Aluminum Alloy Refinement
Gases indeed occur during the die casting process. However, some dynamics and things come to play when talking about die-casting gases. For this reason, it’s ideal that we analyze this subject matter for an optimum die casting experience.
It promises to be an interesting topic, so let’s get right into it.
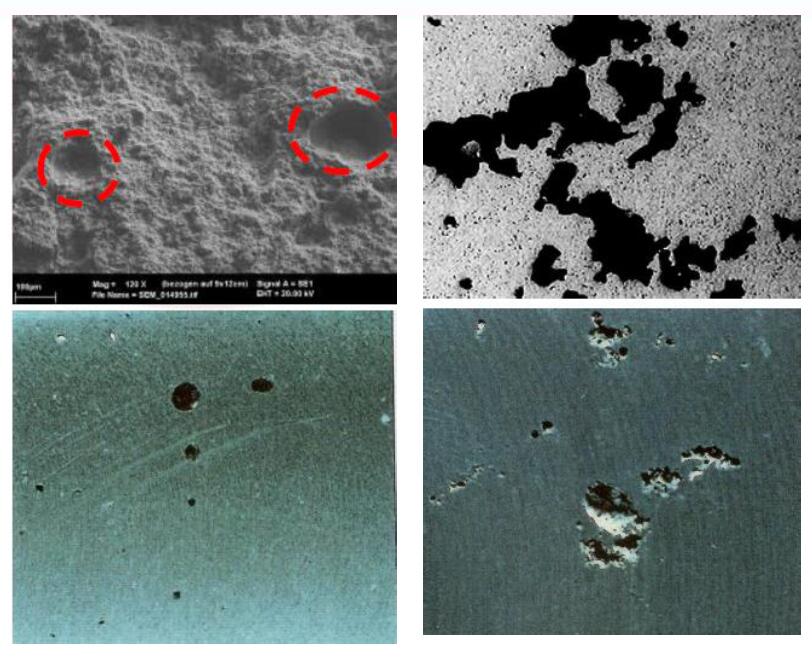
1.Where does the gas in the die-casting process come from?
In the die-casting process, we all try to avoid gas generation. Too much gas will leave many pores in the die-casting, resulting in casting defects and even scrapping.
Then, how does the gas in the die-casting process occur? There are four main aspects:
- The material itself: In the process of making aluminum ingots at the end of smelting, the material itself will contain certain gas impurities.
- Melting process: During the melting of aluminum ingots, gas will enter.
- Die-casting process: If the die-casting parameter setting is unreasonable or the release agent spraying is unreasonable, the gas will be drawn into the aluminum alloy liquid.
- Mold: Due to the unreasonable design of the mold’s runner, overflow groove, and exhaust design, gas will be involved.
For these gas problems, we need to control and improve as much as possible to ensure that the product quality meets the requirements.
2.Two product defects
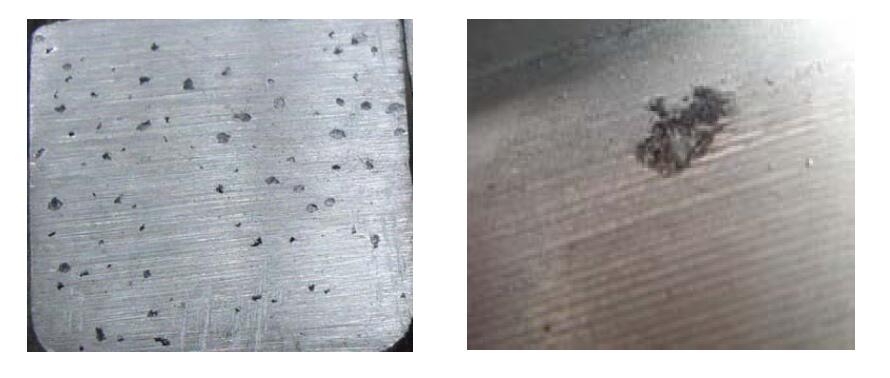
- Pinholes: Sometimes, when we cut the product for analysis, we will find dense pinholes inside. This phenomenon is because there are a large number of hydrogen atoms in the aluminum alloy liquid. When the casting is solidified, the hydrogen atoms are converted into molecular hydrogen, forming pinholes.
- Impurity points: The product contains high-hardness impurity points (Inclusions), which will severely wear the tool or even break the tool during subsequent machining. Such impurities are usually oxides.
The reasons for these two phenomena:

Aluminum reacts with water vapor at high temperatures to produce aluminum oxide and atomic hydrogen.
Water vapor comes from air or oil pollution. The aluminum liquid absorbs more water vapor if the air humidity is higher. The generated hydrogen atoms are dissolved in the molten aluminum, and more than 85% of the gas in the molten aluminum is hydrogen. The molten aluminum temperature is usually higher than 670°, so it is not hydrogen but hydrogen atoms that dissolve in molten aluminum.
Hydrogen evolution phenomenon: When the aluminum alloy liquid solidifies from a liquid state to a solid-state, the solubility of hydrogen changes. From 0.68ml/100g in liquid state (volume of 2% aluminum liquid) to 0.036ml/100g in solid-state. Therefore, as the temperature drops, hydrogen atoms precipitate and gather together to form molecular hydrogen. This creates pinholes in the product.
Atomic hydrogen → molecular hydrogen → hydrogen → pinhole
How to improve the situation?
- Shorten the solidification time of the casting, and make the casting solidify before the hydrogen does not accumulate.
- Use refining methods to remove atomic hydrogen. Currently, the second method is mainly used.
The generated alumina has extremely high stability and becomes an impurity in the alloy liquid. Therefore, we need to refine the aluminum alloy liquid to remove the hydrogen atoms and filter out the impurities for these two kinds of defects.
3.Purpose and method of refining
Purpose: Degassing + slag removal, removing oxidized inclusions in molten aluminum while also taking away hydrogen atoms.
Method:
- Adsorption purification: filtration method, solvent method, bubble floatation method
- Non-adsorption purification: vacuum treatment method, ultrasonic treatment method, electro-solvent method (non-adsorption purification equipment is complicated, high cost, and not widely used)
Filtering method
Relying on the mechanical hindrance or adsorption of the filter medium to filter the inclusions, and at the same time intercept the hydrogen adsorbed on the inclusions to achieve the purpose of refining, this is one of the effective methods to eliminate the inclusions.
The filtering method effectively removes inclusions, but the degassing effect is poor, and the filter plate is often clogged.
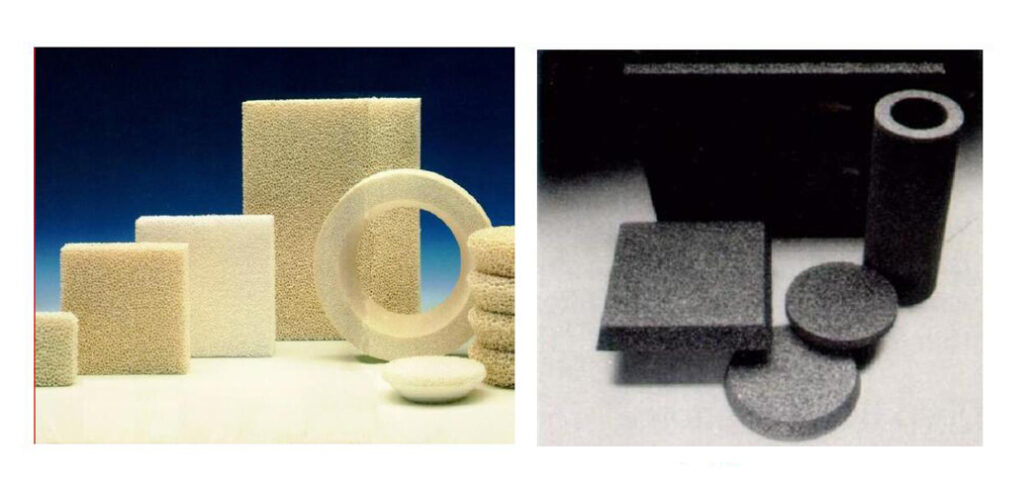
Standard filter plates are ceramic material, graphite material, and so on.
Solvent method
The solvent is generally composed of alkali metal or alkaline earth metal halide mixture. After being added to the molten aluminum, it can adsorb and dissolve the molten aluminum’s oxidized inclusions and hydrogen atoms. The generated material floats to the liquid level and enters the molten slag to remove impurities and exhaust gas.
The disadvantage is that the ability to remove suspended fine inclusions is poor.
Solvents generally include: NaCl, NaF, KCl, Na3AlF6, etc.
Bubble floatation
Gas (usually produced by nitrogen, argon, chlorine, or salts) is introduced into the molten aluminum to generate many bubbles to take away the hydrogen atoms in the molten aluminum.
The principle of the floating method is shown in the figure:
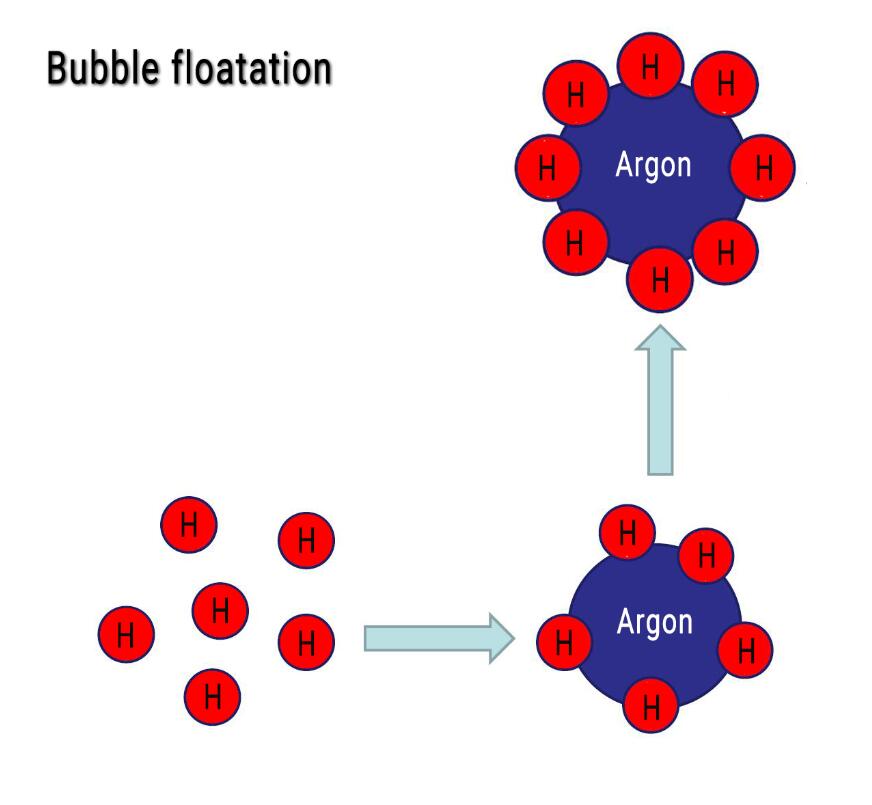
Form bubbles → float up → break through the oxide film → escape the melt
- Formation of bubbles: Pour a gas insoluble in the molten aluminum into the molten aluminum. The partial pressure of the bubble is much smaller than that of the molten aluminum. The hydrogen atoms enter the bubble through diffusion and float with the bubble.
- Floating: The molten aluminum moves directionally from the bottom of the molten pool to the liquid surface to form convection. During the ascent process, the bubbles continue to grow larger, increasing the diffusion rate of hydrogen.
- Escape: There is a thick oxide film on the surface of the molten aluminum, which has relatively high strength. The speed at which the bubbles escape depends on the structure of this layer of the oxide film. Adding a slag breaker that can break and dissolve the surface oxide film can eliminate the barrier of bubbles from escaping and increase the dehydrogenation rate of the molten aluminum.
There are two ways to increase the degassing speed:
- Increase the number of bubbles as much as possible, reduce the diameter of the bubbles as much as possible, and increase the effective contact area between the molten aluminum and the bubbles.
- Increase convection
Selection of refining agent for floatation method: nitrogen method, chlorine method, chloride salt method, argon method
Nitrogen method:
Nitrogen is the earliest method used because of the low price of nitrogen. However, nitrogen also has some disadvantages. So let’s see a few of the drawbacks.
- In order to avoid the generation of nitride impurities (AlN, Mg3N2), the refining temperature is required to be too low 710°~720°, which limits the ability of hydrogen atoms to diffuse into bubbles
- Nitrogen bubbles can only inhale hydrogen about 0.1 times their volume, and the refining effect is not obvious
- The quality of nitrogen is stringent, and traces of oxygen and moisture will significantly reduce the refining effect. For example, only containing 0.5% oxygen can reduce the degassing effect by 40%.
Chlorine method:
The refining effect of chlorine gas is perfect, but because chlorine gas is a highly toxic gas, it has not been used at present.
Chlorine salt method:
Because these chloride salts have serious pollution problems, their applications are greatly restricted.
Argon method:
When argon is ventilated, the refining temperature can reach 760°, significantly enhancing the diffusion ability of hydrogen atoms into bubbles.
The density of argon is higher than that of oxygen. Therefore, it can be enriched on the surface of molten aluminum, reducing the reaction between molten aluminum and air, so the refining effect is better.
How to use argon method:
With argon or nitrogen as the carrier, the powdered refining agent and argon are mixed and sprayed into the aluminum liquid through the nozzle. This not only has high hydrogen removal efficiency but can also remove the inclusions.
Common methods include bell-jar type, single-pipe air blowing, and rotating rotor air-jet method. However, Bell-shaped and single-tube blowing are basically not currently used due to their low efficiency.
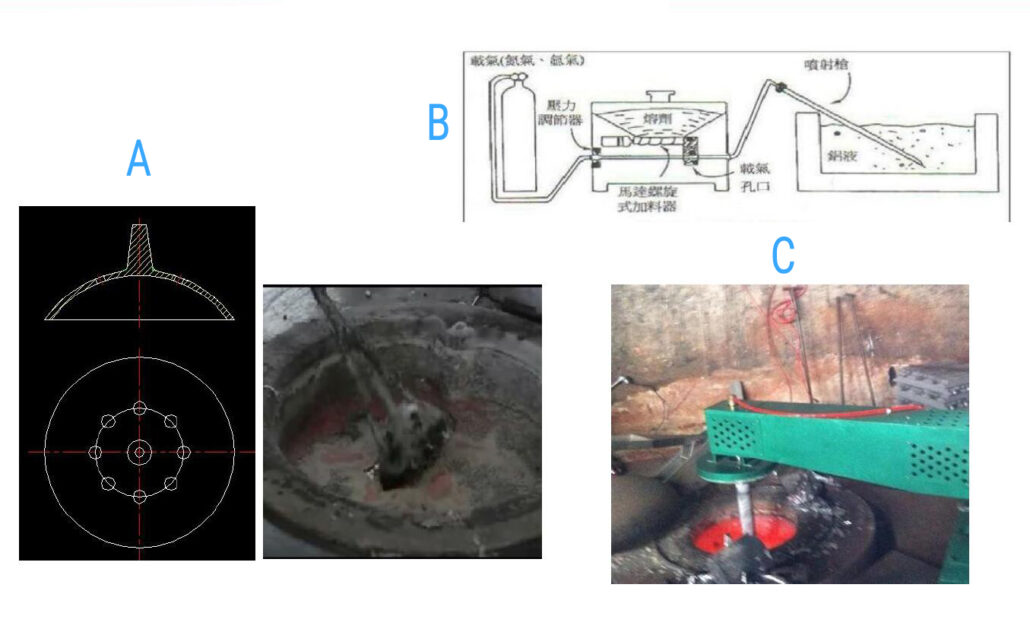
Rotating rotor jet method:
Let’s see a few characteristics of the rotating rotor jet method.
- It can fully break the bubbles and make the diameter of the bubbles very small
- The bubble rotates and rises under the combined action of buoyancy and centrifugal force (both increasing the time distance of buoyancy and the chance of small bubbles polymerizing is very small).
- The rotor rotates horizontally and radially, which basically does not damage the oxide film on the surface of the crucible too much.
- The size of the bubble can be adjusted. When the diameter of the floating bubble reaches D2mm~D3mm, it can directly break through the surface tension of the alloy liquid and escape the oxide film.
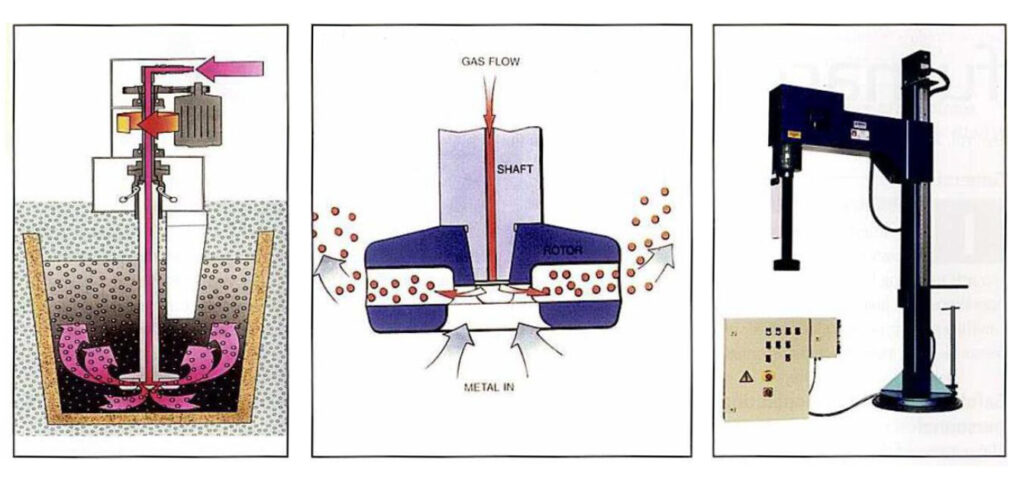
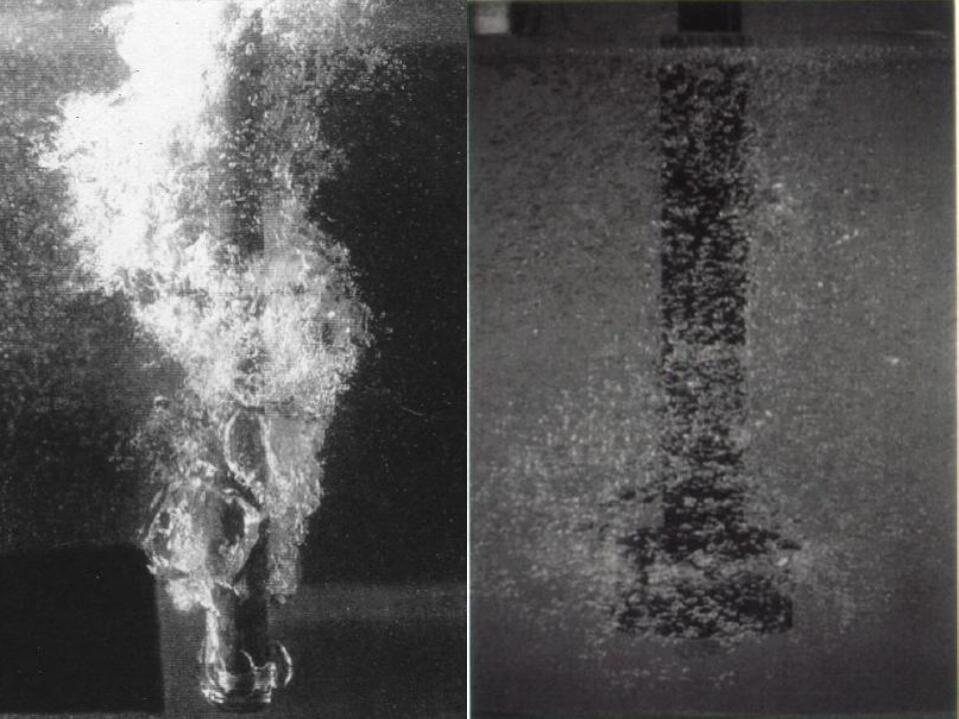
The main steps of using the rotating rotor jet method:
- Purity of inert gas: select high-purity argon for argon; select special pure nitrogen for nitrogen, not industrial nitrogen;
- Protective paint: The rotor nozzle and spray rod need to be painted to extend the life
- Temperature: Adjust the temperature of the aluminum alloy liquid to 740°~760°
- Nozzle extension depth: Try to extend the nozzle to the bottom of the crucible to 50mm-100mm, which can increase the jet flow rate and improve the time for the gas to contact the melt and the purification efficiency.
- Nozzle speed: speed up, the bubble diameter decreases, but it will aggravate the liquid surface tossing and sinking; it can be set to 450~600r/min
- Positive and negative rotation: effectively prevent the liquid surface from sinking and causing inhalation, and the one-way rotation time can be controlled within 10s.
- Blowing pressure: based on the standard that the melt does not pour into the spray rod, generally 0.2~0.3Mpa
- Gas flow rate: The flow rate is related to the nozzle speed, the depth of penetration, and the gas pressure, generally 0.25~0.4m3/h. At the same time, pay attention to the flow monitoring and degassing effect. (Observe bubble size and bubbling range)
- Blowing time: about 5~8min
- Stand still: It takes approximately 3 to 5 minutes for bubbles to float up, so you need to stand for 5 to 10 minutes to let the remaining bubbles escape.
Analysis of main components of injection equipment:
- Nozzle structure: The blade adopts a straight radial nozzle, and the bubble is fine.
- It is better to use graphite or ceramic material for the nozzle and spray rod; generally, cast iron or steel nozzle is not used, mainly because iron will pollute the molten aluminum. Graphite nozzles are pollution-free, cost-effective, and are currently the most widely used material. Ceramics are more expensive but have a long life.
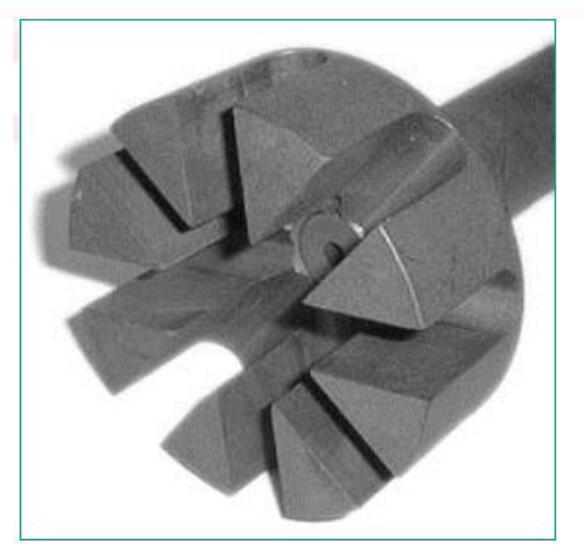
4.Orthogonal test refining effect:
First, analyze the most important factors that affect the refining effect: nozzle speed, argon flow, injection time, and standing time;
Experimental parameters:
- 45kg aluminum alloy per furnace
- Ventilation pressure 0.2-0.3Mpa
- Refining temperature 720-730°
- The nozzle is 50mm away from the bottom of the crucible
- Analysis of 100g sample from 50~70mm below molten aluminum
- Hydrogen meter as a means of inspection
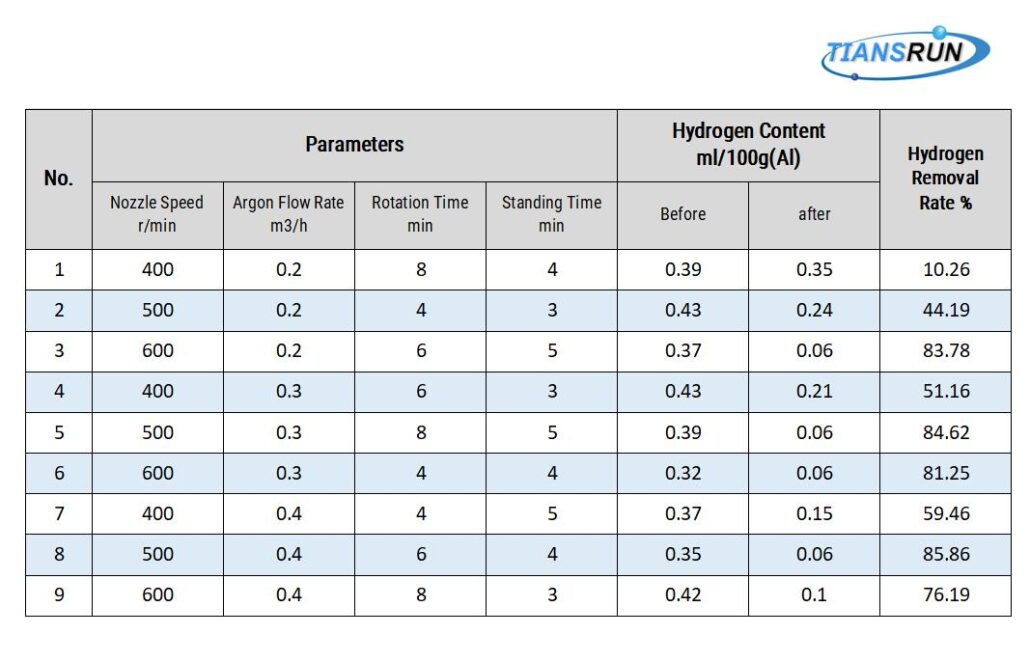
The best process is analyzed by the orthogonal method: the nozzle speed is 600, the flow is 0.4, the rotation time is 6min, the standing time is 5mins, and the hydrogen removal rate is above 85%. When the hydrogen content is 0.1ml/100g, it can meet the production requirements of general products
The data is only for reference. Actual work needs to do process test by yourself due to differences in alloy materials, molten aluminum volume, furnace equipment, degassing equipment, personnel, environment, and other factors.
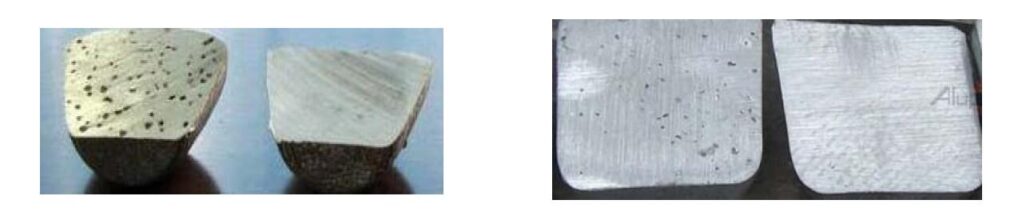
5.Why is the refinement not working?
There are times when you do not see the desired result from the refinement process. The problem could be that there is little or no attention to good practice.
So let’s see some common things to note in the refining process for effectiveness:
- Aluminum alloy solution temperature during refining: 720~750 degrees
- Whether the blowing tube is at the bottom of the aluminum alloy solution: 50~100mm
- The refining agent uses high-purity argon or ultra-pure nitrogen (non-industrial nitrogen)
- Standing time 5~10 minutes