What is die sticking and how to deal with it
1.The Danger of Sticking
Die sticking is one of the most common problems in die-casting, which can happen especially for aluminum alloys. It leads to:
- Repairing of Mold
- Discontinuation
- Affect automation
- Severe cases could lead to unwanted mold scratching, which spoils your mold.
The issue of “sticking” in the die-casting process has always been a difficult problem in the industry!
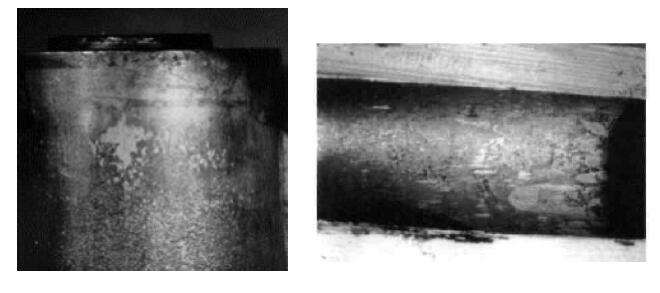
2.Die Casting Production Cycle
To deeply understand the phenomenon of die sticking, we need to study the different die casting stages, and the surface state of the die casting die.
Sticky mode theory is a comprehensive theory based on metallography, chemistry, and mechanics.
3. The effect of molten metal on the surface of the mold
3.1 Physical Shock
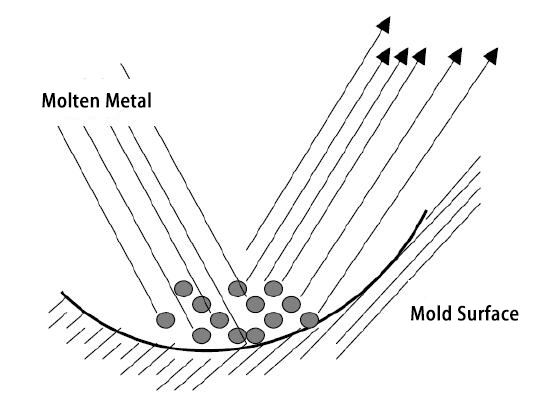
3.2 Chemical corrosion
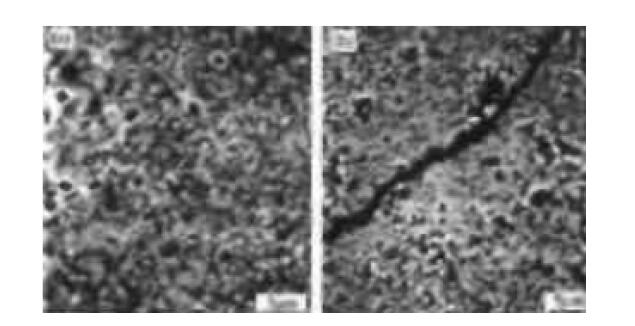
The molten metal has a physical impact and chemical corrosion on the mold surface when the temperature of the molten metal increases, the solid particles dissolve in the molten metal, which reduces the physical impact on the mold surface and reduces impact wear.
On the other hand, the increase in temperature will aggravate chemical corrosion. Therefore, the effect of the molten metal on the surface of the mold, the overall result depends on the degree of change of the two.
4. Why does the phenomenon of mucous membranes occur?
When the molten metal enters the cavity, a series of physical changes and chemical reactions will occur with the cavity wall.
1) The surface of the mold cavity changes every time it is shot, such as the color of the mold surface changes.
2) The surface of the mold is gradually covered with some small pits, 0.6 microns -> 3.6 microns -> 15 microns.
3) There are generally two changes in the pits: continue to grow larger or produce micro-cracks.
4) During injection, the molten metal enters the micro-cracks. This creates a sticky mold.
Further analysis: two phenomena occur in actual production
Erosion
The first is erosion: mainly caused by physical impact and chemical corrosion. It can also be said that erosion results from erosion and corrosion.
Sticking
After erosion occurs, die sticking follows. Both erosion and sticking have a mutually reinforcing effect. It should be said that die sticking is challenging to avoid altogether, but it can be reduced to a certain extent.
5. Sticky Mode Factor
5.1. Iron Element
Analysis of the composition of aluminum alloys is very important because the aluminum in the casting has a strong affinity with the iron in the mold. Suppose the iron content in the aluminum alloy is insufficient (in the range of 08-0.9%). In that case, it will easily adhere to the surface of the mold material and react with the iron element in the mold material. The aluminum-iron metal compound on the surface of the mold cavity plays an essential role in the sticking of the mold.
- Increase the sticking phenomenon
- Reduce sticking phenomenon
The analysis of aluminum alloys is very important because the aluminum alloy in the casting has a strong affinity with the iron in the mold. If the iron content in the aluminum alloy is insufficient (in the range of 08-0.9%), it is easy to bond in the mold of the H13 material mold.
Countermeasures: The iron content in the alloy should be strictly controlled at 0.8-0.9%.
5.2. The Surface Roughness of The Mold Is Not Up to Standard.
When the mold surface is rough, the molten metal tends to stick to it as it fills the mold.
Countermeasures: mold surface polishing. And regularly maintain the mold to keep the surface roughness of the mold up to standard.
5.3. Die Surface Hardness Is Not Up to Standard
It is required that the hardness of the mold core, inserts, sprue sleeves, and diverter cones after heat treatment is HRC46-48.
Countermeasures: modify the heat treatment process or replace the heat treatment manufacturer to make the hardness meet the standard.
5.4. Special Materials with High Melting Point Are Used at The Sticking Point
The special material with a high melting point is used in the mold sticking place, which is very effective in preventing mold sticking reducing the chance of mold sticking.
Action: Molybdenum is one of the special materials that can be welded in the mold at the sticking point.
5.5. Cast fillet
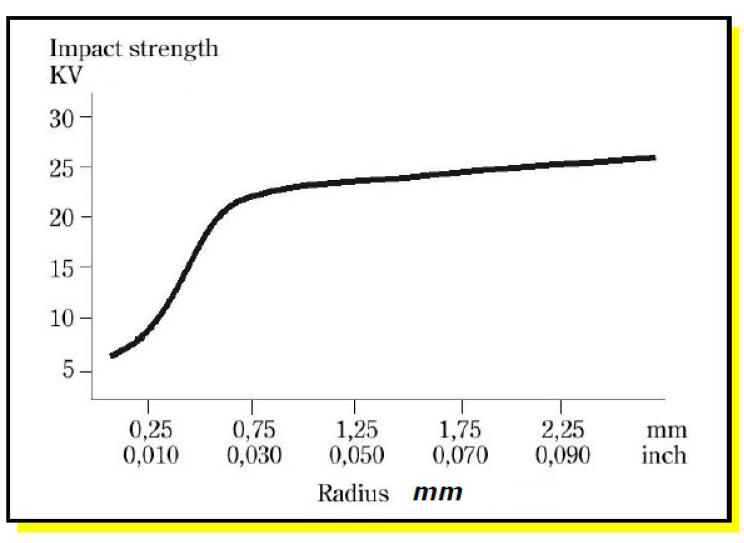
The casting fillet is too small, resulting in increased cracks and increased die sticking.
Countermeasures: Aluminum alloy fillet needs Ra>1mm
5.6. Mold temperature
The level of mold temperature is very critical for mold sticking to occur. As the molten metal is pressed into the mold under high pressure, a physical or chemical reaction occurs between the molten metal and the surface of the mold. The higher the mold temperature, the easier the mold sticking phenomenon occurs.
The mold temperature is too high, and the core is generally bonded to the mold as a whole. It is also worth mentioning that high mold temperature will cause the release agent to fail and cannot form an effective protective film (the surface cannot be wetted, and the Leidenfrost effect occurs between the release agent and the mold surface), which aggravates the stickiness. Model phenomenon.
Responses:
Because the core is surrounded by alloy liquid, it is not easy to dissipate heat, and the temperature will be high. It is necessary to strengthen its spray cooling or arrange cooling water channels inside the core.
The contact between the aluminum alloy and the mold will not stick at room temperature. However, when the temperature rises by 10℃, the reaction speed of the molten aluminum and the surface of the mold cavity increases by 2 times. At 500 °C, the reaction rate has increased hundreds of millions of times compared to room temperature.
5.7. Ingate speed
The speed of the inner gate is too fast, causing the inner gate to be flushed sharply, resulting in severe mold sticking. So, consider reducing the gate speed. In addition, too fast a speed can generate more air pockets and aggravate erosion.
Countermeasures: Check the factors that affect the speed of the ingate:
- The size and speed of the punch.
- Shot force.
- Increase the gate area.
- Reduce high speed.
- Shorten the high-speed stroke (the premise of ensuring the quality of castings), essentially reducing the flushing time.
- Other PQ2 factors.
The gate speed is essentially a temperature problem. If the speed is too fast, the alloy liquid will have severe friction with the mold cavity, thereby increasing the surface temperature of the mold cavity. Theoretically, the gate speed should not exceed 60m/s, but the gate temperature can be controlled, and the speed should be increased appropriately.
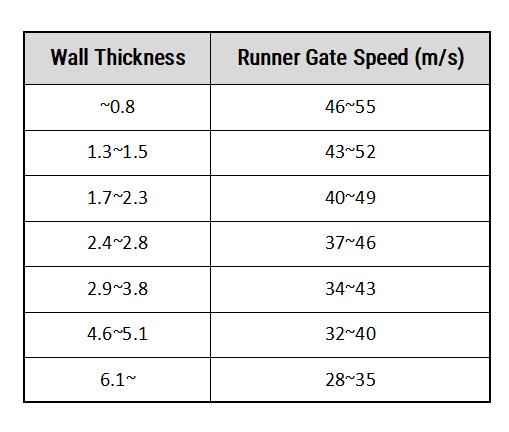
5.8. The Angle of Incidence of Molten Metal
Adjust the incident angle of the molten metal to avoid hitting the core directly; otherwise, it will aggravate the sticking.
Responses:
- The molten metal should be filled along the cavity wall as much as possible
- Change the position of the inner gate
- Try to choose a low speed to fill the product
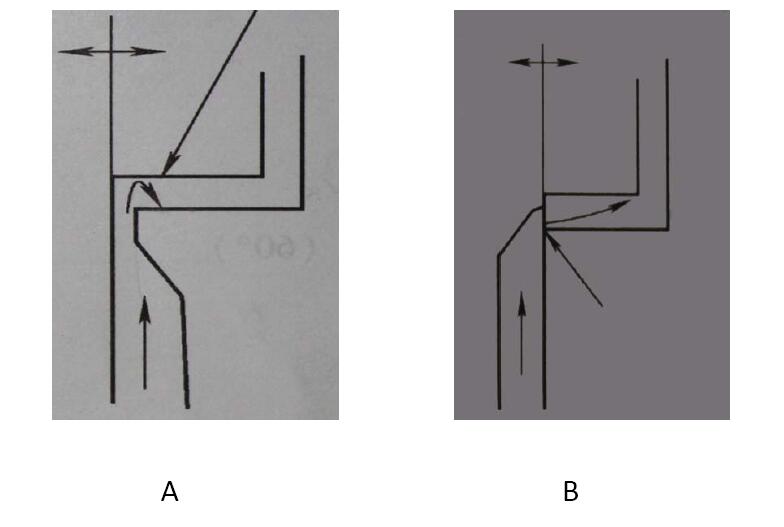
5.9. Casting pressure
If the casting pressure is too enormous, the high pressure is more likely to allow the molten metal to enter the micro-cracks, and it is more likely to cause mold sticking.
Countermeasures: On the premise of ensuring the quality of the castings, try to use a low casting pressure.
5.10. Pouring temperature
The higher the temperature of the molten metal, the more serious the chemical corrosion, and the easier it is to produce sticking.
Countermeasures: Reduce the pouring temperature of molten metal and generally control the pouring temperature of the aluminum alloy at around 660-680 degrees
5.11. Release Agent and Spray Process
Poor release agent quality and incorrect spraying processes can lead to sticking. An essential role of the release agent is to produce a protective film to prevent the molten metal from reacting with the surface of the mold. Once the protective film fails, the mold sticking will increase. In addition, when the water of the water-based mold release agent is vaporized, an oxide layer will be formed on the surface of the mold, which is also conducive to protecting the mold.
Responses:
- Check the effectiveness of the release agent
- Check the proportioning concentration of the release agent
- Change the process parameters such as spraying amount, spraying position, spraying time, and so on
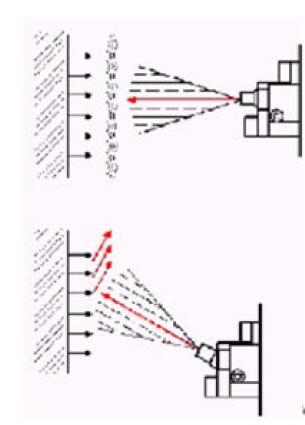
5.12. Mold Surface Treatment
The mold surface treatment process is not in place, which will also lead to mold sticking.
Responses:
- Nitriding of the mold surface (nitriding thickness is the key).
- Perform PVD processing.
- Oxidation treatment
The purpose is to form a dense protective layer on the surface of the mold to prevent the occurrence of mold sticking.
5.13. There Are Many Impurities In The Alloy Liquid
The aluminum alloy liquid is not purified and refined and contains many high-hardness impurities (such as the formation of monocrystalline silicon). High hardness impurities will wash out the mold surface.
Countermeasures: Do an excellent job of refining treatment such as slag removal and degassing
5.14. Clamping Cooling Time
If the cooling time of mold closing is too short, the mold will be opened before the casting is completely cooled. If the production cycle is too short, the mold temperature will rise, and the mold will be stuck.
Countermeasures: Reasonably formulate process parameters.
5.15. Clean the Mold Surface In Time
When there is a rough area on the mold surface where sticking occurs, this area will rapidly increase the degree of sticking. When cleaning the mold, it must be ensured that the rough parts caused by the sticking of the mold are removed and treated.
5.16. The melting point of mold material
Special treatment should be given to areas where mold sticking occurs. A common practice is to add a chemical substance with anti-stick properties to this area of the mold, one of which is a tungsten-based compound or a molybdenum-based compound.
The content of tungsten or molybdenum in these two materials is very high, increasing the melting temperature of the mold surface and effectively avoiding the interface effect of aluminum alloy.
6. How to deal with the mold after sticking?
Traditional treatment method: Use sandpaper and oil stone to polish the mold, but this treatment method is easy to damage the mold.
A better way: Cleaning with a sodium hydroxide solution, essentially like chemical polishing
2Al+2NaOH+2H2O—2NaAlO2+3H2↑ But it cannot be polished with acidic substances; otherwise, it will damage the mold.
Sodium hydroxide solution concentration: 100g/l, add 100g sodium hydroxide to one liter of water. The concentration is for reference only. The higher the concentration, the easier it is to remove. Increasing the solution temperature is also beneficial to the reaction (generally, the temperature is 55-90 °C).
Advantage: Higher efficiency than traditional
Disadvantages: This method is slightly more expensive, but it is more economical if used for waste liquid treatment and recycling.
7. Summary
7.1. The Occurrence of Sticking Is Affected by The Following Factors:
The temperature of the mold surface, the temperature of the aluminum alloy melt, the composition of the aluminum alloy material and the mold material, the surface finish of the mold, the design and direction of the inner gate, the strengthening treatment of the mold surface, etc.
7.2. At Present, The Main Reasons for Sticking Mold Include:
- Direct scouring of the cavity when the metal flow enters the mold cavity at a relatively large angle;
- the temperature of the metal stream is rather high;
- The gate speed is faster.
- Control of mold temperature.
7.3. Measures to Deal with Sticking
- The direction of the molten metal entering the mold must contact the surface of the cavity at a slight angle;
- Under the condition of ensuring the quality, try to reduce the temperature of the molten metal;
- Minimize the temperature in the mold where the mold is prone to sticking;
- Within the allowable range, increase the iron content in the aluminum alloy to 0.9%;
- The release agent sprayed on the surface of the mold should effectively reduce the occurrence of mold sticking;
- The surface treatment of the mold can reduce the sticking of the mold. These surface treatment methods include nitriding and carbonitriding treatment, physical vapor deposition dense layer (PVD), an aluminum film, etc.;
- Use other high-strength unique materials where sticking is likely to occur. These materials include molybdenum-based alloys, such as Mo-785; and tungsten-based alloys, such as Anviloy 1150.
7.4. Summary
When we try out the mold, it is not only OK to produce qualified products but to produce qualified products at a lower speed, lower temperature, and lower pressure, which reflects the company’s strength.
Although the problem of sticking is challenging to avoid, we can summarize more on-site experience to formulate an economical and reasonable process.