Heat Treatment of Die Castings-1
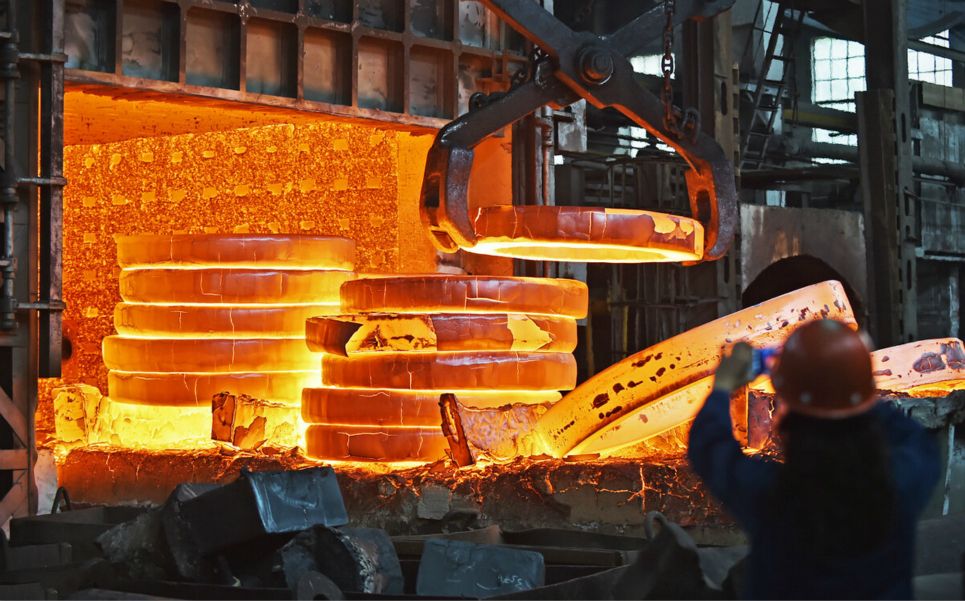
1.The Concept of Metal Heat Treatment
Definitions
Metal heat treatment is to heat the metal workpiece to a suitable temperature in a certain medium, keep it at this temperature for a certain period of time, and then cool it in the different mediums at different speeds by changing the microstructure on the surface or inside of the metal material—a process in which structures are used to control their properties.
Features
- One of the important processes in machinery manufacturing and an important link in quality management
- Generally, do not change the shape of the workpiece and the overall chemical composition
- Changes in the microstructure inside the workpiece or the chemical composition of the workpiece surface
- Changes in mechanical properties, physical properties, and chemical properties
Classification
- Overall heat treatment: overall heating, heat preservation
- Surface heat treatment: surface changes such as case hardening
- Chemical heat treatment: chemical method, both physical method
Characteristics of the metal heat treatment process
- Heat treatment process: including heating, heat preservation, cooling three processes, these processes are interconnected and uninterrupted.
- Heating: mainly choose the heating temperature and heating speed
- Heat preservation: It is to control the heat preservation time to ensure that the temperature of the workpiece is balanced inside and outside.
- Cooling: mainly to control the cooling temperature and cooling speed.
2.Aluminum Alloy
Properties of pure aluminum
Pure aluminum is very soft and not suitable for direct use. The physical properties of pure aluminum are shown in the table below:
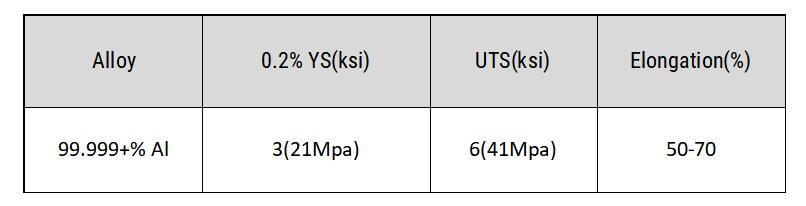
How to increase the strength of aluminum alloy:
- Alloying
- Work hardening
- Reduce grain size
- Heat treating Precipitation strengthening
Classification of aluminum alloys
- Deformed aluminum alloys: generally made into semi-finished products or die forgings by press working. (Example: 1050, 2024, 3104, 4032, 5083, 6061, 7050, etc.)
- Cast aluminum alloys: generally used to cast complex castings. (Example: A356, A390, ZL101, ZL401, YL104, ADC12, etc.)
Most high-strength aluminum alloys are precipitation-strengthened, which at peak strength
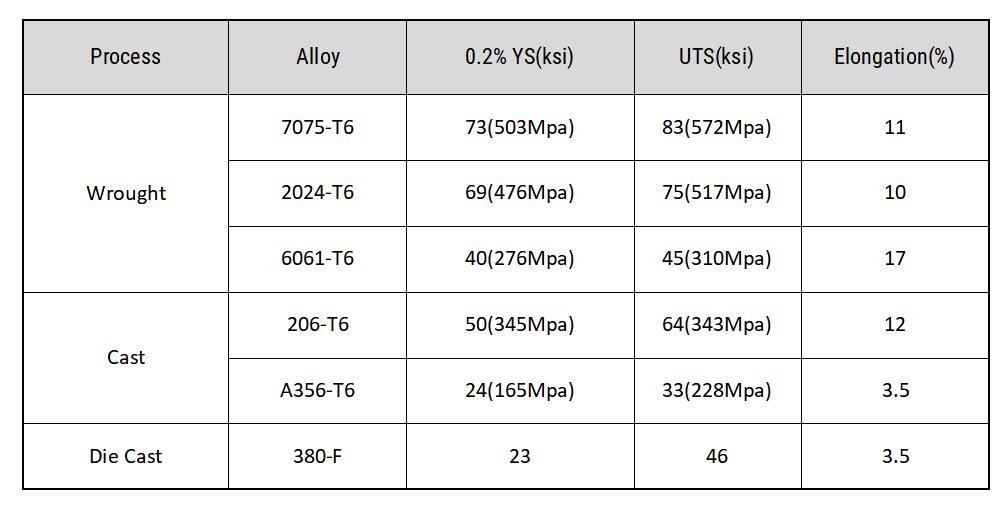
Classification of deformed aluminum alloys
Anti-rust aluminum alloy: Al-Mn system Al-Mg system
Features:
- Higher corrosion resistance and strength than pure aluminum, and
- Good weldability and plasticity,
- Poor cutting performance
Hard aluminum alloy: Al-Cu-Mg system
Features:
- Good strength and heat resistance,
- Corrosion resistance is not as good as pure aluminum and rust-proof aluminum alloy
Super hard aluminum alloy: Al-Zn-Mg-Cu system
Features:
- High strength,
- Good mechanical properties,
- Strong corrosion resistance,
- High low-temperature strength
- Poor resistance to stress corrosion and exfoliation corrosion,
- Poor welding performance
Forged aluminum alloy: Al-Mg-Si system
Features:
- Medium strength,
- Good corrosion resistance,
- Good welding performance,
- Good process performance,
- Good oxidation coloring performance
Classification of cast aluminum alloys
Al-Si based alloy
Features:
- Good casting performance and wear resistance,
- Small thermal expansion coefficient
Applications: Housings, Cylinders, Cases, Frames, Pistons
Al-Mg based alloys
Features:
- High strength and plasticity,
- Good corrosion resistance,
- Good comprehensive mechanical properties
- Machinability at room temperature,
- Easy to oxidize during casting
Application: radar base, aircraft engine case, propeller, landing gear
Al-Zn alloy
Features:
- High strength,
- Easy to corrode,
- Low price,
- Self-quenching
Applications: Models, templates, and equipment supports
3.Aluminum Alloy Heat Treatment
Principle of heat treatment
Heat treatment of aluminum alloys, also known as age hardening (aga hardening) or precipitation hardening (precipitation hardening)
Select a certain heat treatment process, control the heating speed to rise to a corresponding temperature, keep it for a certain period of time, and cool it at a certain speed to change the structure of the alloy.
After heat treatment, nano-sized particles inside the material will be uniformly distributed in the aluminum core matrix—for example, Mg2Si particles, Al2Cu particles. Nano-sized tissue strengthens the casting by preventing dislocation movement. The tissue resembles a reticular or spherical structure.
Note that not all aluminum alloys can be strengthened by heat treatment.
Basis:
According to whether the second phase precipitation occurs during the heat treatment process, precipitation strengthening behavior of dispersion strengthening behavior occurs. If it occurs, it becomes a heat treatable strengthened alloy.
Method:
Generally, it can be determined by the alloy phase diagram, that is, the alloy system whose solubility curve (surface) decreases rapidly with the decrease of temperature belongs to the heat-treatable strengthening alloy.
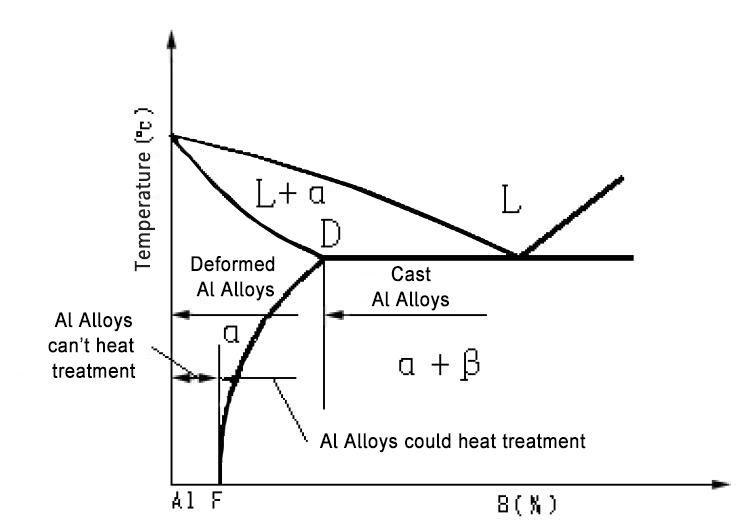
- The alloy whose composition is at the left of the F point is called the aluminum alloy that cannot be strengthened by heat treatment.
- The alloy whose composition is between F and D is called aluminum alloy that can be strengthened by heat treatment.
- The composition located to the right of point D is cast aluminum alloy.
- It should be noted that point D in the phase diagram is only the theoretical boundary line of the maximum saturated solubility of the alloy and cannot be absolute.
Purpose of heat treatment of aluminum alloy
- Improve mechanical properties: mainly include increasing strength, increasing fatigue strength, increasing ductility, and increasing impact resistance
- Improve processing performance
- Eliminate intragranular segregation and improve organizational uniformity
- Eliminate the internal stress caused by the chilling, uneven wall thickness of the casting itself and hinder shrinkage during the casting process to obtain a stable structure and size.
Characteristics of heat treatment of cast aluminum alloy
- Since the structure formed during the casting process is relatively coarse, and the uniformity of the intragranular composition is poor, the heat treatment time is relatively long, generally several hours or even longer.
- The shape of the casting is relatively complex, and the wall thickness difference is large. It is easy to deform during heating and cooling and is difficult to correct. Therefore, cast aluminum heat treatment’s heating and quenching speed need to be appropriately slowed down.
- The heat treatment process system should be selected for different cast aluminum alloys according to their composition, structure, and performance requirements.
Three stages of heat treatment:
- Solution heat treatment: dissolution of soluble phase
- Quenching: The formation of supersaturated solid solution.
- Aging: Precipitation of solute atoms at room temperature or high temperature.
But not all three stages need to be implemented. Some heat treatments include only one or both of these.
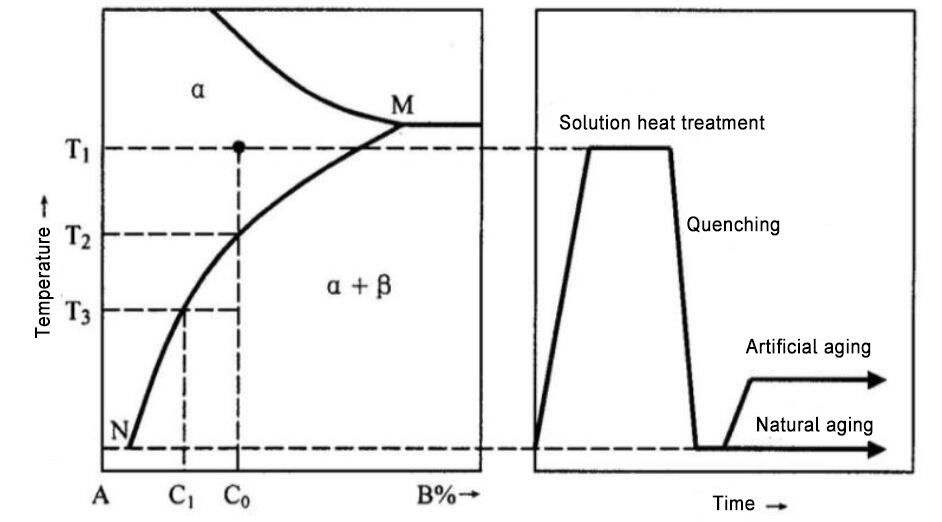
Solution Heat Treatment
For parts that need heat treatment, use a range of 20 to 30 degrees lower than the temperature of the solid and liquid phases. The temperature range of die casting alloys is generally 490 to 540°C (914 to 1004°F). The actual temperature will depend on the specific alloy type.
When heated to close to the solid and liquid phase, Mg, Si, Cu, etc., will dissolve into the solid phase of the aluminum alloy to form a supersaturated solid solution. The supersaturated solid solution will produce eutectic silicon spheroidization at this time. Spherodizes the eutectic silicon particles.
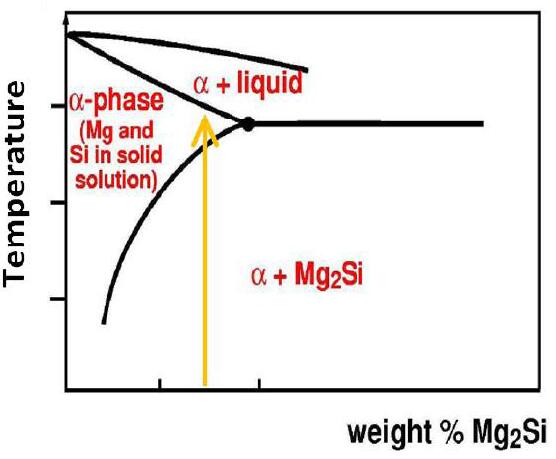
Quenching treatment
Quenching refers to the process of heating the alloy to a temperature close to the solid and liquid phase, and after maintaining it for a period of time, cooling at a rate faster than the precipitation of the second phase from the solid solution to obtain a supersaturated solid solution, followed by rapid cooling to inhibit the strengthening phase in the cooling process. In order to obtain a supersaturated aluminum-based α solid solution, it is prepared for the aging treatment.

- Realize the prerequisites for quenching
The solubility of the strengthening phase in the alloy in aluminum should increase significantly with the increase of temperature. Otherwise, the purpose of solution treatment will not be achieved.
- Changes after quenching
After quenching, the strength and hardness of aluminum alloy do not change much, but the plasticity is high. This process is similar to the quenching of steel, but the quenched structure of aluminum alloy is completely different from that of steel.
During the quenching process of steel, austenite is transformed into martensite, that is, its structure changes; while in aluminum alloy, the matrix only dissolves in the strengthening phase and brings about the change of concentration, and only the high-temperature α phase is forcibly “frozen” to the surface room temperature.
After the aluminum alloy is quenched, the matrix structure has not changed, so it still maintains the original good plasticity characteristics of the aluminum alloy, and because the brittle second phase dissolves into the matrix, the plasticity is further improved, and the strength is due to the matrix alloy elements. The concentration increases and increases; solid solution strengthening is obtained.
Aging Enhancement
The aluminum alloy obtained by solution treatment (or quenching) to obtain a supersaturated solid solution is placed at room temperature or heated to a certain temperature, and the supersaturated solid solution is decomposed to form uniformly distributed nanoparticles. Its strength and hardness increase with time, during its plasticity and toughness decrease. This process is called aging.
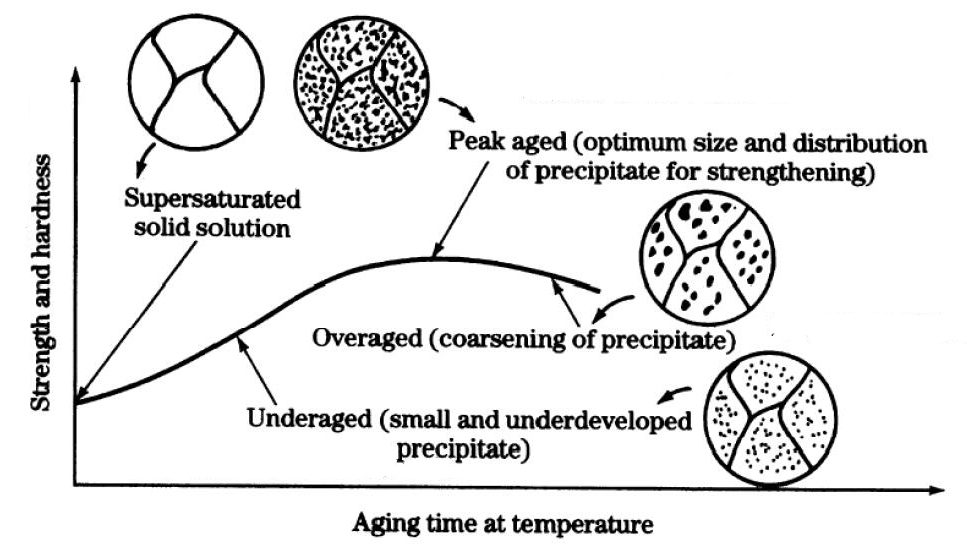
Achieving age-hardening prerequisites
- Alloying elements must have greater solubility in aluminum, and the solubility increases with the increase of temperature
- In the process of aging heat treatment, GP region and transition phase can be formed, and obvious lattice distortion can be caused in the matrix weight.
The basic process of aging hardening;
Taking Al-Cu alloy as an example, the aging sequence is:
α solid solution→α+GP region→α+θ′′→α+θ′→α+θ
Note: The four aging stages mentioned above do not occur at any aging temperature, nor does the aging precipitation must form the GP region first, and then develop to the θ′′ and θ′ phases. When the aging temperature is high, for example, for Al-4Cu alloy, above 250 °C, due to the high atomic activity at this time, the θ phase can be directly formed without going through any intermediate stage; on the contrary, when the temperature is low, such as below 130 °C , mainly form the GP region, and it is difficult to obtain other phases.
Aging Enhanced Classification
Aging enhancement is divided into natural aging and artificial aging. Then, artificial aging can be divided into under-aging, complete aging and over-aging
Natural aging: room temperature (high strength, good plasticity, and toughness, corrosion resistance is also better than artificial aging, and its heat treatment process is simple)
Artificial aging: heating (the strength of the alloy, especially the yield strength, is higher than that of natural aging, but the plasticity and corrosion resistance are slightly worse)
Under-aging: that is, incomplete aging, heating the casting to 150-170 ° C, and holding the temperature for 3-5 hours to obtain a heat treatment process with good tensile strength, good plasticity, and toughness, but low corrosion resistance.
Complete aging: heat the casting to 175-185°C and keep it for 5-24h to obtain a heat treatment process with sufficient tensile strength (i.e., the highest hardness) but low elongation.
Over-aging: The casting is heated to 190-230 ℃ and kept for 4-9 hours so that the strength is reduced and the plasticity is improved to obtain better stress resistance and corrosion resistance, also known as stabilized tempering.
Age hardening law
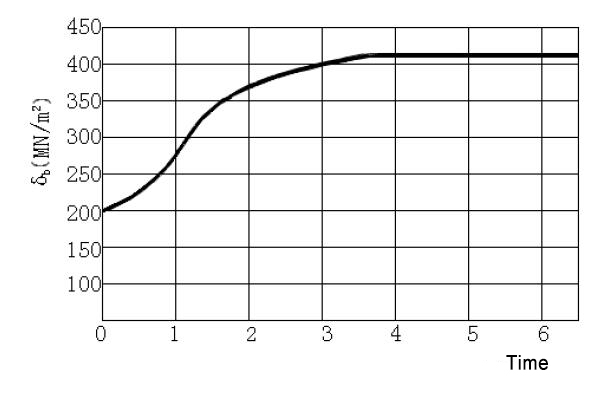
- The higher the aging temperature, the lower the peak strength and the smaller the strengthening effect.
- The higher the aging temperature, the faster the aging speed and the shorter the time required for the peak intensity to appear.
- The low temperature keeps the supersaturated solid solution obtained by solution treatment relatively stable and inhibits aging progress.
A356-T4 170℃ aging treatment:
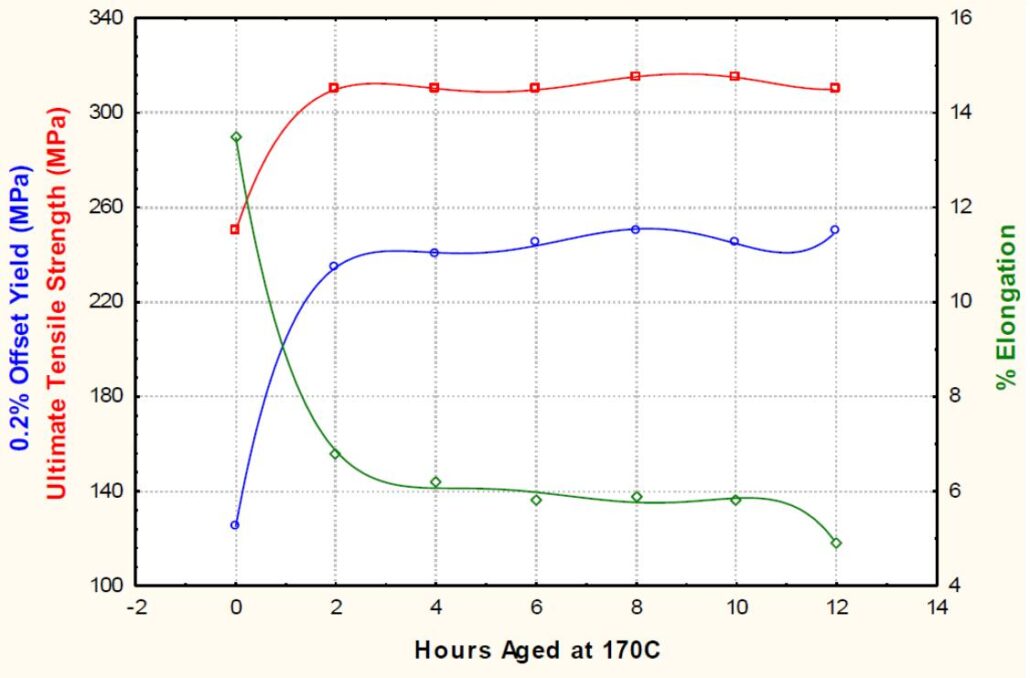
Factors Affecting Timeliness
- Influence of the residence time from quenching to artificial failure Generally, if placed for a period of time, the strength will decrease, and the plasticity will increase.
- The influence of the chemical composition of the alloy. The composition of the alloying elements should be dissolved in a solid solution, and the solid solution should change with temperature.
- The effect of aging temperature. This determines the critical nuclei’s size, number, composition, and aggregation growth rate.
- The influence of the solid solution treatment process of the alloy.