Maintenance and Care of Die Casting Machines 1
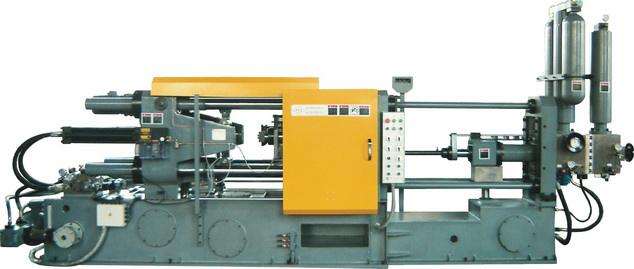
Question 1: The relationship between the die casting machine and us?
We can regard the die casting machine as a living body; from the purchase of the machine to the scrapping of the machine, it has gone through a complete life cycle.
Our factory relies on die-casting machines to make money, but we cannot treat die-casting machines as slaves. We need to take good care of the die casting machine, and it needs to be maintained and repaired frequently. Once a problem occurs, be sure to stop it from checking and fixing it.
In some ways, die casting machines also represent the business itself. If the die-casting machine is well managed and pays attention to safety and hygiene at all times, the development of the enterprise will be very good. On the other hand, if the die-casting machine is not well maintained, the machine is full of oil stains, and the bottom surface is full of dirty water, then it can be seen that the management of the enterprise is still imperfect, and the quality of the products cannot be guaranteed.
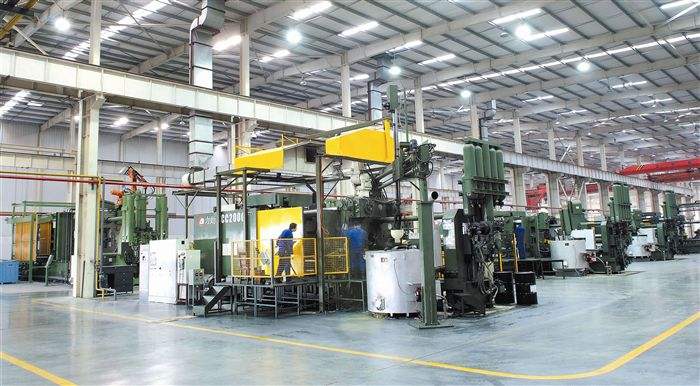
Question 2: Who will maintain the die casting machine? Operator or mechanic?
There are some problems with the die-casting machine. The employees often blame each other, refuse to take responsibility, and do not know who is responsible for the maintenance. Our common principles are:
- Daily maintenance needs to be performed by an operator.
- Professional maintenance requires a mechanic.
There must be a clear division of labor and responsibilities so that the on-site work can be carried out smoothly.
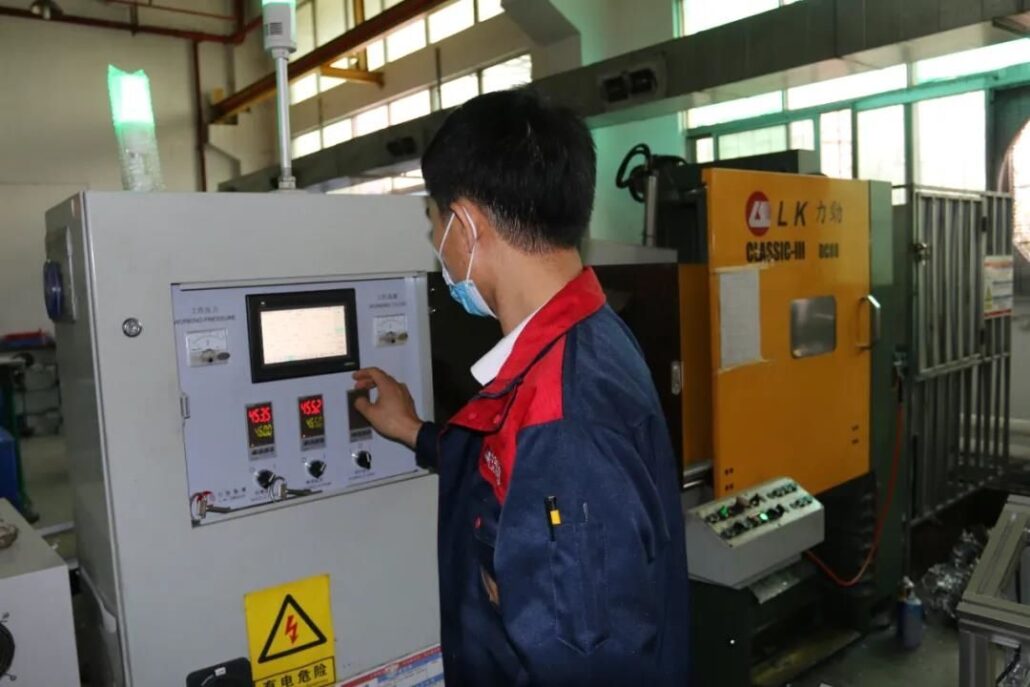
Before repairing the die casting machine, matters needing attention include;
1) Qualified personnel: Repair work must be carried out by trained and qualified professionals.
2) Power outage listing: During maintenance, power off and press the emergency stop switch. And hang warning signs such as “Maintenance in progress, closing is prohibited.” Prevent other personnel from closing the switch and turning on the power.
3) Anti-slip: During maintenance, avoid stepping on non-stressed parts such as sheet metal parts, and be careful to prevent slipping.
4) Pressure relief: The oil must be unloaded before disassembling the hydraulic parts to ensure that the pressure oil in the high-pressure oil circuit is completely discharged, such as the accumulator. The pressure oil must be released first when removing any high-pressure components, such as hydraulic valves, oil pipes, etc. Since there may be residual pressure inside, when loosening the screw, it should be loosened slowly, and the screw can be removed after the residual pressure is discharged—all loose.
5) Tools: Do not beat the Colin pillar arbitrarily, and use special tools such as copper rods
6) Restoring safety components: Safety doors and other safety components removed during maintenance need to be restored in time to prevent accidents caused by operational errors.
7) Remove the plunger tip: The plunger tip should be removed during maintenance to prevent the plunger tip from malfunctioning due to maintenance errors.
8) Prevent burns: Prevent burns when disassembling hot parts.
9) Protective ground wire:Try to avoid removing the protective grounding wire during electrical maintenance. When it must be removed, it should be removed last, and when it is restored, it should be restored first.
10) Adjust parameters: The parameters are adjusted by special personnel, and it is strictly forbidden to adjust the parameters when the machine is in production.
11) Mould: Carefully check the unused mold, and reduce the injection pressure and speed during the initial die-casting.
For the maintenance of the die casting machine, we mainly start from eight aspects:
1)The appearance of die casting machine
2)Hydraulic system
3)Electrical part
4)Clamping part
5)Injection part
6)Lubrication part
7)Cooling system
8)High-temperature parts system
1.Appearance maintenance of die casting machine
1.1 Clean up/Daily
Before leaving work every day, the alloy chips and oil stains on the machine must be cleaned up, and attention should be paid to the cleaning of the elbow (machine hinge), Colin column, template, and injection chamber (feeding barrel).
1.2 Check for oil leaks/weekly
Check whether there is oil leakage at the oil tank, hydraulic pump, hydraulic cylinder, hydraulic motor, hydraulic valve, pipe joint and pressure gauge, and the connection of the oil circuit board. If there is, it should be dealt with in time.
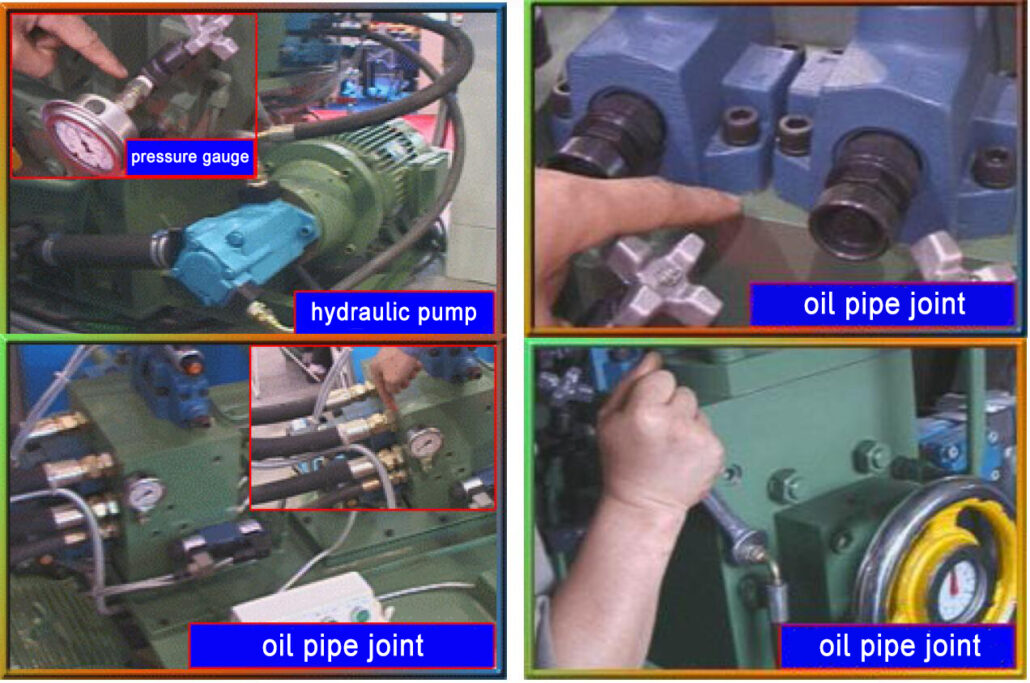
2.Hydraulic System
The hydraulic system of the die-casting machine is particularly important. For example, 70% of the failure of the die-casting machine is caused by hydraulic oil.
Question 3: What problems can be caused by poor quality hydraulic oil?
Inferior hydraulic oil contains a lot of solid particles and has poor wear resistance. It directly leads to the wear of the spool and valve sleeve of the hydraulic valve, causing the hydraulic oil to leak out. In this way, the oil pressure cannot reach the set value during the die-casting process, and the quality of the products produced is unqualified.
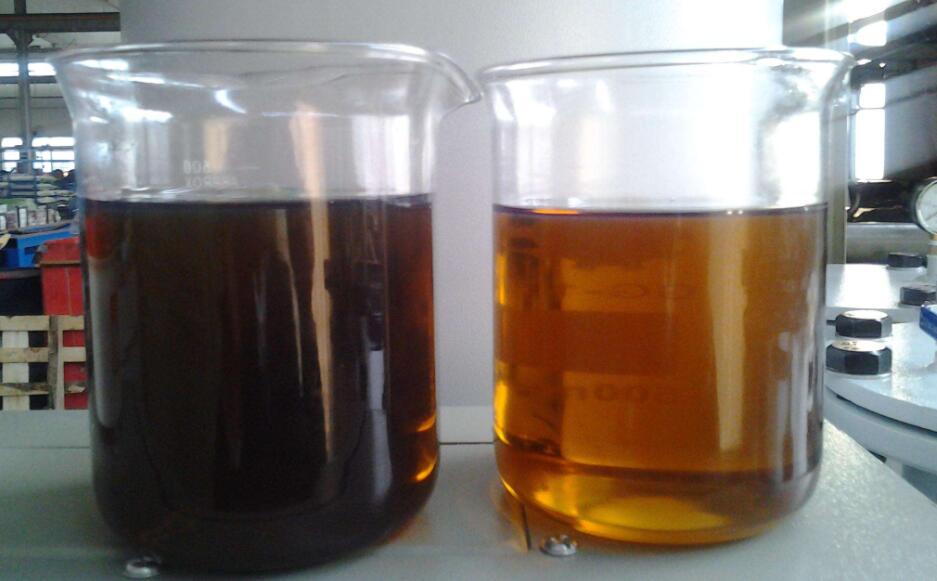
Question 4: What are the two types of hydraulic oil?
- Flame retardant hydraulic oil (water-soluble hydraulic oil)
- Mineral hydraulic oil
Precautions:
- Either type can be used, but one thing to note is that once a certain type is selected, it must not be used in combination, and the type of oil cannot be changed after cleaning.
- Compared with mineral oil, the flame retardant is safer, and it is not easy to burn if the oil leaks and falls into the furnace.
- Generally, when the die-casting machine is designed, there will be instructions on which oil can be used, and the replacement of oil needs to be approved by the equipment manufacturer.
Question 5: Oil change interval and how to change the oil? Oil change interval
It is recommended to once a year, such as during the holiday period. This awareness should be established. 1-day oil change guarantees 364-day machine performance.
How to change the oil
Method 1: Directly replace all the oil
Method 2: You can replace part of the oil,
Operation:
- Make a container roughly divided into upper, middle, and lower parts, and install oil drains in the middle and lower parts.
- Pour the oil out of the die-casting machine into the container and let it stand for more than 24 hours.
- Skim off the oil that floats, and don’t leave the trash at the bottom.
- Open the oil drain and pour it into the die casting machine again.
- Add some new oil to ensure the oil level (about 2/3 or more).
Question 6: We also changed the oil, but why didn't it work?
- Not only the system of an oil change but also the concept of an oil change. Is it “I want to change it” or “I want to change”?
- “I want to change it” may be to put the oil out and then pour it back when you mess with it, and the task is completed, which is actually useless.
- “I want to change” is the concept that you need to change the oil. Only in this way can you do things well and show the effect of the oil change.
- Be sure to find a serious and responsible person to spend a day doing it well.
Question 7: How to clean the fuel tank?
It is not recommended to use sand when cleaning the fuel tank. The effect of fine sand is good, but if the sand remains inside, it will cause great damage to the valve and cannot be detected. A cotton cloth is recommended for cleaning. The cleaning staff must be careful.
Question 8: Regular Cleaning or Replacement - Filters (Weekly Checks)
When the equipment has a filter indicator, always check the filter’s indicator. When the indicator pointer is in the green area, it is normal. In the yellow area, it is slightly blocked, and in the red area, it is severely blocked. When the pointer enters the yellow area, the filter element must be cleaned.
The filter screen filters the oil internally to ensure the oil’s quality further. Therefore, it is necessary to regularly check whether the filter screen has too many impurities or blockages. If there is any problem, it should be cleaned or replaced.
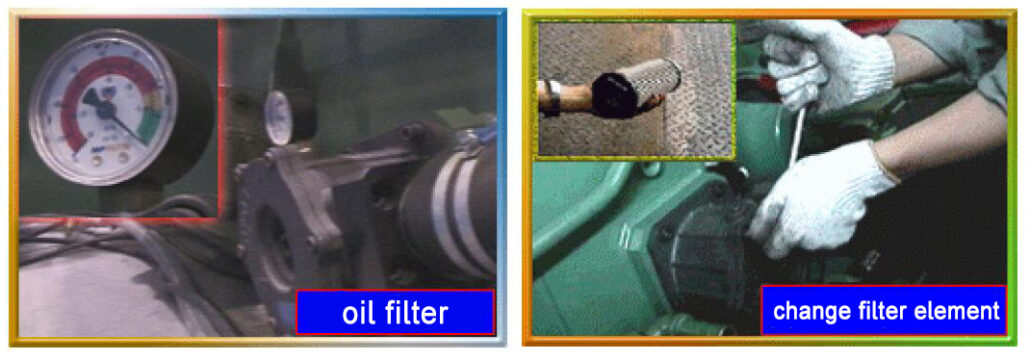
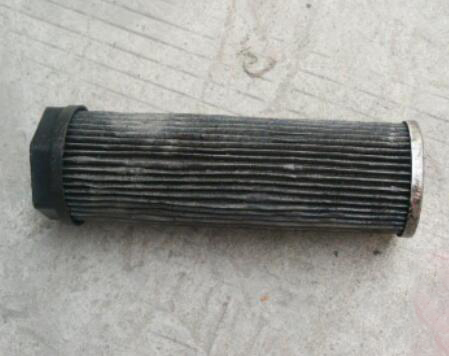
Question 9: What is a reasonable oil level?
It is recommended to rely on the upper limit, at least 2/3. If the oil level is too low, it is like a person not having enough to eat. Also, going to work will impact the performance and life of the machine. So check the oil level frequently.
Question 10: How to control the oil temperature?
Die-casting machines have coolers to cool the hydraulic oil, but we still need to check the oil temperature and the effect of the cooler frequently.
Temperature difference between inlet and outlet: about 10°
The starting temperature of hydraulic oil: 18° (the temperature is too low, the viscosity is relatively high, the resistance is large, and it is easy to increase the damage of the valve)
Working temperature: 30°~40° is recommended.
Warning temperature: over 45°
Stop working: over 55°.
The high-temperature work of hydraulic oil will cause great damage to the machine. This is because, on the one hand, the pressure is not easy to build up, and on the other hand, it is easy to accelerate the aging of the sealing ring. In this way, it starts to leak when the pressure is high, and it is more difficult to produce a good product.
Question 11: When changing molds, prevent hydraulic oil system contamination.
When changing the mold, if there is a core-pulling cylinder, the interface between the core-pulling cylinder and the oil pipe needs to be blocked with a plug to prevent the garbage from being brought into the hydraulic system of the die-casting machine.
Question 12: Hydraulic part screws/semi-annual inspection
Check the oil pipe joints, oil valve mounting screws, and other joints every six months. If they are loose, they should be tightened in time to prevent leakage or air from entering the hydraulic system.
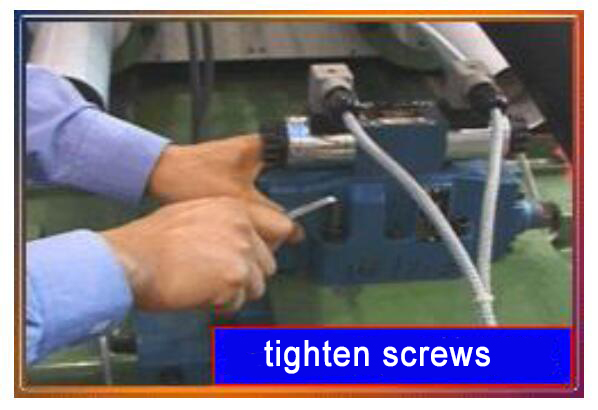
Question 13: Ways to Check Nitrogen Pressure / Monthly Check
Turn off the motor, press the emergency stop button, and unscrew the stop valve (some models can automatically discharge the load). When the oil pressure drops to zero, the nitrogen pressure gauge indicates the accumulator’s nitrogen pressure and each nitrogen pressure The values specified in the machine instruction manual must be met.
For example, the DCC400 horizontal cold chamber die casting machine has a nitrogen pressure of 90-100 bar in the fast-injection accumulator and a nitrogen pressure of 80-90 bar in the booster accumulator.
DC88 and DC160 hot chamber die casting machines have no nitrogen pressure gauge. Instead, observe the injection pressure gauge when the pressure is released. When the pressure drops to a certain value, it will accelerate and drop back to zero. This value is the nitrogen pressure value. The nitrogen pressure of the feeding accumulator is 40-45 bar.
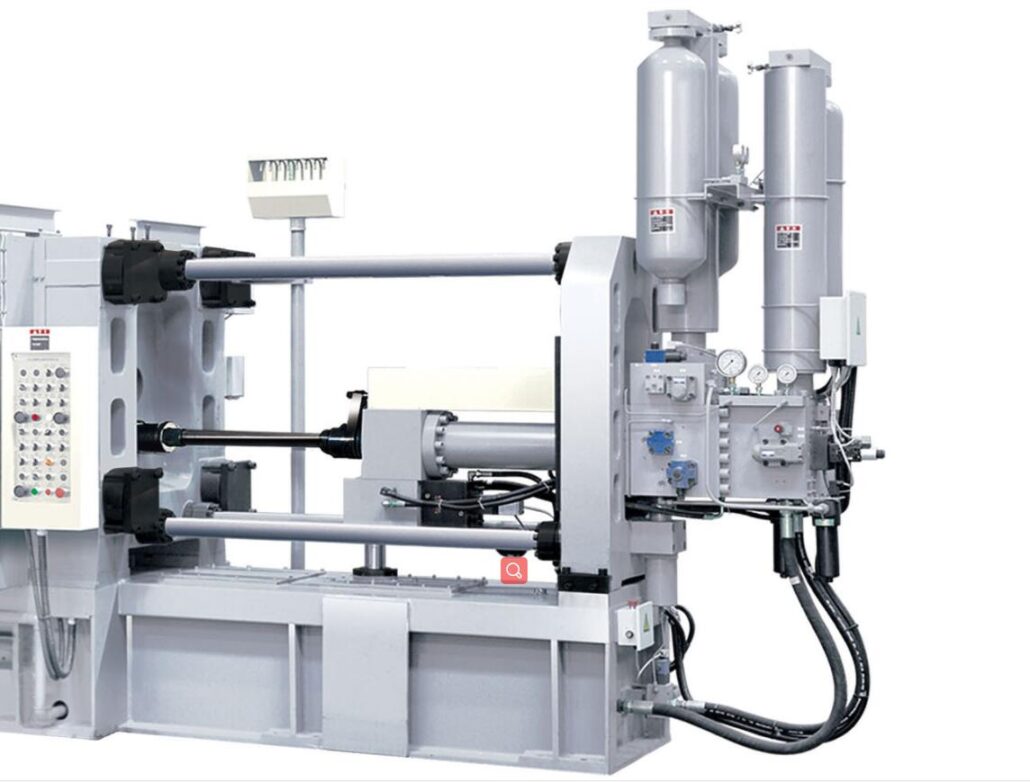