Die Casting Defects - Hard Spot
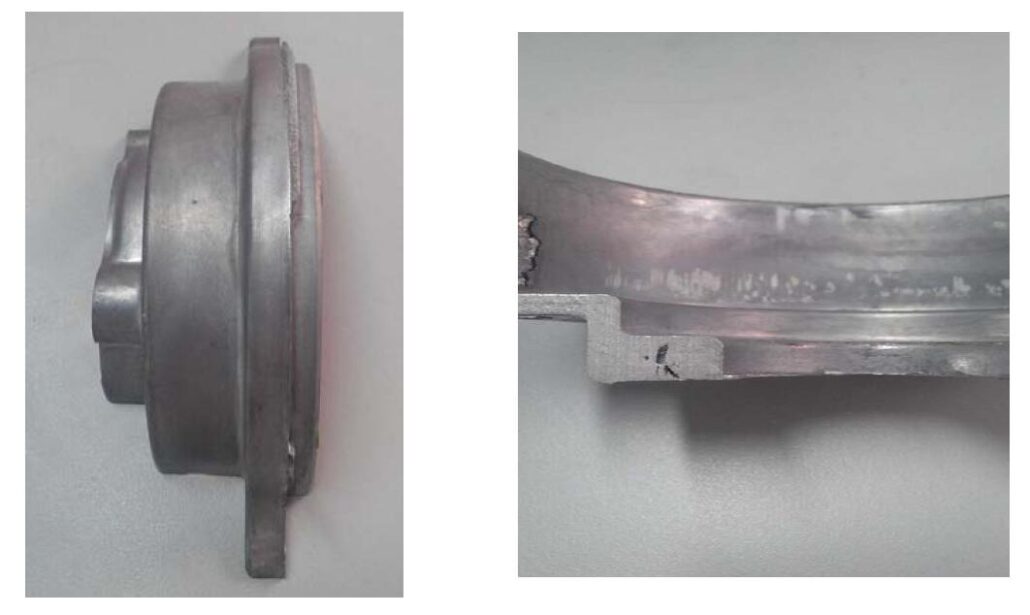
If there are hard spots in the die casting, it will bring us some problems in the subsequent processing. Some of such problems are listed thus:
- The casting surface is rough.
- The machining accuracy of die castings is reduced, and the dimensions are out of tolerance.
- The cutting resistance is increased, and the normal production cannot be serious.
- The tool is severely worn, and the cutting edge is cracked.
Today, let's discuss the "hard spot" in die casting, its causes, and solutions.
1. What is a hard point?
Definition: Hard spots are small particles or lumps on die castings whose hardness is higher than that of the aluminum body and play a harmful role in the machining process.
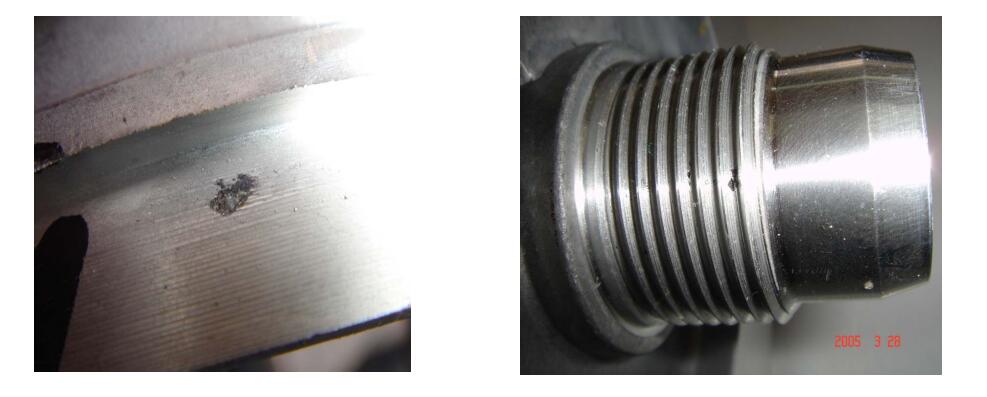
2. Classification of hardpoints
For hardpoints, the current unified understanding is to classify hard points into five categories:
1) Metal oxides
2) Metal sludge
3) Refractory material
4) Primary silicon phase
5) Secondary oxide
3. Metal oxides
The main components are inclusions such as alumina, which are usually porous alumina compounds or non-porous dark alumina compounds.
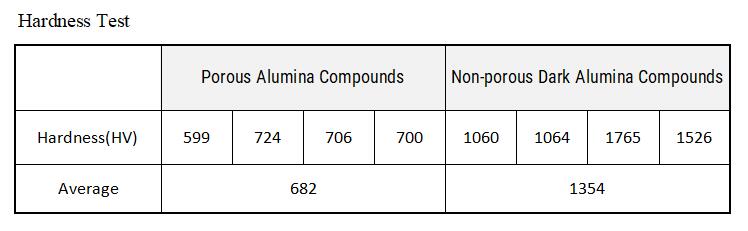
The results show that the hardness of any oxide is higher than that of the aluminum matrix. The former is 10 times higher than the aluminum matrix microhardness (HV68), and the latter is 20 times higher. So the hardpoint is very hard.
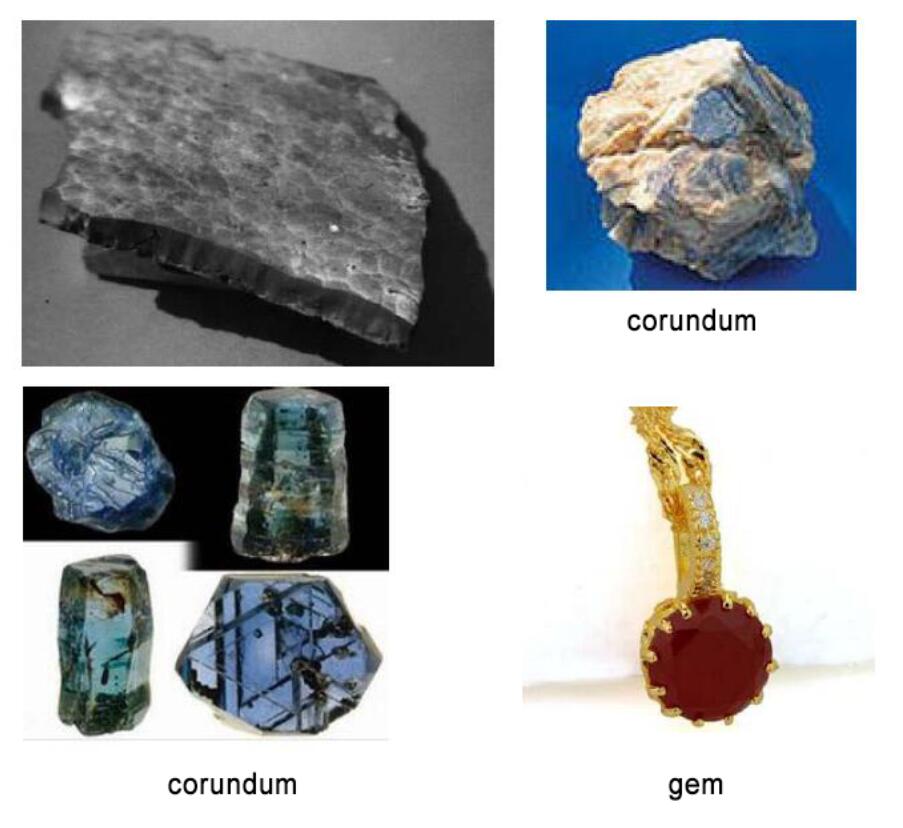
Metal oxides can be processed into corundum, and corundum can be processed into very hard gemstones. So “gem” and “hard point” are homogeneous and heterogeneous.
Reasons for the formation of metal oxides:
- The liquid level fluctuates violently during the melting process of molten aluminum. The aluminum alloy liquid reacts with oxygen and water in the air to form aluminum oxide.
- The melting temperature is too high, which promotes the accelerated oxidation of molten aluminum.
- The molten aluminum stays in the furnace for too long, resulting in a large amount of alumina.
- Too much return material is added, resulting in too many impurities in molten aluminum.
Responses
– Take a suitable melting temperature, do not blindly increase the temperature of the alloy liquid.
Melting temperature: 680~700 degrees,
Refining temperature: 720~740 degrees,
Insulation temperature: 680~700 degrees.
– Refining and removing slag from the melt to improve the refining process (e.g. GBF method – rotary rotor jet method).
– Each furnace corresponds to the corresponding aluminum alloy grade.
– Stopping production for more than 8 hours (strictly 4 hours) must be re-refined and degassed, and tested for ingredients.
– Strictly control the proportion of the returned material (not more than 1/3), and do a good job of cleaning and drying the returned material.
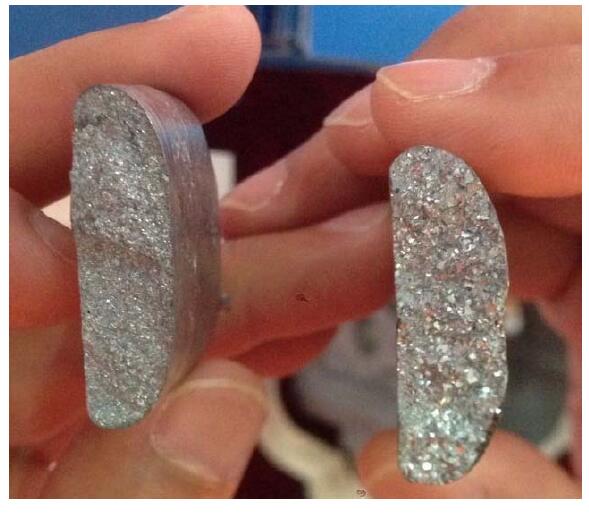
4. Metal Sludge
Metal sludge is mainly formed when the temperature of the alloy liquid decreases.
For example, when aluminum ingots are put into the furnace, the temperature of the feeding position will fluctuate violently, and the sludge will be generated here.
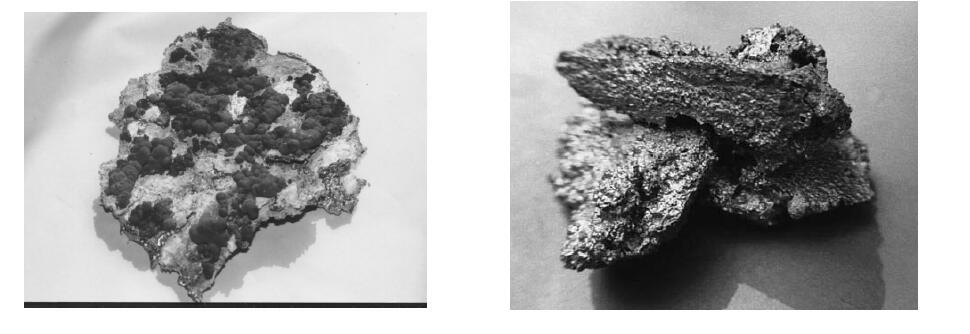
Metal Sludge Composition Analysis
– Metal sludge is actually a metal impurity phase of AlSiFeMn phase.
– Its microhardness (HV630) is about 9 times that of an aluminum body.
– It is denser than molten aluminum and will deposit on the bottom of molten aluminum.
– Too much time will also increase the silt.
Responses
– Strictly control the temperature of alloy liquid.
Melting temperature: 680~700 degrees,
Refining temperature: 720~740 degrees,
Insulation temperature: 680~700 degrees.
– Preheat the alloy ingot before charging.
– Take care to preheat the transport oven bake.
– Preheat alloy ingots, spoons, slag removal tools, degassing tools, etc., before operation.
– It is strictly forbidden to add cold material into the holding furnace or the melting furnace.
– Furnace improvements, grooves and baffles at the bottom.
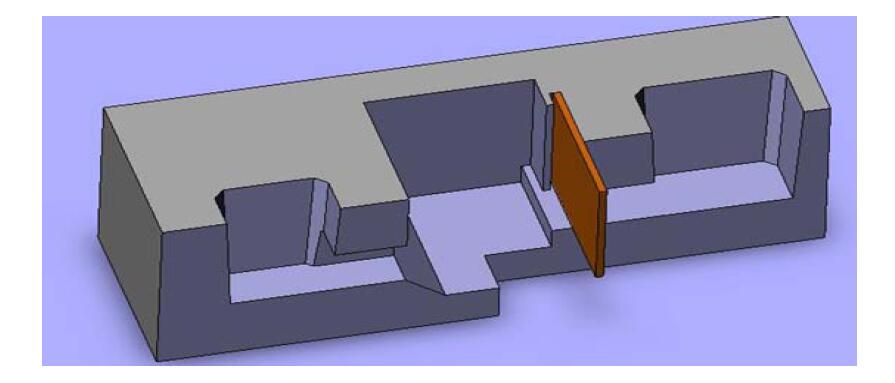
5. Refractory material
When the temperature is too high, or the molten aluminum contains salts such as sodium salt and potassium salt, the inner wall of the furnace crucible are likely to react with the molten aluminum, resulting in nodules on the furnace wall, and the nodule fragments are likely to fall into the molten aluminum and eventually enter the die casting to form hard spots.
When the inner wall of the crucible is rich in SiO2, nodules are more likely to be formed.
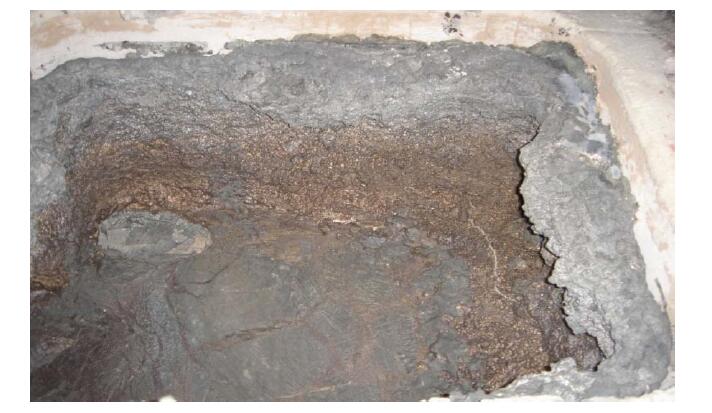
Composition Analysis
– Analysis of its composition found that the nodules are aluminum silicate compounds (Al2O3·XSiO2), and their microhardness is about HV1300, which is about 20 times that of the aluminum matrix. Its existence will cause obvious tool wear and chipping.
– The harm is not limited to the wear of the tool; if it is not cleaned regularly, it will also reduce the holding furnace capacity and reduce the thermal efficiency of the holding furnace.
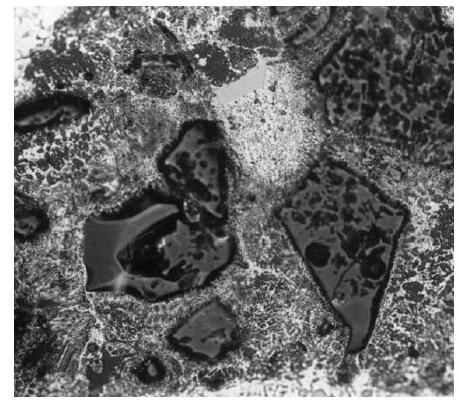
Responses
– Use the rotary rotor jet treatment method to refine the molten aluminum.
– If possible, take the material from the middle of the furnace and enter the holding furnace.
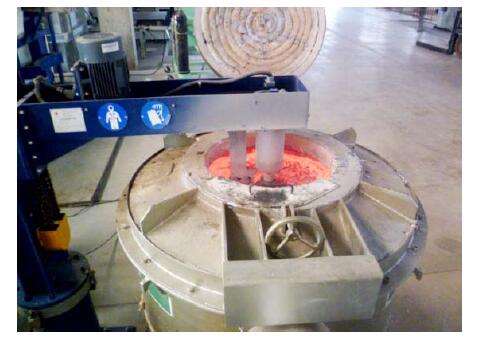
– And regularly remove a small number of nodules on the inner wall of the crucible, and remove it in its small state.
– Use refractory materials with high alumina and barium content, and reduce silica content and porosity of furnace lining materials. But the disadvantage of this material is that it is expensive.
6. Primary silicon phase
Existing in aluminum-silicon alloys, when the silicon content in the alloy exceeds 12.5%, Si precipitates in the form of primary crystals.
Therefore, when the silicon content exceeds the standard, or the alloy composition is uneven, the local content is high, and primary silicon will be formed.
The microhardness test of the primary silicon phase found that its average microhardness was HV1050, which was 15 times that of the aluminum matrix.
Obviously, this would also cause significant damage to the tool.
Countermeasures
– Do not use raw materials with high primary silicon content (the content cannot exceed 12.5%).
– Do not keep warm for a long time; the temperature is slightly higher (it is best not to keep it in a semi-solid state for a long time).
– Stir evenly to prevent the local high silicon content of the aluminum alloy from causing segregation.
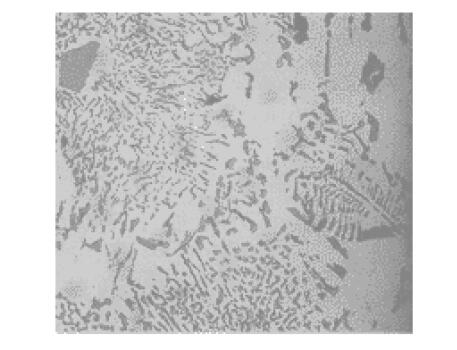
7. Secondary oxidation slag inclusion
The molten aluminum produces oxides during the casting and filling process and finally remains in the die casting. Secondary oxidation is exacerbated if there are too many runners and cavity corners and a short flow impacts the cavity.
Responses
– Change gate size and feeding angle:
Figure A forms a right angle, which will involve too much gas in the die casting.
Figure B is reasonable.
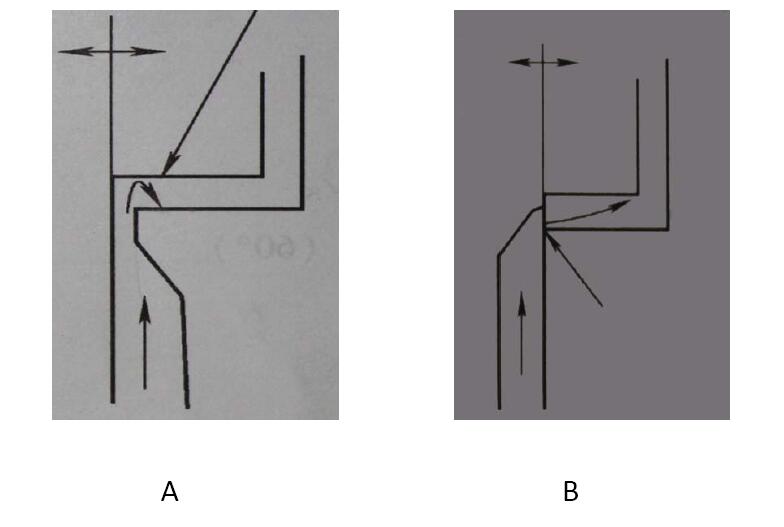
– Correction of the cross-sectional area of the runner:
The cross-sectional area of the runner should be continuously reduced so that the molten metal flow is not dispersed.
– Set a reasonable low speed to prevent too much gas from entering the molten aluminum.
8. Summary
- The charge should be free of oil and dust and should be stored in a dry place to prevent the charge from being exposed to rain and dampness and resulting in a thicker corrosion layer on the surface;
- Small pieces of debris have a large surface area and bring in a lot of oxidized inclusions, so they should not be used as a direct addition to the charge;
- Limit the Fe content in the raw materials, and the Si content should not be close to or exceed the eutectic composition.
- Reasonable selection of crucible and lining materials to prevent Fe on the crucible from infiltrating into the molten aluminum and the reaction between the molten aluminum and the refractory lining to produce a large amount of slag;
- Attention should be paid to controlling the melting temperature of molten aluminum, a slightly higher melting temperature should be maintained during the melting stage, and cold ingots should be avoided after melting;
- Use high-efficiency refining methods such as rotating rotor method (GBF) to blow nitrogen (or argon) to refine aluminum liquid;
- The molten aluminum should not be parked for too long, the molten aluminum at the bottom of the crucible should not be poured into parts, and the residues on the furnace wall and furnace bottom should be cleaned on time;
- When transferring molten aluminum, attention should be paid to the smooth flow of the liquid to prevent splashing, and the number of transfers should be minimized. Once the inclusions in the molten aluminum are formed, it is difficult to remove them by chemical methods, so the main thing is to take preventive measures.
9 Case
9.1. Sampling: collect alloys from defective parts
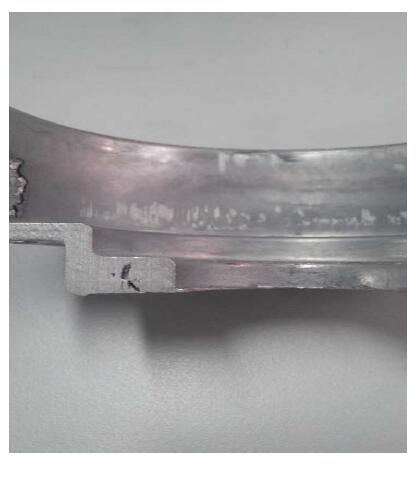
9.2 Detection:
– HF (hydrogen fluoride) treatment of the sampled material first
– Metallographic analysis (optical microscope) – Compositional analysis (electron probe, also called X-ray spectrometer)
– Microhardness Analysis (Microhardness Machine)
9.3 Analysis:
- Composition: It has been determined that the main component is an aluminum-silicon-iron-manganese phase intermetallic compound (metal sludge).
- Microhardness: Its microhardness is around HV500-700.
9.4 Actions taken:
- Control the return charge to less than 30% and the original return charge at 40-50%.
- Increase the melting and holding temperature by 10 degrees.
- Regularly clean the furnace bottom and furnace wall.
- Clean and dry the return material.
- Preheat the surrounding tools that are in contact with the molten aluminum.