Heat Treatment of Die Castings-3
1.Common heat treatment process for die castings
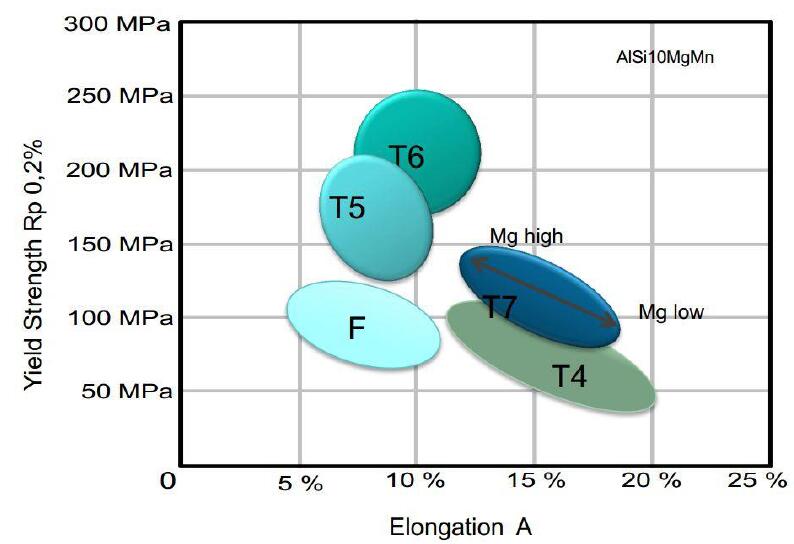
- T4 high ductility, medium strength
- T5 medium ductility, high strength
- T6 medium ductility high strength
- T7 high ductility medium strength
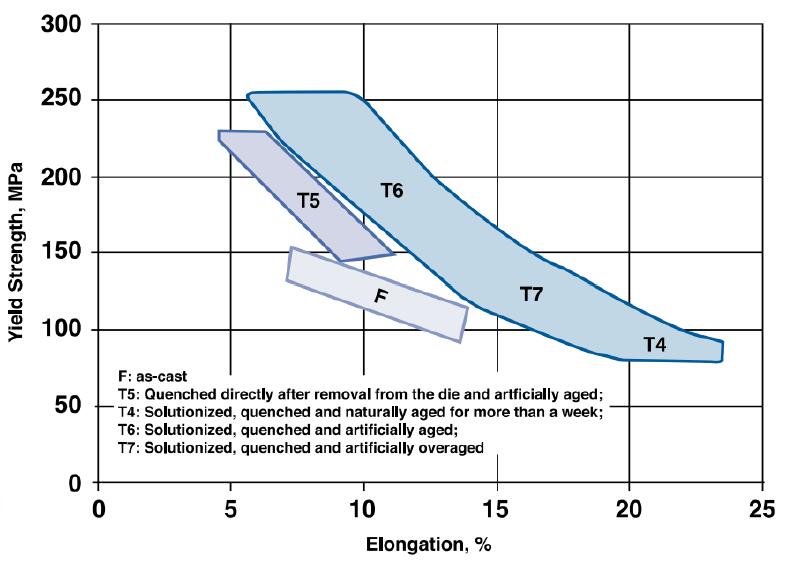
If heat treatment is so good, why is traditional casting not heat treated?
This is because heat treatment will cause blistering on the surface of the casting.
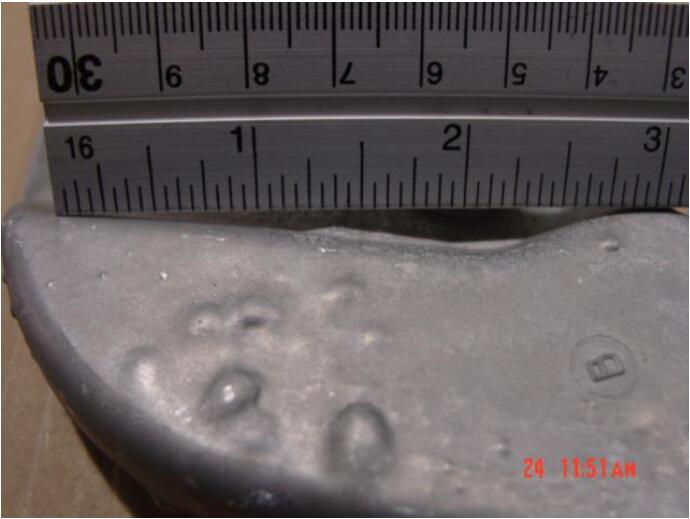
Why is it bubbling?
First of all, there should be defects under the die casting surface, with air bubbles or pores generated by the release agent. The pressure during the production of die castings is very high, reaching 40Mpa~140Mpa.
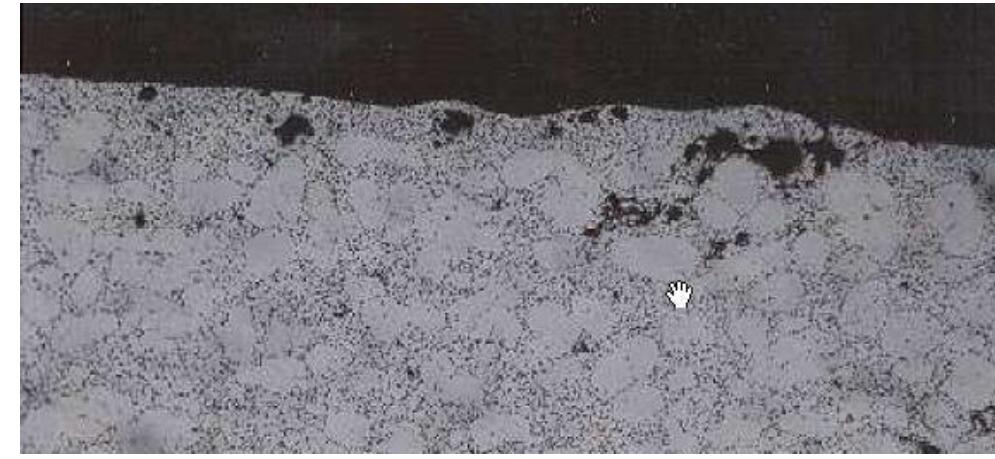
So there is the same pressure in the pores below the surface. During solution treatment, as the temperature increases, the pressure of the pores inside the casting increases rapidly. When the pressure exceeds the strength of the casting, blistering occurs on the surface of the casting.
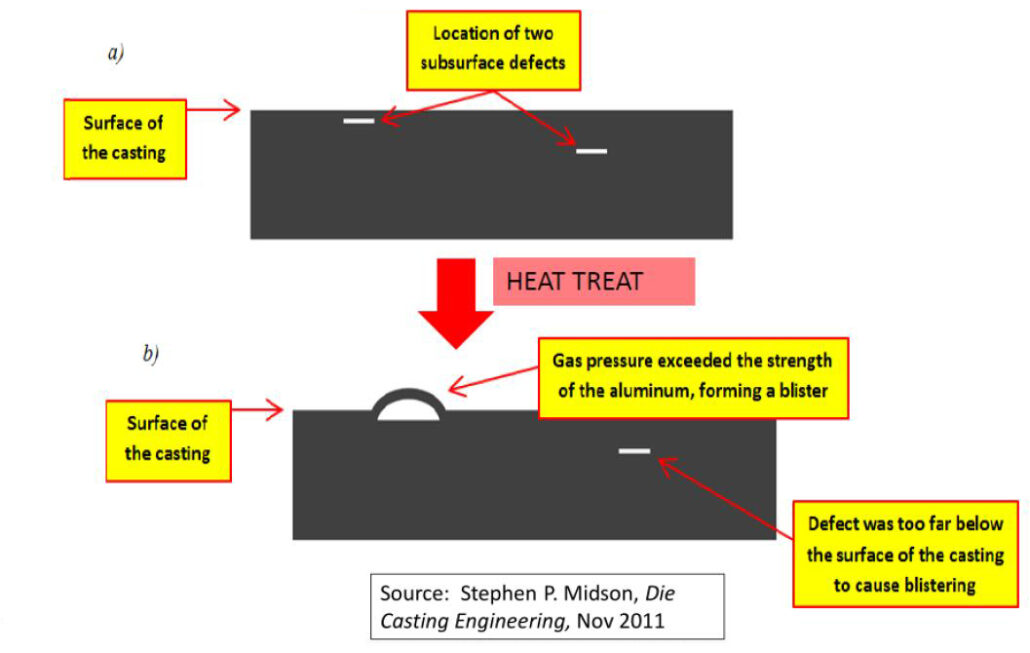
2.T6 heat treatment of conventional die castings
Ordinary heat treatment methods are definitely not acceptable, which will lead to blistering of die castings. However, Australian research has shown that conventional die castings can be T6 treated via the following scenario.
- If solution heat treatment can be performed at a lower temperature, 430 to 480°C (806 to 896°F)
- Shorten the solution time to 15 minutes
After the above two changes, blistering of die castings can be avoided. The quenching and aging processes are consistent with the normal T6 heat treatment.
Properties of 380 alloy, corresponding yield strength, tensile strength, and elongation under different heat treatment methods
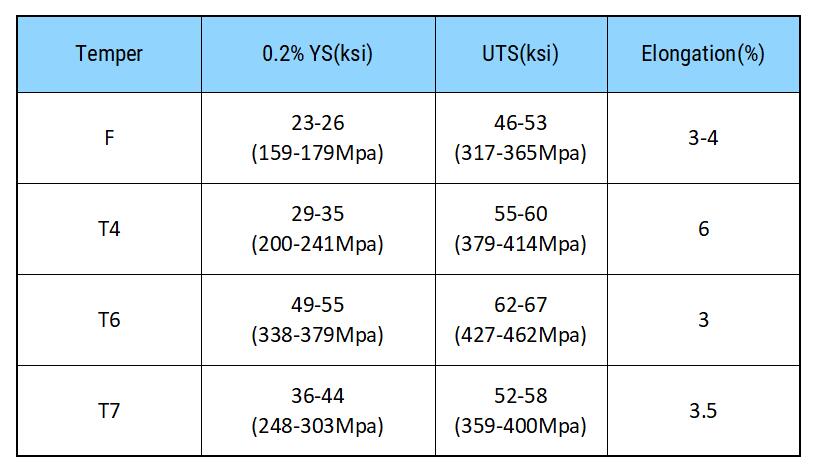
F is the unheated state. It can be seen that the yield strength and tensile strength can be greatly improved after T6 heat treatment.
Properties of A360 alloy, corresponding yield strength, tensile strength, and elongation under different heat treatment methods
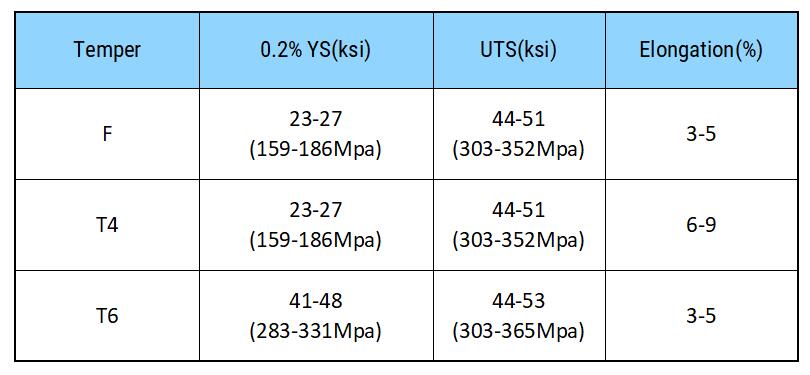
The T6 heat treatment mentioned here belongs to Australia’s Commonwealth Scientific and Industrial Research Organization. If you use this technology, you need to pay CSIRO patent fees. Practically using this heat treatment process is not easy:
- It is not easy to meet the strict temperature range of solution heat treatment.
- The casting is removed from the solution heat treatment furnace and quenched within 15 to 30 seconds. Generally, it needs to be carried out in a live bottom furnace. Normally achieved using a drop bottom furnace requires a certain investment in equipment. The Australian researchers reported using a fluidized bed furnace to heat treat their castings requiring this equipment.
- Die castings after solid-liquid heat treatment will deform during quenching. Unless the quenching speed control is reasonable, the deformation will increase.
- After the solid-liquid heat treatment, there will still be some waste products.
3.T5 Heat Treatment of Conventional Die Castings
The T5 heat treatment is relatively simple. The casting is taken out from the mold cavity and quenched with water immediately without complicated solution heat treatment.
Take 380 alloys as an example to illustrate the T5 heat treatment.
Different types of 380 alloys: mainly the composition of Mg and Fe elements is different
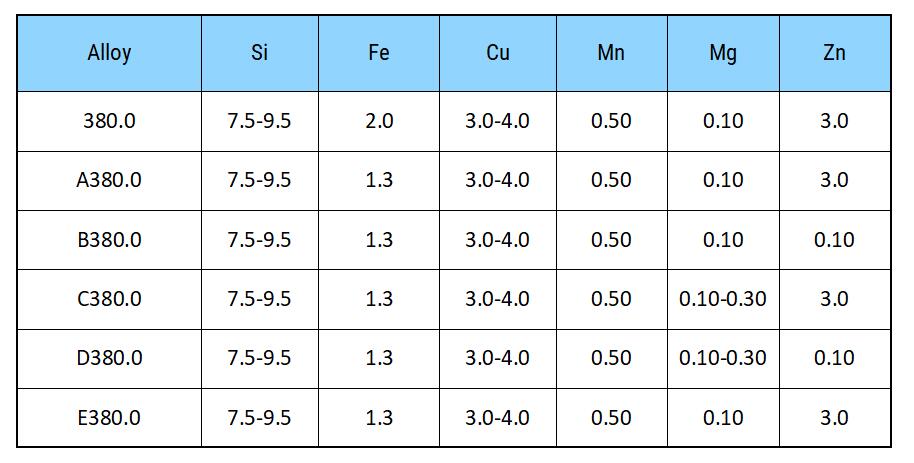
Different magnesium content has a great influence on the properties. The properties of the alloy after T5 treatment are shown in the figure
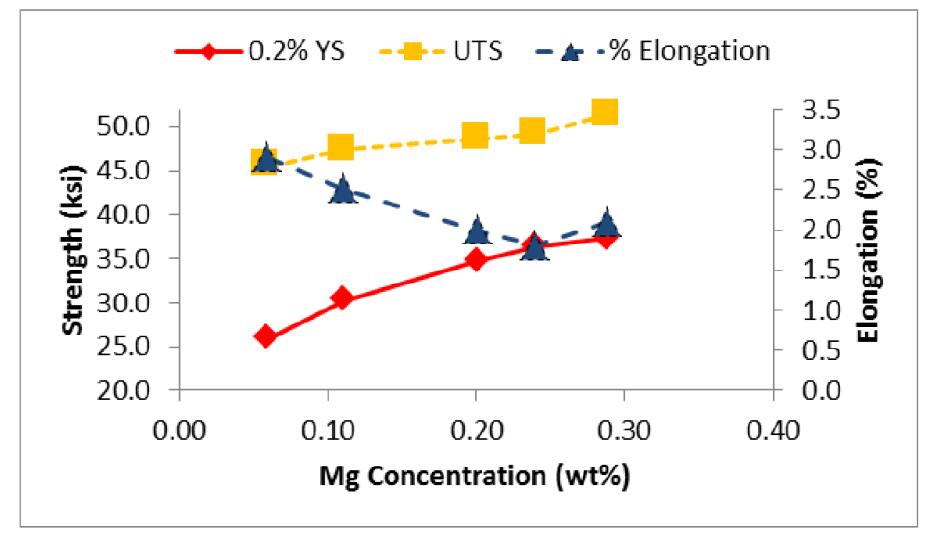
- When the magnesium content (0.06%) is the lowest, the mechanical properties do not change after T5 heat treatment, which is the same as the casting without heat treatment.
- The Mg content is between 0.11% and 0.29% for other alloys. After T5 treatment, all properties are improved.
- The ratio of performance improvement is related to the ratio of magnesium content.
- In order to improve the strength, the magnesium content can be increased to 0.3%.
C380 conventional die casting, aging treatment at different temperatures:
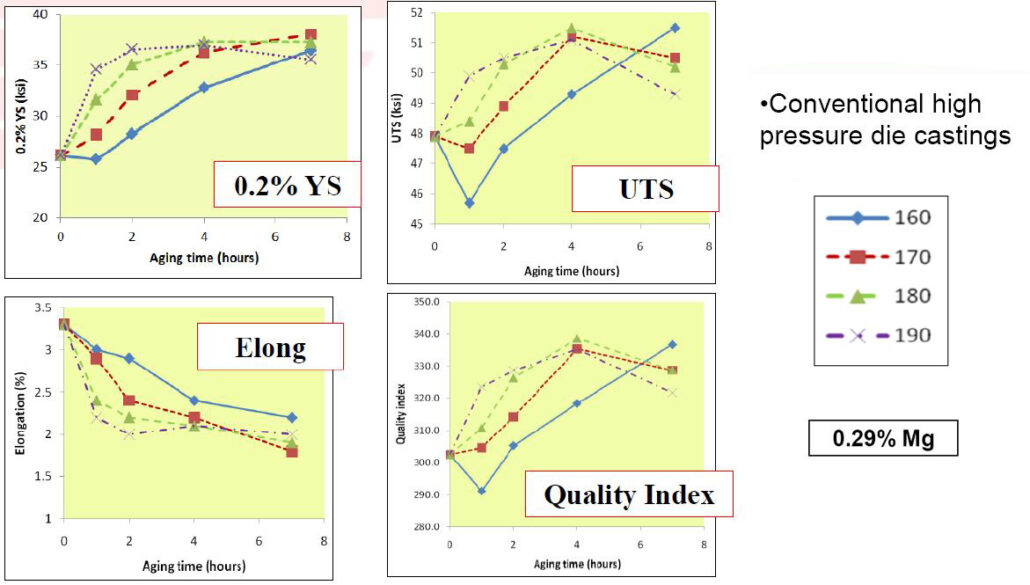
in conclusion:
- The best T5 treatment conditions: conventional C380 alloy with 0.29% magnesium content—180 ℃ through 4 hours of aging treatment.
- Yield strength -37 KSI (255Mpa), which is 43% higher than that of ordinary castings and 60% higher than that of A380.
- Tensile strength increased by 11%
- The elongation is reduced to 2.1% from 3.3%.
2.Conventional Low Iron Die Casting Alloy Heat Treatment
Die castings are generally less ductile, mainly due to the following two factors:
- There are residual pores in the casting
- The iron content in the alloy is higher
Why is the iron content high in the alloy? In order to reduce the burning loss of aluminum alloy liquid to mold steel, the conventional iron content is between 0.8 and 1.3%.
Current research has concluded that other elements can also reduce burn loss. Example: Manganese and Strontium
There are currently two classes of low iron alloys:
- New cast aluminum alloy 367 & 368 Mercalloy 367 & 368
- 380 with low iron (experimental stage)
– Reduce the iron content in the alloy to a maximum of 0.25%
– Adjustment by strontium and manganese: 0.05~0.07% strontium and 0.25~0.35% manganese
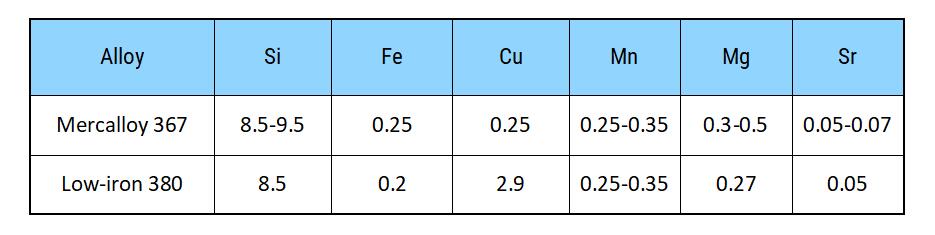
Properties of low iron 380 alloys after T5 treatment
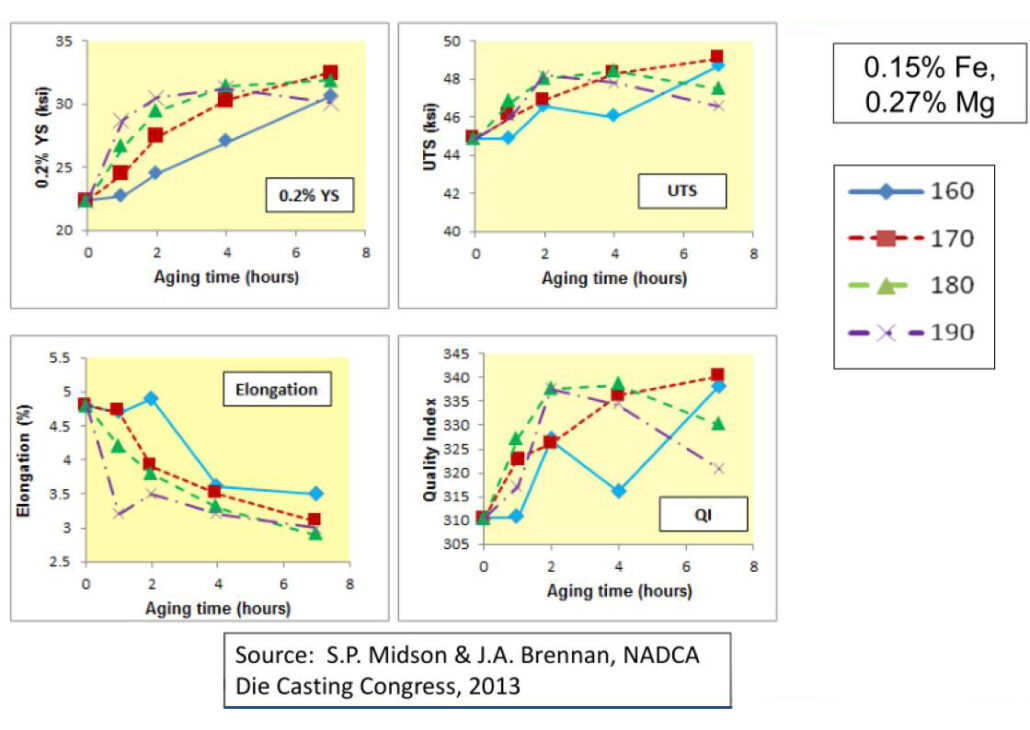
Low Iron Alloy 380 - Peak Strength
The best T5 heat treatment condition is at 170℃:
- Yield strength increased by 45%
- Peak tensile strength increased by only 4ksi.
- Elongation decreased from 4.8% to 3.3%
- Also treated by T5, the ductility of low iron 380 alloy is better than that of normal iron 380 alloy
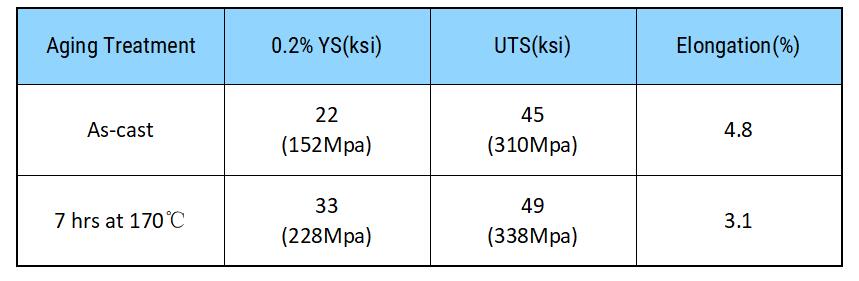
3.Heat Treatment of High Vacuum Die Castings
In vacuum die casting, the cavity and pressure chamber are evacuated before injection, thereby reducing the residual holes in the casting by reducing the entrainment of gas.
Blistering is less likely to occur when less gas is involved in the casting. Products can be treated with full or partial T6.
Alloys with low iron content available: Silafont36 and Aural
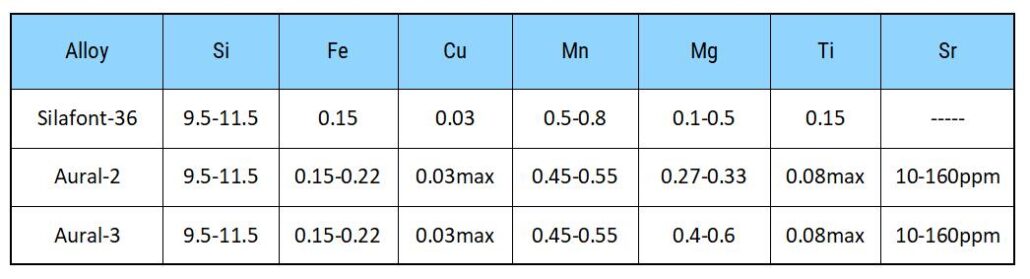
T6 heat treatment: partial solution heat treatment, temperature 460 ℃. Using air quenching (air quench) can reduce castings’ deformation—aging treatment.
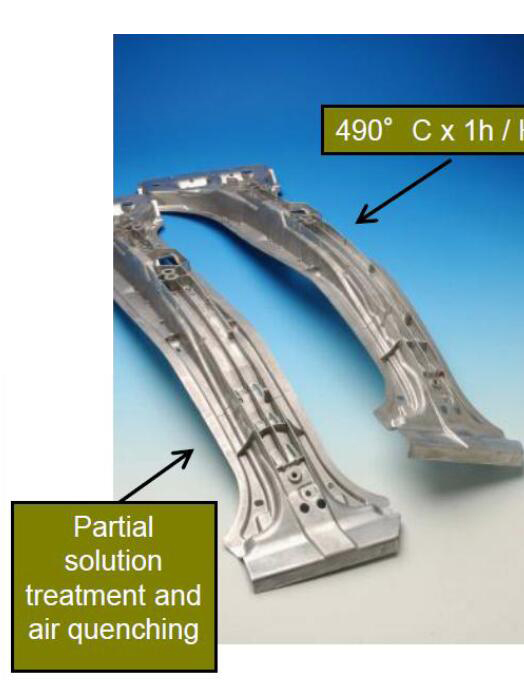
strength, tensile strength, and elongation corresponding to different heat treatment methods
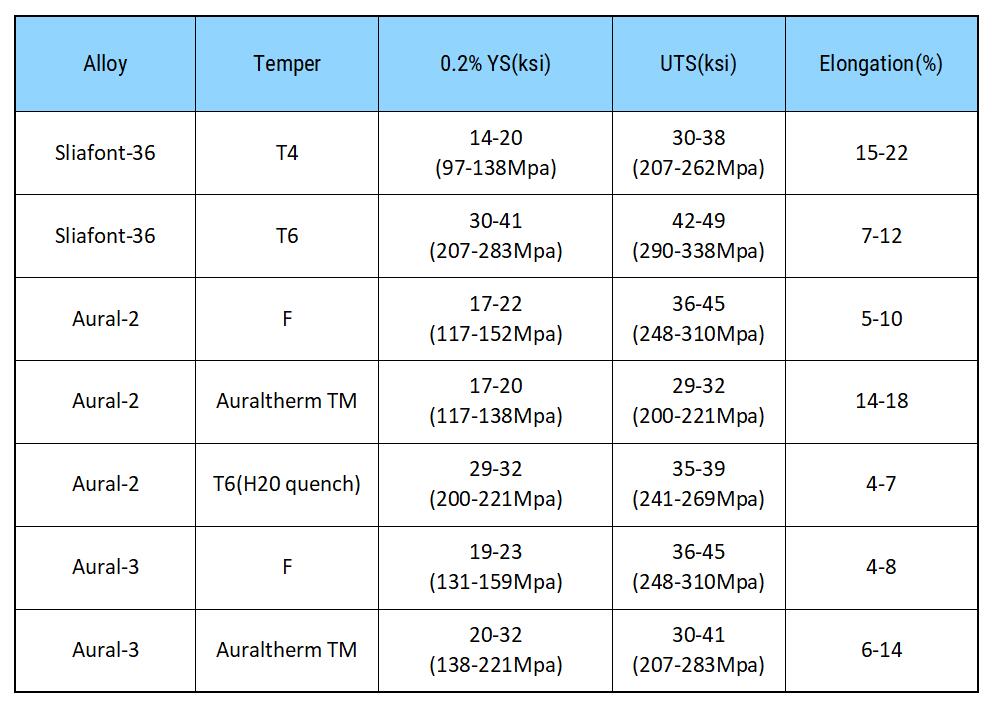
4.Heat Treatment of High-Density Die Castings
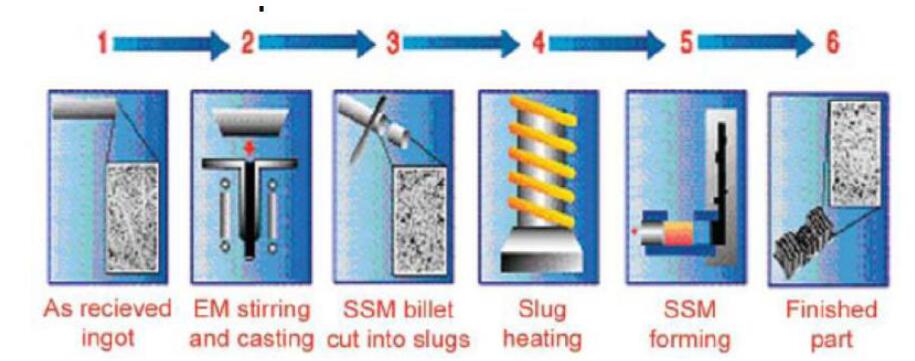
Commonly used high-density die casting processes are: semi-solid die casting and squeeze casting
Process features:
- Fill the mold with laminar flow to avoid entrainment caused by turbulent flow.
- Use high casting pressure and a large gate to improve shrinkage cavity defects.
- Alloys with lower iron content (max. 0.25%) to be cast.
- Can be heat treated T4, T5 and T6
Semi-solid die casting:
- Most die casting processes use full liquid filling.
- The material used in semi-solid die-casting is 50% liquid and 50% solid.
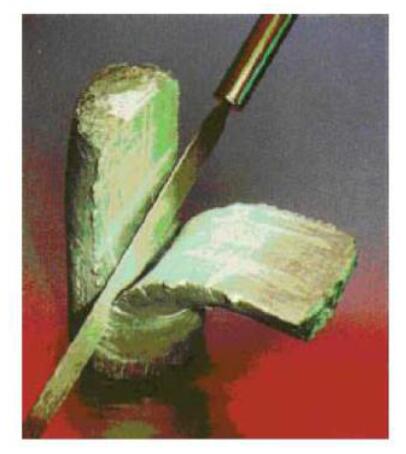
Thixcasting processing steps(left) lead to a re-heated Billet ready to cast that is soft enough to be easily cut with a knife.
Squeeze casting:
Use low-speed injection to avoid filling disorder.
In semi-solid die casting and squeeze casting, blistering is rare. Therefore, the casting can be fully heat treated. 500-540℃(932~1004℉) can last for 2~12 hours.