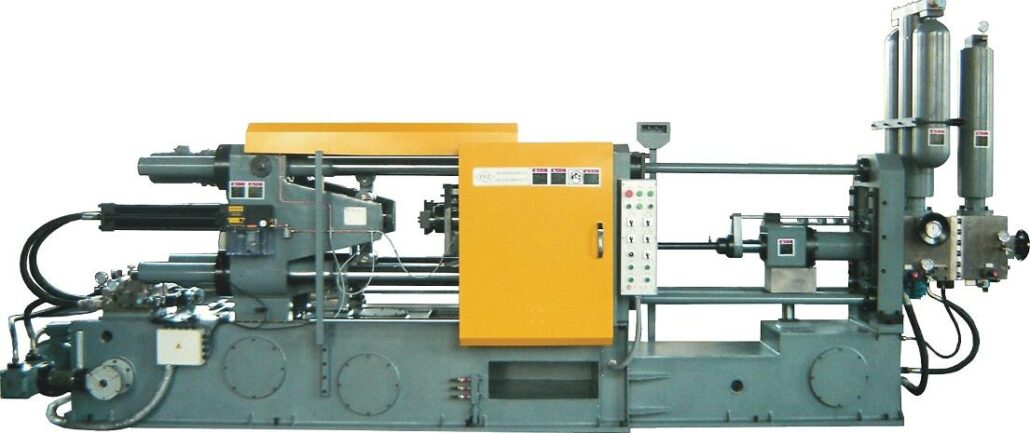
Features of horizontal cold chamber die casting machine:
- The molten metal enters the cavity with less turning and pressure consumption, which is conducive to the pressurization effect, so the pressure is enormous.
- The machine has simple operation procedures, high production efficiency, easy maintenance, and easy automation
- The shot chamber generally has two-shot positions, eccentric and central, and can be adjusted arbitrarily between the eccentric and central positions
- The metal liquid has a large contact area with the air in the pressure chamber. Therefore, if the speed is not selected correctly during injection, it is easy to be involved in gas and impurities.
- It is inconvenient to die-cast products with inserts, and the structure of the die-casting mold is complicated when using the center feed.
- The horizontal machine is the most widely used model, commonly used for aluminum, magnesium, and copper alloys die-casting. One can also use the machine for die-casting of ferrous alloys.
The main components of the horizontal cold chamber die casting machine are the clamping mechanism, injection mechanism, power system, control system, etc.
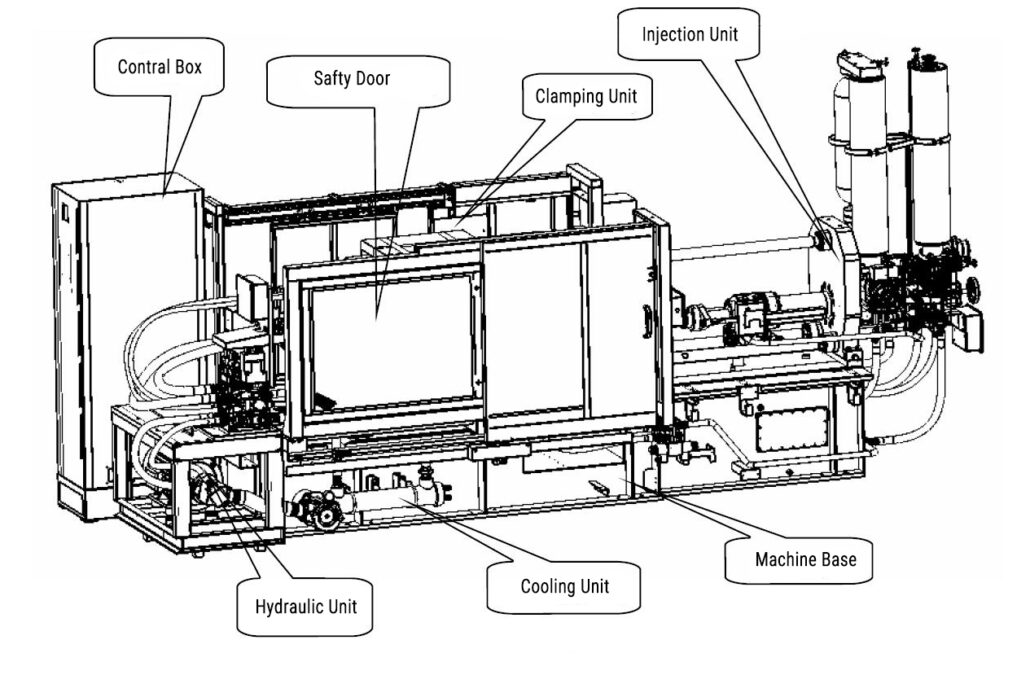
The production process of cold chamber die casting machine:
- Clamping: The first step is to install the die-casting die on the die-casting machine. Clean and inspect the die casting molds, then spray mold release agent. Then, operate the machine to close the die-casting mold.
- Injection: The molten metal is transferred from the furnace to the press chamber with a ladle. The plunger pushes the molten metal from the pressure chamber into the mold. After filing the mold, the punch applies high pressure to solidify the molten metal.
- Cooling: After the molten metal fills the mold, it solidifies under high pressure. There must be sufficient solidification time to ensure that the mold is locked. The casting can only be unclamped after it has completely solidified.
- Ejection: After the mold is opened, the ejection cylinder of the die-casting machine is controlled to push the ejection mechanism of the mold to push the product out of the mold. Using a robot or manually, the die casting is removed.
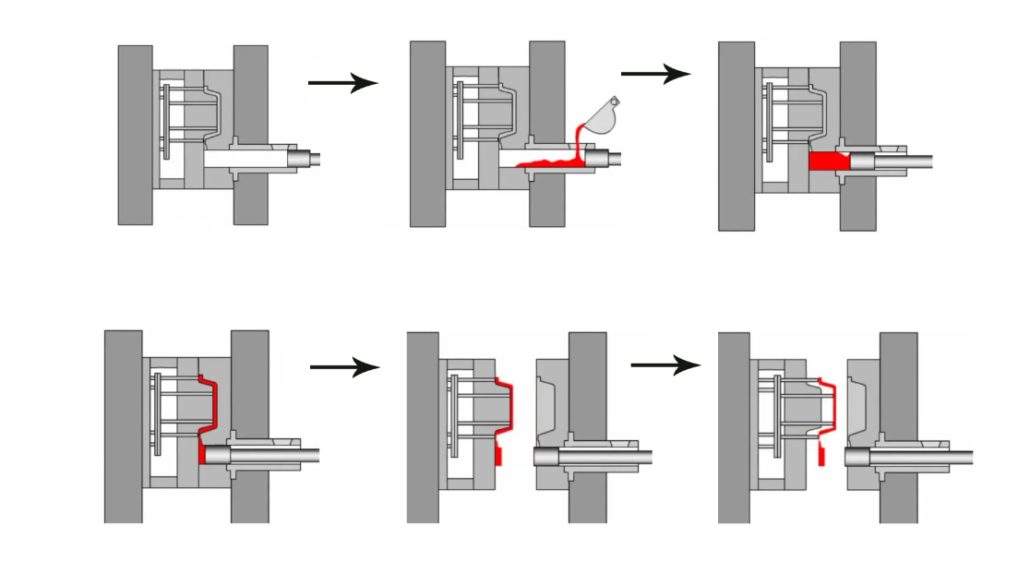
Main parameters of cold chamber die casting machine:
- Clamping force: measure the clamping force of the machine; the bigger the machine, the higher the clamping force
- Plate size: the size of the machine’s fixed and moving templates; the larger the machine, the larger the size
- Space between tie bars: The maximum size for die installation.
- Die height: the maximum and minimum thickness allowed by the die
- Plunger diameter: the diameter of the punch that can be selected
- Intensifier: the pressure of the die-casting booster process
- Ejecting stroke: the maximum distance that the machine can eject the product
Hot Chamber Die Casting Machine
The injection mechanism of the hot chamber die casting machine is generally vertical, and the pressure chamber is immersed in the liquid metal of the heat preservation crucible and is integrated with the crucible. The injection part is mounted on the crucible.
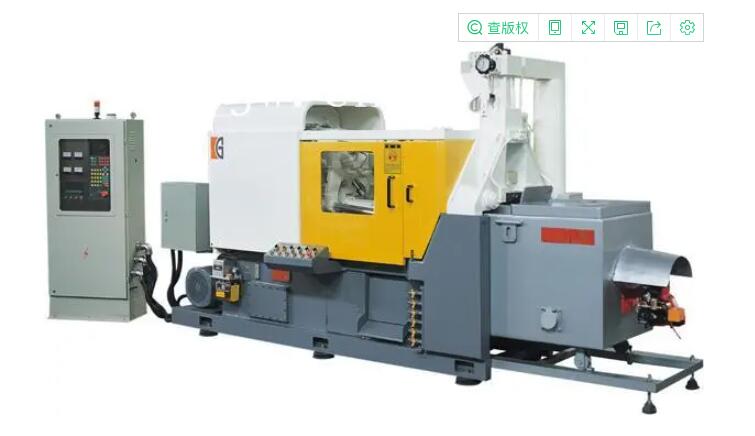
The main components of the hot chamber die casting machine include clamping mechanism, injection mechanism, power system, control system, etc.
Features of hot chamber die casting machine:
- Simple structure, convenient operation, high production efficiency, easy to realize automatic production
- Small metal loss and stable process
- The purity of the molten metal is high, and the temperature fluctuation range is small
- The casting has fewer inclusions and good quality
- The crucible can be sealed, and the protective gas can be introduced to protect the liquid surface of the alloy, which is of special significance for the anti-oxidation and anti-burning of the magnesium alloy liquid.
- The pressure chamber and the injection punch are immersed in the molten metal for a long time, which is easy to cause adhesion and corrosion, which affects the service life
- It is difficult to replace the pressure chamber, and it is easy to increase the iron content of the alloy
- Commonly used in lead, tin, zinc alloy die-casting, and sometimes magnesium, aluminum alloy can also be die-casted
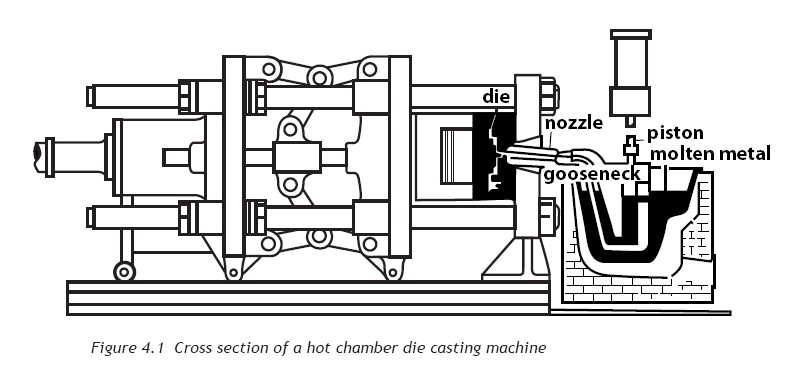
The production process of hot chamber die casting machine:
- Clamping: The first step is to install the die-casting die on the die-casting machine. Clean and inspect die-casting molds, then spray mold release agent. Operate the machine to close the die-casting mold.
- Injection: The punch presses the molten metal into the mold through the gooseneck and nozzle. The punch applies high pressure to solidify the molten metal.
- Cooling: After the molten metal fills the mold, it solidifies under high pressure. There must be sufficient solidification time to ensure that the mold is locked. The casting can only be unclamped after it has completely solidified.
- Ejection: After the mold is opened, the ejection cylinder of the die-casting machine is controlled to push the ejection mechanism of the mold to push the product out of the mold. Using a robot or manually, the die casting is removed.
The general parameters of the hot chamber die casting machine are similar to those of the cold chamber die casting machine and will not be described in detail.
2.Selection Principle Of Die Casting Machine
There are basic guidelines when it comes to picking a die casting machine. The following points should guide your decision.
- Understand the types and characteristics of die casting machines;
- Consider the alloy type and related requirements of die castings;
- The selected die-casting machine should meet the operating conditions and technical needs of die-casting parts;
- The die casting chosen machine should have a certain margin in terms of performance, parameters, efficiency, and safety to ensure satisfactory yield, productivity, and safety;
- On the premise of guaranteeing the fourth point, the reliability and stability of the machine should also be considered, and a die-casting machine with reasonable cost performance should be selected accordingly;
- For the production scale of die-casting parts with many varieties and small production volume, on the premise of ensuring the fourth point, the compatible specifications should be scientifically selected to cover the right sorts and reduce the cost of the die-casting machine.
- Among the technical indicators and performance parameters of the die-casting machine, the first thing to pay attention to is the injection performance. Under the same or similar specifications, the model with a broader range of injection performance parameters is preferred;
- Under possible conditions, try to be equipped with mechanized or automated devices, which are beneficial to product quality, production efficiency, safe production, enterprise management, and cost accounting;
- Evaluate the effect of the selected die casting machine, including yield, productivity, failure rate, maintenance frequency, workload, performance stability, operational reliability, safety, etc.
3.Die Casting Mold
This permanent metallic mold features significantly in the die casting process. It is a make up that comprises stationary and movable mold halves which contain the mold cavity.
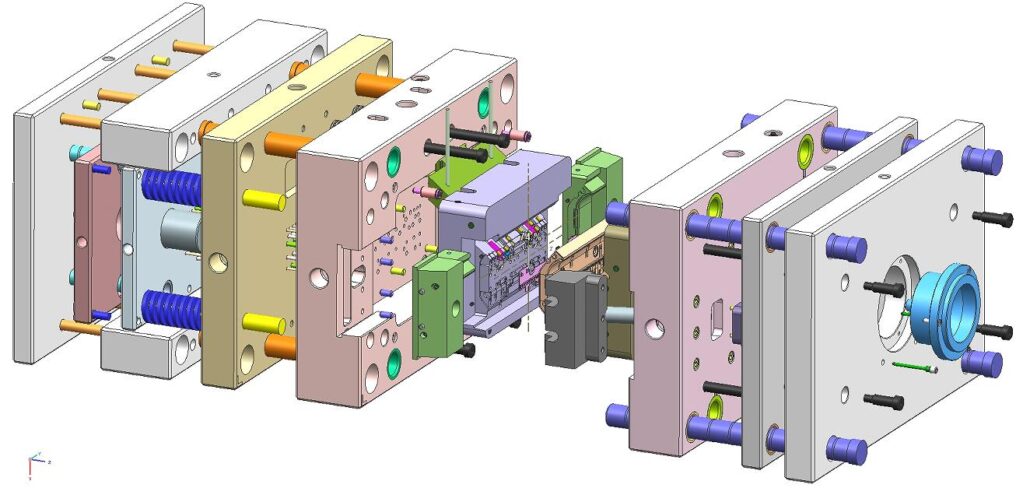
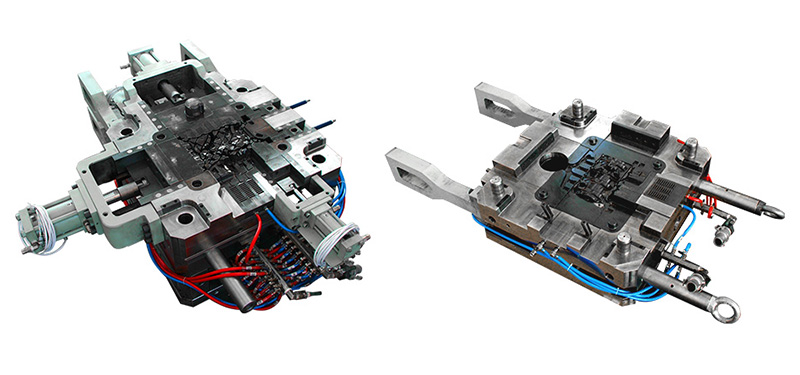
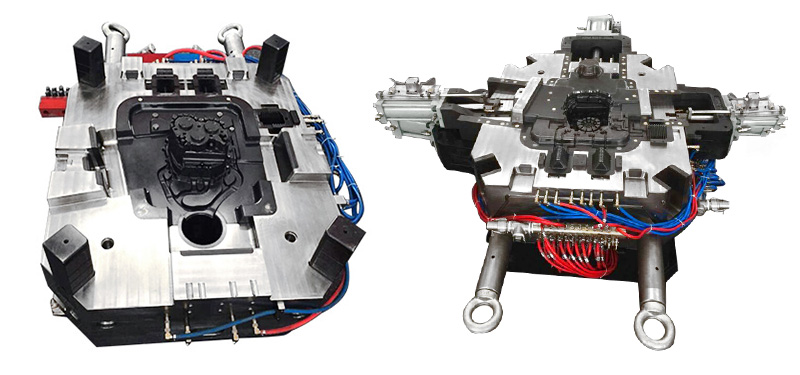
The Composition of Die Casting Mold
The die-casting mold is composed of two basic parts: a movable mold and a fixed mold, including:
- Forming part: the part that determines the geometric shape and dimensional accuracy of the casting, and the part that forms the outer surface of the casting becomes a cavity. The inner surface of the casting becomes the core.
- Mold base part: the frame of the die-casting mold, the parts of the mold are merged and fixed according to certain rules and positions so that it can be installed on the die-casting machine.
- Runner system:The channel through which molten metal enters the cavity during die-casting. It consists of a sprue sleeve, a runner, and an inner gate.
- Drainage system: the part used to remove gas and collect metal slag during die-casting, which is composed of slag bag and exhaust trough.
- Ejection mechanism: The mechanism that ejects the casting to make it come out of the mold, which is composed of a push plate and an ejector rod
The die casting mold has the following functions.
- Holds molten metal in the shape of the desired casting
- Provides access to the cavity (Provide means for molten metal to get into the space where it is held in the desired shape)
- Remove heat from molten metal to allow solidification
- Enables the removal (ejection) of the solidified metal