Analysis of Die Casting Parameters By Case
1.Case Information
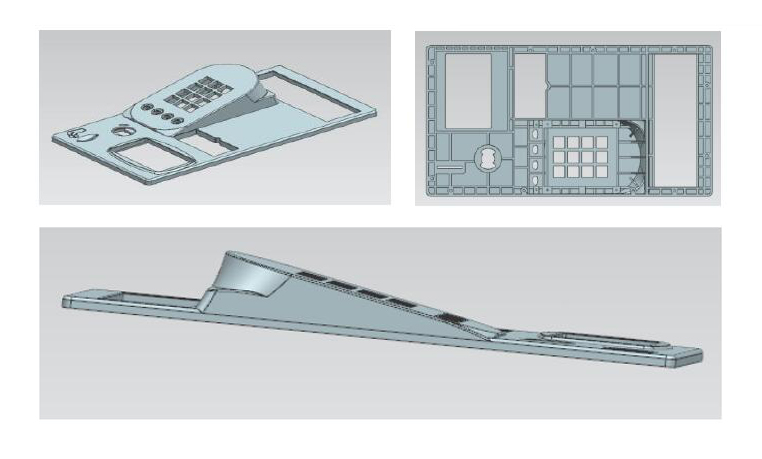
1)Product name: Telephone landline panel
2)Product information: material: ADC12, wall thickness: 2.5mm, weight: 512g, size: 332x174mm
3)Area information: the projected area of the whole mold is 600cm², the gate area is 310mm² (the gate thickness is 1mm)
4)Die casting setting: plunger diameter is 50mm, machine tonnage is 200 tons, rapid injection speed is 3m/s
We are going to check whether the process parameter setting of this product is reasonable!!
2.Die Casting Process Parameters and Product Quality
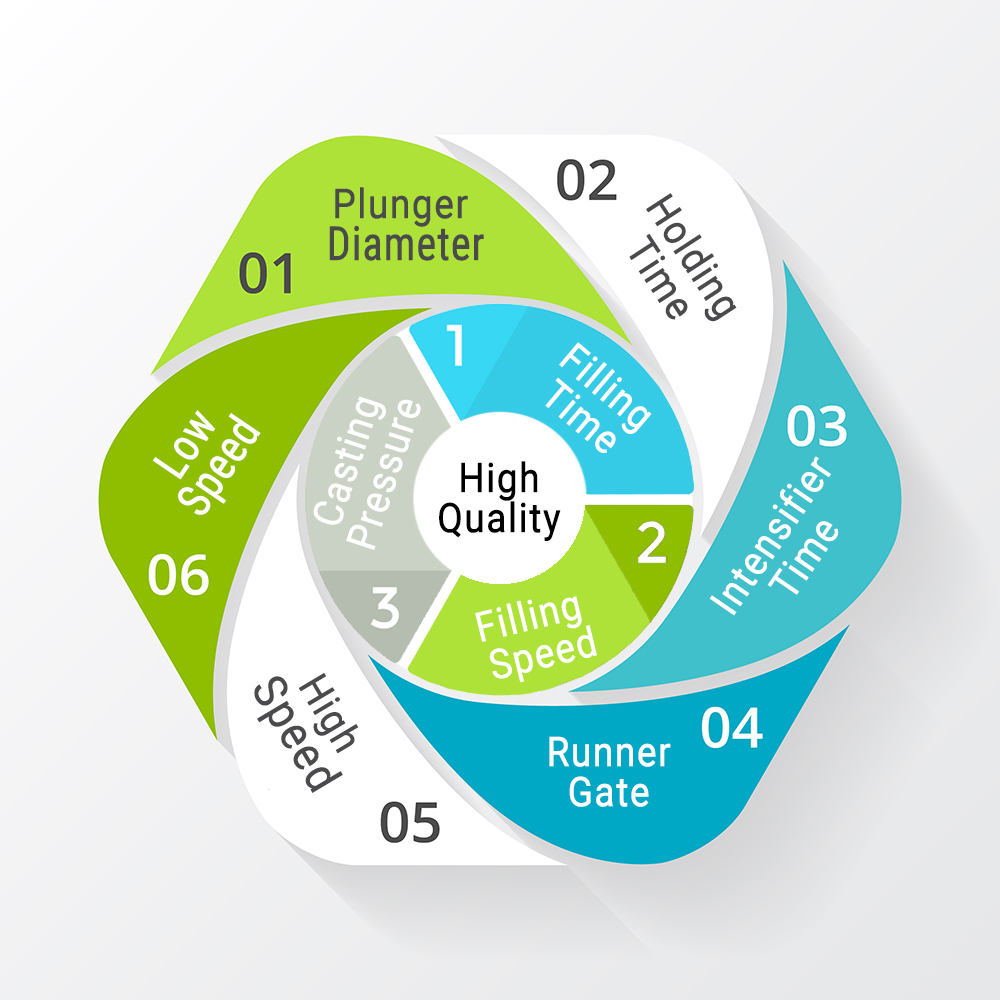
As shown in the figure, when we adjust the machine, we usually adjust the parameters of the outer circle in the figure, such as: plunger size, injection speed (low speed and fast speed), gate area, pressure build time, pressurization time, etc.
And what we want is excellent product quality. But the intermediate links, including casting pressure, filling speed, and filling time, cannot be seen from the machine.
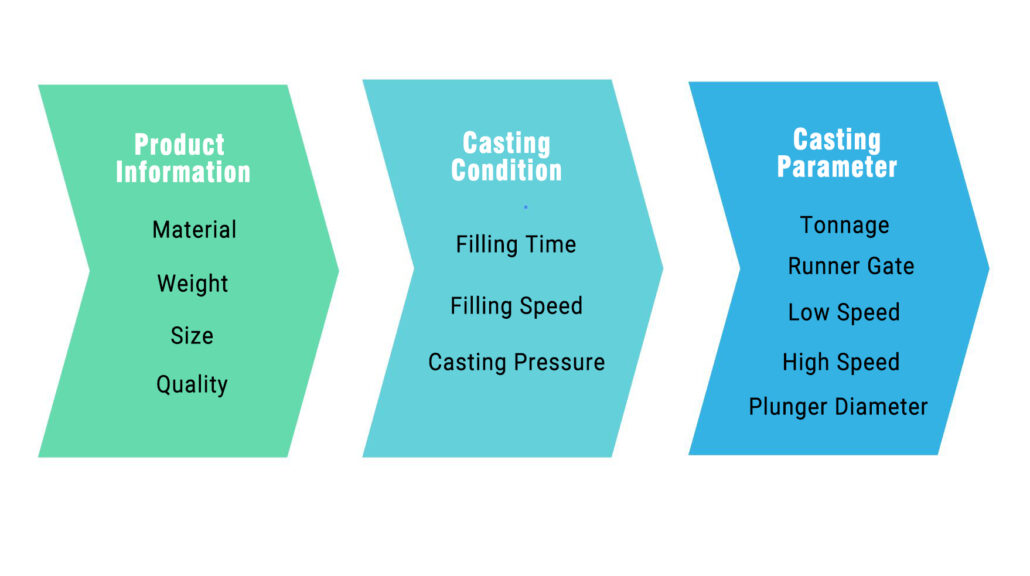
From the product information, we choose reasonable casting conditions. According to the casting conditions, we calculate the correct process parameters. Only by following this sequence can the mold and product quality be well controlled. It is not possible to skip the intermediate link directly and set the process parameters directly.
3.Casting Conditions
Casting Pressure
Casting pressure generally refers to the maximum boost pressure. In the final increase stage, the pressure is exerted by the plunger on the molten metal surface in the cavity.
- Benchmark of casting pressure: 60MPa for general parts and products with appearance requirements
- Pressure-resistant products and high-strength products are 90MPa
According to the product information above, we selected the casting pressure as 70MPa.
Fill Speed
Fill speed refers to the speed of the molten metal as it passes through the ingest. The speed of the inner gate of aluminum alloy die-casting is generally set according to the thickness of the product. Therefore, you can refer to the following table.
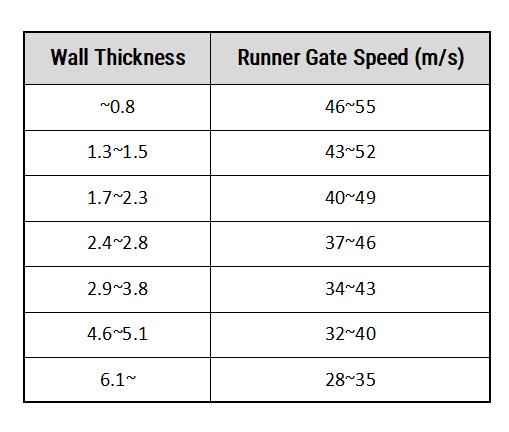
The wall thickness of the case product is 2.5mm, the weight is 512g, and the size is 174 x 332mm, so the filling speed we choose is 40m/s.
Fill time
Filling time refers to the time it takes for the molten metal to enter the mold cavity from the beginning to fill the cavity completely.
Filling time (s) = α x product wall thickness² general aluminum alloy α=0.007, magnesium alloy α=0.005
So the filling time of our case product is: 0.007x 2.5 x 2.5=0.04s
To sum up, the casting pressure=70Mpa, the filling speed=40m/s, and the filling time are 0.04s.
4.Process parameters
Selection of Machine Tonnage by Clamping Force
F (clamping force) = 1.1 x F (bulging force) = 1.1 x P casting pressure x S projected area
Casting pressure=70Mpa, projection area=600cm²
Clamping force = 1.1 x 70 x 600 x 0.01 = 462 tons, so you need to choose a die casting machine of 400~500 tons.
Choice of Plunger Size
According to the tonnage of the die casting machine, try to choose the standard plunger size. We choose a 500T die casting machine with a plunger size of 80mm.
Low-speed process
As shown in the figure below, the blue line is the speed curve of the plunger, and the red line is the pressure curve on the punch. The whole injection process is the process from A to E.
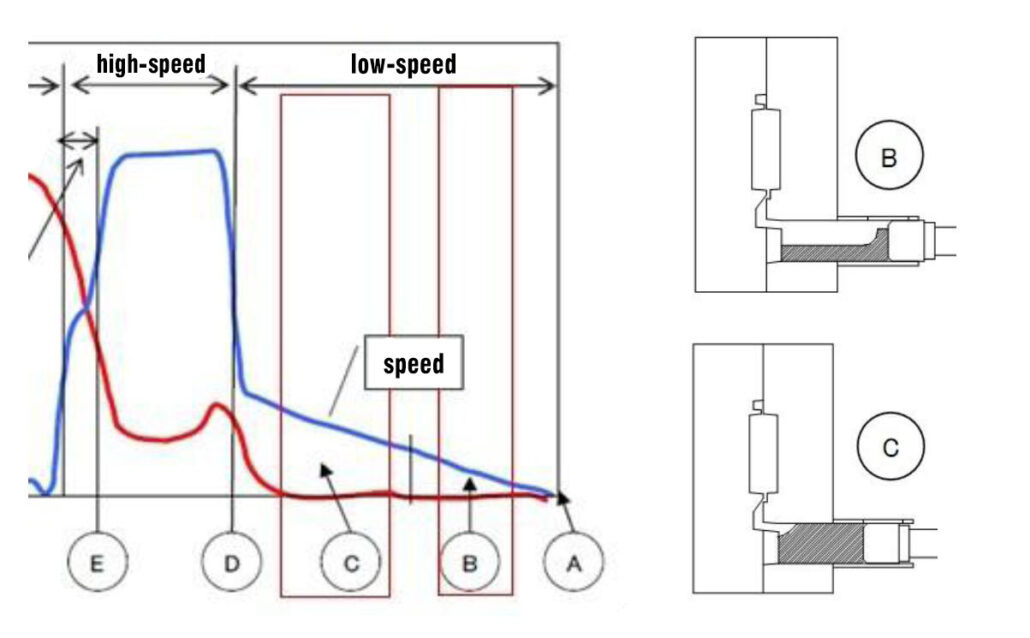
Stages A, B, and C are the low-speed movement stages of the plunger. In stage A, the plunger seals the gate of the press chamber at a speed of 0.1~0.2m/s; in stages B and C, the metal is moved at a speed of 0.2~0.7m/s. The liquid is pushed to the gate position in the mold.
Stage D is the transition stage between low speed and high speed; Stage E is where the plunger pushes the molten metal to fill the mold cavity at high speed. The filling speed is usually up to 20~60m/s.
Low-speed setting
On the left side of the picture, the speed is too low, and there will be gas trapped in the tail of the molten metal. In the middle of the picture, if the speed is too fast, the metal spray will be generated, and the spray will involve the gas into the molten metal.
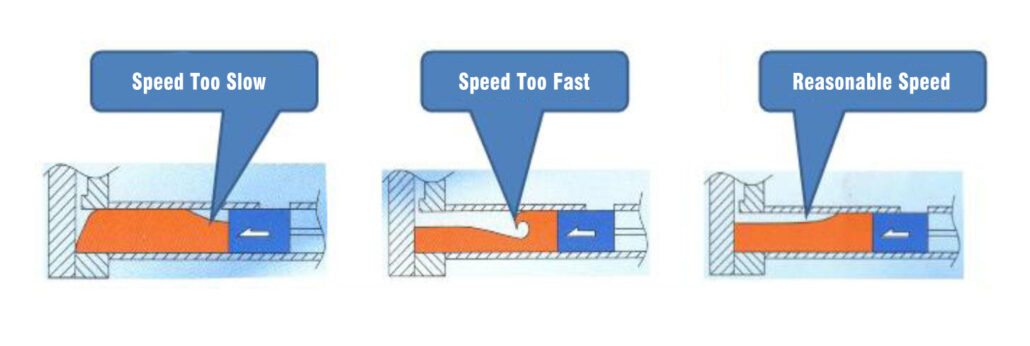
On the right side of the picture, the plunger pushes the molten metal forward at a certain acceleration without generating spray, which is a reasonable injection speed.
In the low-speed stage, is it better for the punch to move at a uniform acceleration or at a uniform speed?
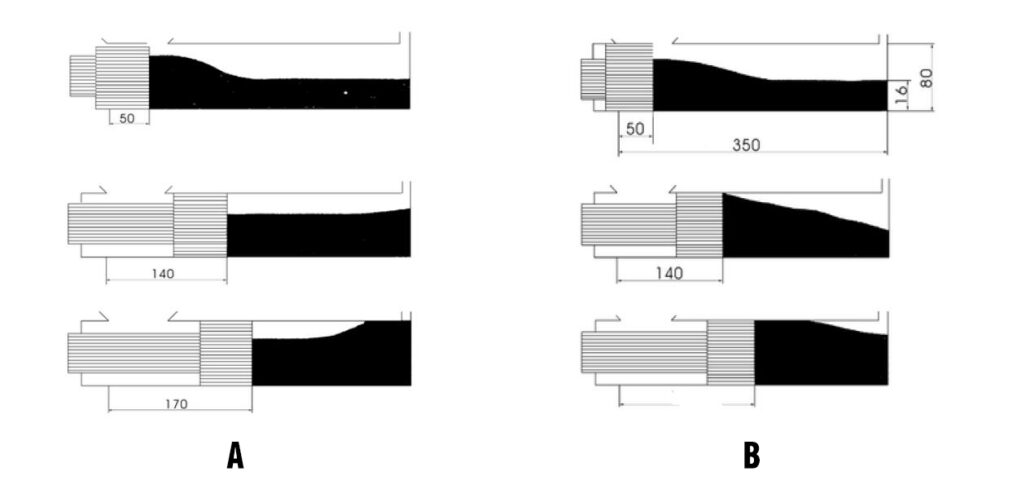
plunger A moves in the form of the alloy liquid at a uniform speed, and the plunger B moves in the form of the alloy liquid at a uniform acceleration
Conclusion: If the equipment allows, choose uniform acceleration to low critical speed. The faster the speed without ripples, the better.
In general, the low-speed range is 0.2~0.25m/s, and the calculation formula is as follows:
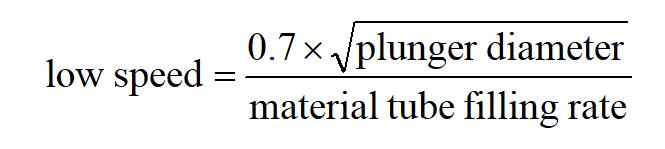
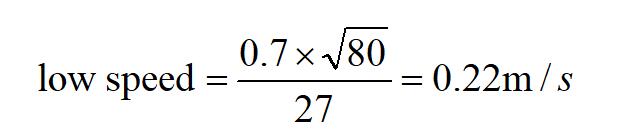
The diameter of the plunger is 80mm, and the filling material of the material tube is the filling rate of the shot sleeve.
The stability of low speed has a great impact on product quality. As with high speed, monitoring and management are required. In addition, whether the pressure chamber and the punch are stuck, etc., are also the reasons for the instability of the actual speed, so you must pay attention.
Filling rate in the calculation formula = casting weight / top cross-sectional area / plunger empty stroke / solution density x 100%
The filling rate is too low: the liquid aluminum in the shot sleeve cools too quickly
The filling rate is too high:
- The aluminum liquid is easy to splash out from the pouring port, causing personal injury and equipment damage
- The temperature of the shot sleeve is too high, causing the deformation of the shot sleeve to accelerate and the punch to be stuck.
The recommended filling rate of the shot sleeve: about 20%~50%, about 33% is the best if the large thin-walled parts can be biased to 50%.
High-speed process
In the high-speed process, the molten metal in the pressure chamber is driven into the mold cavity, and it can be concluded that:
Casting quality (above the inner gate) = the quality of the molten metal filling the cavity in the pressure chamber
Note: We generally believe that the slag bag and exhaust take up 20% of the product quality
Casting mass = plunger cross-sectional area x plunger speed x filling time x molten metal density
From this, it can be concluded that plunger speed = casting mass ÷ plunger cross-sectional area ÷ filling time ÷ alloy liquid density
Casting Mass=512 x 1.2 g Plunger Diameter=80mm Filling Time=0.04s Molten Metal Density=2.7
The calculated high speed is 1.13m/s
Conclusion: According to the parameters, the speed of the high-speed plunger can be calculated to be 1.13m/s, but considering the loss, the parameter can be set to 1.5m/s and then gradually increase and adjust according to the product test. Generally not more than 2.5m/s.
So we initially chose the high speed as 1.5m/s.
In practice, high speed can not be achieved by any amount; please refer to the mold limit speed formula:
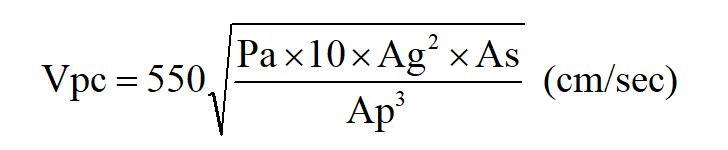
Pa: Accumulator Pressure
Ag: Runner Gate Sectional Area
As: Hydraulic Piston Area
Ap: Cross Sectional Area
Mainly limited by ACC pressure, gate size, and also limited by gate speed (gate speed needs to be less than 60)
Cross-sectional Area of Inner Gate
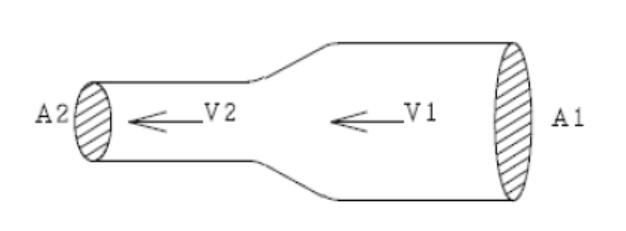
The relationship between the injection speed of the die casting machine and the gate speed can be expressed by Bernoulli’s theorem.
Flow rate Q = flow velocity V × cross-sectional area A, and the flow rates at the inlet and outlet are equal. Q=V1 x A1=V2 x A2
It is assumed that A1 is the cross-sectional area of the punch, A2 is the cross-sectional area of the inner gate, V1 is the injection speed, and V2 is the inner gate speed.
Then A2= A1x V1÷V2
Knowing punch speed=1.5m/s punch diameter=80 mm filling speed=40 m/s, calculate A2=188.4mm²
Conclusion: The gate area can be gradually enlarged from 188.4.
Verify the rationality of punch area and gate area
Experience basis:
Die casting product coordination is very important. Therefore, there is a certain internal relationship between the punch and inner gate areas. The relationship is as follows:
Cross-sectional area of punch ÷ cross-sectional area of inner gate = 20~30
Known gate area = (188) mm2 punch diameter = 80 mm, then 0.785×80²÷188=26.6.
Conclusion: The modified process parameters are relatively reasonable, and the manufacturability is better.
5.Summary
The product information mentioned at the beginning is as follows:
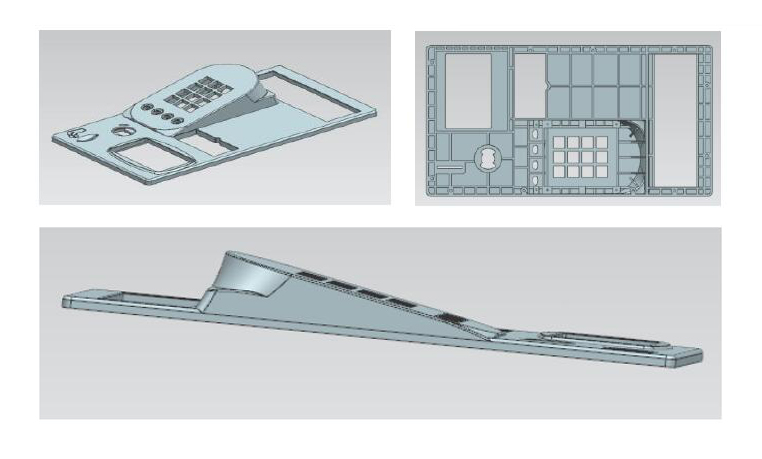
- Product information: The material is aluminum alloy, the wall thickness is 2.5mm, and the weight is 512g. Size: 174X332 mm
- Area information: the projected area of the entire mold is 600cm2, the gate area is 310mm (the gate thickness is 1mm)
- Machine setting: the barrel is 50mm, the tonnage is 200 tons, and the injection speed is 3m/s
After calculation and analysis, there are unreasonable process parameters.
Casting conditions: casting pressure=70Mpa, filling speed=40m/s, filling time 0.04s.
Process parameters of die casting machine:
- Tonnage of die casting machine: 500 tons
- Punch diameter 80mm
- High speed: 1.5m/s (can be increased gradually, no more than 2.5m/s)
- Low speed: 0.25m/s
- Ingate area: 188mm² (can be gradually increased)