Mold Surface Treatment Technology
The failure of the mold often starts from the surface, and the quality of the surface performance of the mold directly affects the service and life of the mold. The performance requirements of the mold surface and core are different, and it is difficult to achieve by changing the material or the overall heat treatment of the mold. However, different surface strengthening technologies can effectively improve the mold surface’s wear resistance, corrosion resistance, adhesion resistance, and thermal fatigue resistance.
The main mold surface treatment technologies include:
1)Surface shot peening
2)Nitriding treatment
3)Oxidation treatment
4)PVD treatment
5)Laser surface strengthening treatment
6)Surface coating treatment
7)Welding treatment
1.Surface Shot Peening
Surface shot peening is a spherical medium that hits the surface of the mold at high speed to form a layer of compact and compressed tissue. Shot peening improves the strength and hardness of the mold surface and improves the mold resistance to thermal fatigue cracking.
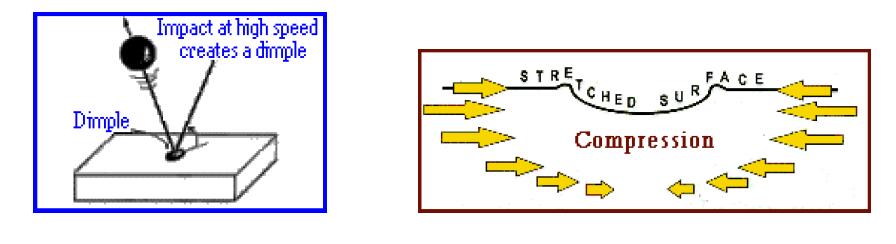
After the surface shot peening, the stress state of the mold surface changes. As a result, the original tensile stress on the die surface becomes compressive stress. As shown below:
The yellow curve is the surface compressive stress state after shot peening.
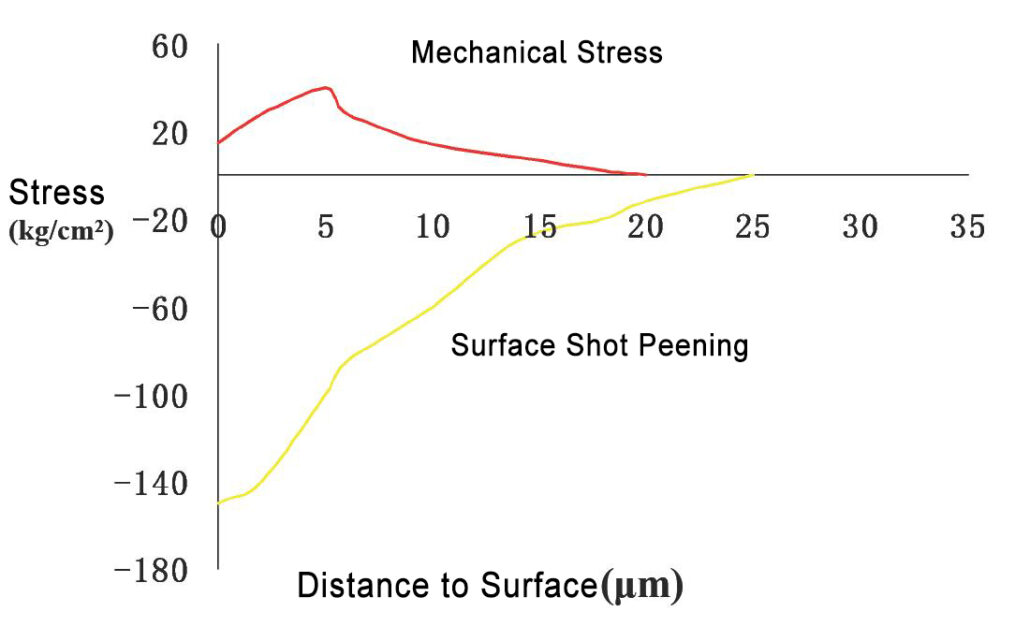
The surface microstructure is also improved after shot peening.
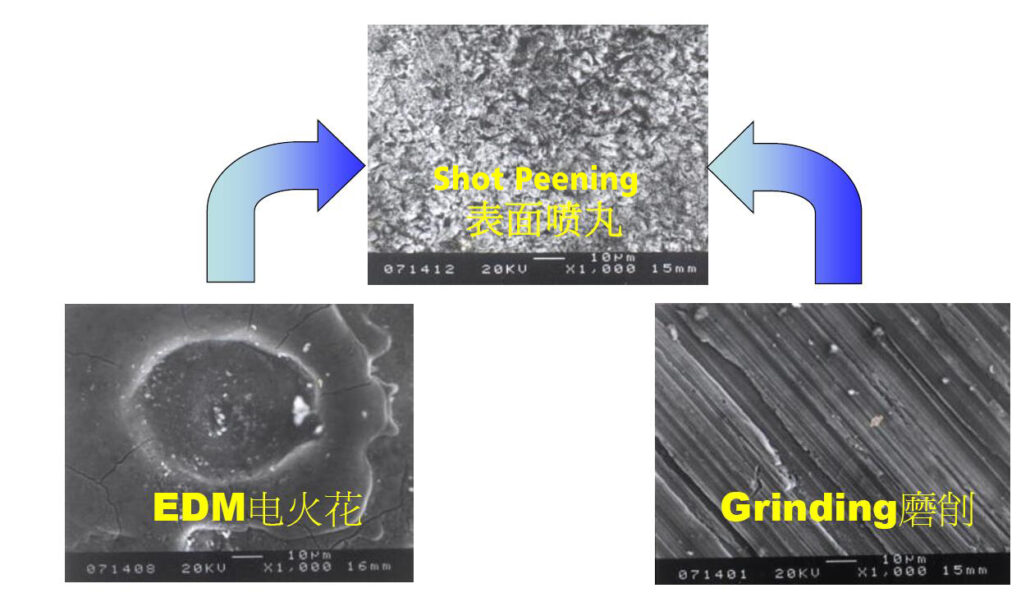
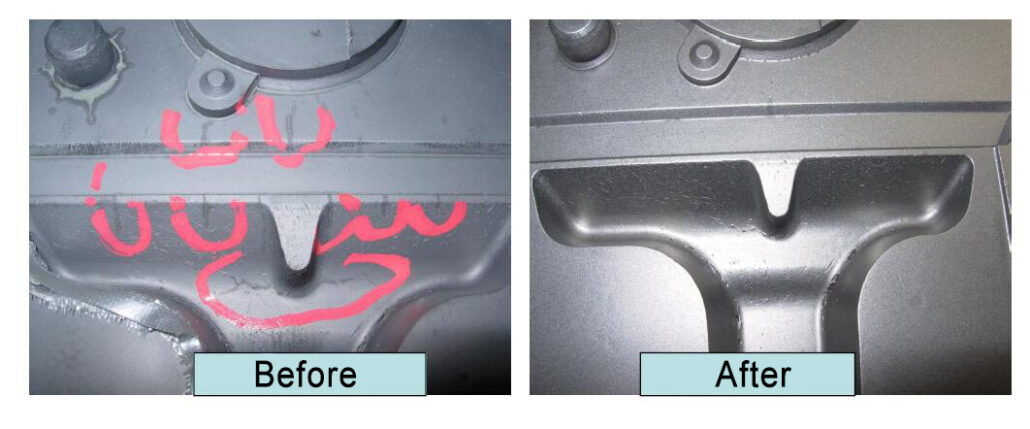
2.Nitriding
Nitriding treatment is a chemical heat treatment process in which active nitrogen atoms penetrate the workpiece’s surface at a specific temperature.
The benefits of nitriding
- High hardness and high wear resistance: After nitriding, the surface hardness of the parts can be as high as 950~1200HV, and it can still maintain fairly high hardness at 600℃. This is obviously not achieved by carburizing and quenching. Furthermore, the wear resistance is also very good due to the high hardness.
- Higher fatigue strength: The surface after nitriding produces a large residual compressive stress, which can partially offset the tensile stress generated under the fatigue load, delay the fatigue failure process, and significantly improve the fatigue strength.
- Good corrosion resistance: It can resist the corrosion of the atmosphere, weak alkaline solution, etc., and has good corrosion resistance.
- The friction coefficient is reduced: A layer of compound on the nitrided surface can store a small amount of oil and has a lubricating effect.
- 5) Anti-scratch, anti-seize, and anti-adhesive wearability are improved. After nitriding, there is a ceramic-like surface compound on the surface, which is not easy to be stuck or scratched and has good anti-seizure performance.
- Minimal heat treatment deformation. The nitriding temperature is low, generally 480~580 ℃, and the heating and cooling speed are very slow. During the treatment process, there is no structural transformation in the heart, and the quenched and tempered structure is maintained, so the deformation of the parts after nitriding is small.
- Beautiful appearance
Unacceptable nitridation is shown in the figure, with a white layer and vein-like nitrides. Its characteristic is that it is easy to cause early surface cracking.
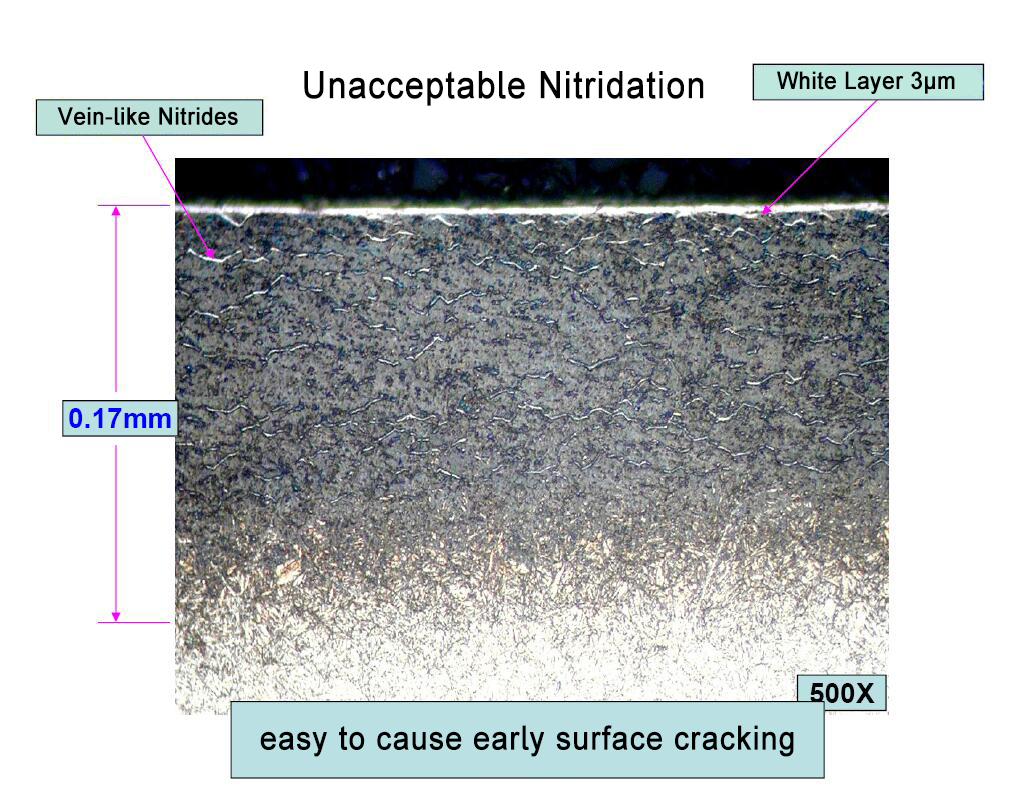
Qualified nitridation is shown in the figure, there is no bright white layer on the surface, and there is no vein-like nitride in the internal structure. This nitride has good erosion resistance and corrosion resistance.

3.Oxidation Treatment
The mold is heated by steam to produce a dense, stable, and protective Fe3O4 oxide film on the mold’s surface without changing the raw material’s mechanical properties in the shape of fish scales. This layer of oxide film isolates the direct contact between the liquid metal and the mold material, thereby effectively delaying the adhesion and burning of the liquid metal to the surface of the die-casting mold material, thereby improving the corrosion resistance of the mold.
Moreover, the scale-like oxide film enhances the adhesion of the mold surface to the lubricant, reduces the friction coefficient, and is easy to demold.
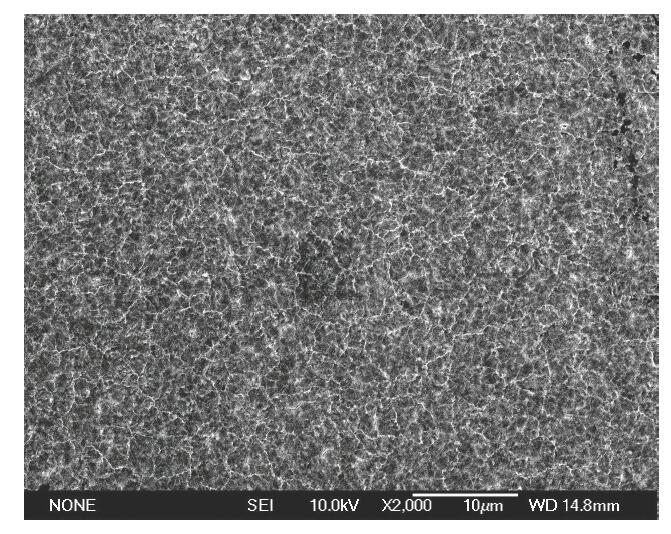
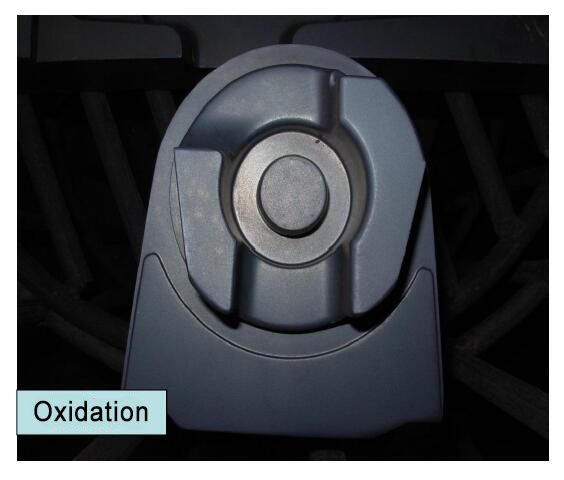
4.PVD Vapor Deposition
Physical Vapor Deposition (PVD) is a process in which a low-voltage, high-current arc discharge technique is used to convert solid plating materials into atomic, molecular, or ionic gas-phase substances under vacuum conditions. The acceleration of an electric field deposits the gas-phase substances—a method for preparing a solid thin film on the surface of a substrate.
Advantages of PVD coating:
- The bonding force between the coating and the mold base is very strong, and it is not easy to fall off.
- The coating has superior high-temperature oxidation resistance and can delay the appearance of fatigue cracks on the surface of the mold.
- The hardness of the coating is as high as HV2000-4500, and the erosion resistance is excellent.
- The production of the coating is in a vacuum environment without pollution. And automatic control of the production process.
- The thickness of the coating can be controlled by the length of the processing time. This will help achieve the desired coating thickness.
- The comprehensive cost of the coating is low, and the average production cost of a single product is reduced by extending the life of the mold.
The figure below is the hardness value after common surface treatment. The surface hardness after PVD treatment cannot be expressed by Rockwell hardness but can be measured by Vickers hardness.
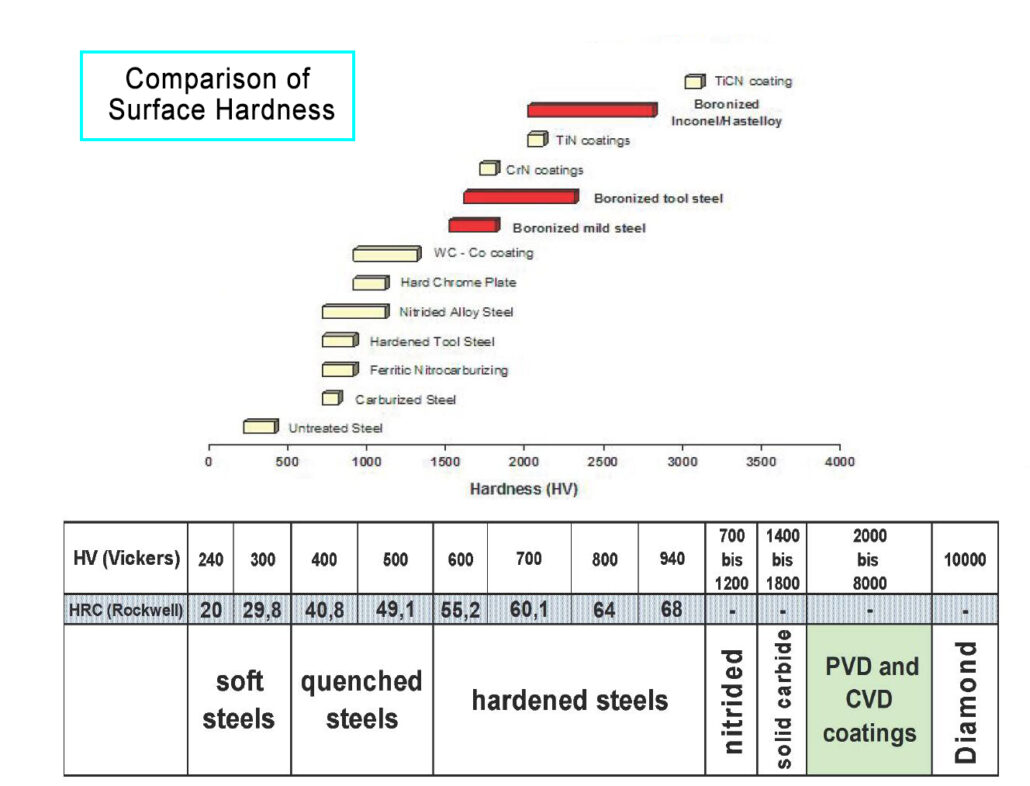
In the next blog, we will specifically explain the knowledge of PVD.
5.Laser Surface Enhancement Treatment
Laser surface quenching is the most mature technology in the field of laser surface modification. It is a high-energy laser beam irradiating the surface of the workpiece so that the surface temperature rapidly rises above the phase transition point (below the melting point). Due to the good thermal conductivity of the metal, when the laser beam is removed, the workpiece is rapidly cooled to realize the material and quench hardening.
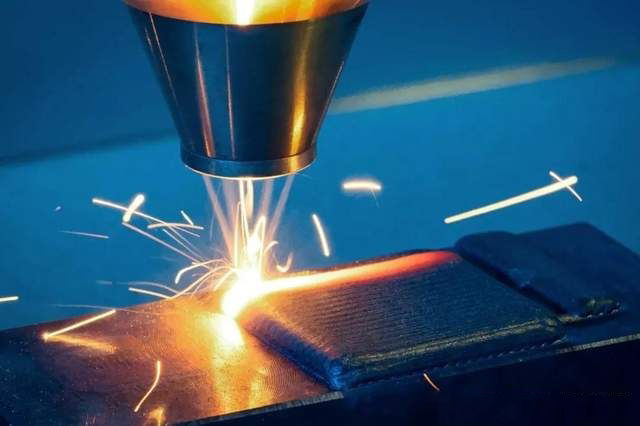
Features of laser surface treatment:
- Fast heating, fast cooling.
- High hardness and high fatigue strength. The hardness of laser surface quenching is 15%~20% higher than that of ordinary quenching. The fatigue strength is greatly improved because the surface has residual compressive stress above 4000Mpa.
- Precise local heating. Through the light guide system, the laser beam can accurately irradiate the local area of the workpiece, especially the corners, blind holes, inner walls of deep holes, and other surfaces that are difficult to be strengthened by other heat treatment processes.
- The depth of the hardened layer is 0.2-0.5mm
- The heat-affected area is small, and the influence on the performance and dimensional deformation of the substrate is small. Furthermore, the quenching deformation is small since it is not the overall heating but a small area scanning heating.
- High production efficiency and easy automation. The laser quenching process has no smoke, low noise, and low heat radiation. After automation, the working conditions are greatly improved.
6.Surface Coating Treatment
The surface coating treatment releases the high-energy electric energy stored by the power source between the metal electrode and the base metal at high frequency instantaneously and forms multiple micro-arc channels through the gas ionization between the electrode material and the base metal. Under the action of the micro electric field, the electrode material is welded to the base metal matrix to form a metallurgical bond.
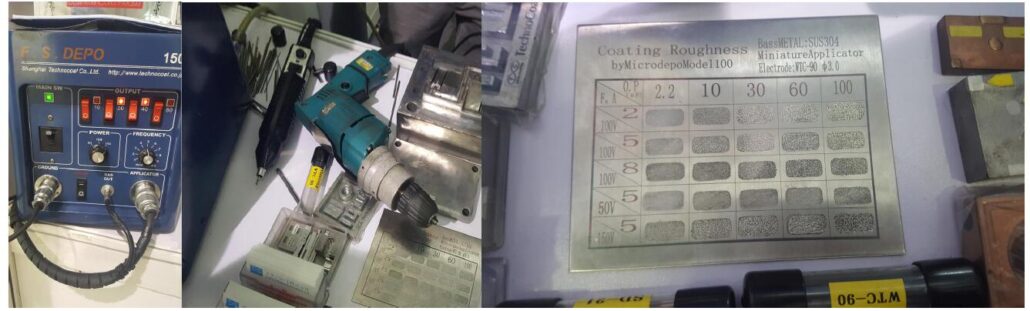
Features of surface coating treatment:
- The tungsten carbide can be quickly penetrated into the surface of the workpiece in a short time, and the efficiency is very high.
- It can increase the heat resistance and wear resistance of the coated workpiece surface and prolong the service life
- Thickness and surface roughness can be adjusted, and the standard thickness is 0.01-0.1mm
- The mold basically does not heat up and does not deform
7.Welding
Bevel preparation
Sharp-angled grooves are prone to cracking during welding. U-shaped grooves will form slag inclusions at the weld. And the third groove is a suitable shape.
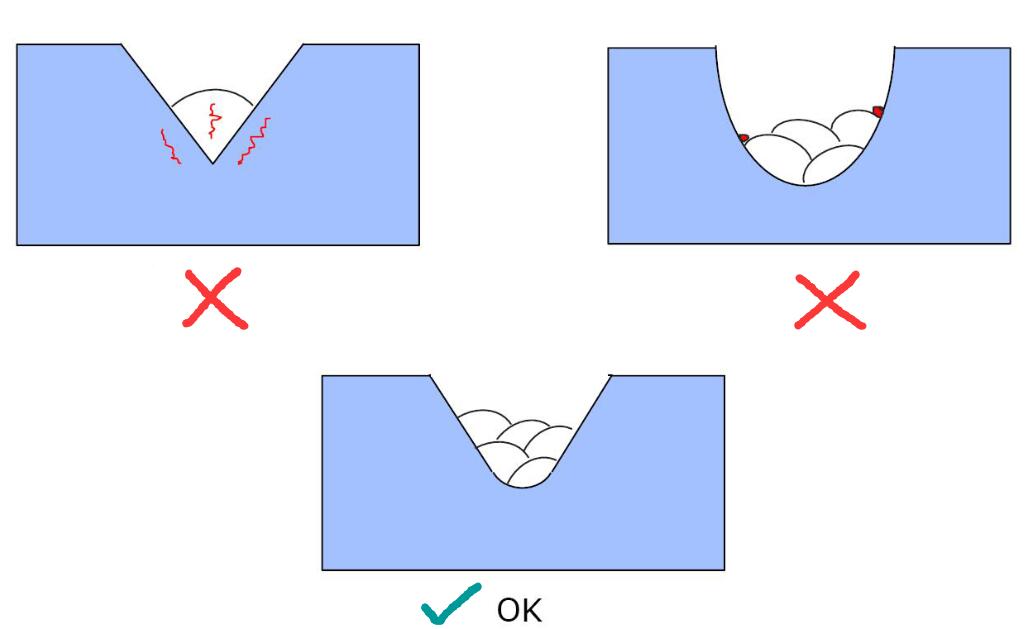
Welding notes
- The heat-affected zone should be minimized when soldering. When welding the bottom first and second layers, use small size electrodes and low current welding. Slowly spread out the solder material.
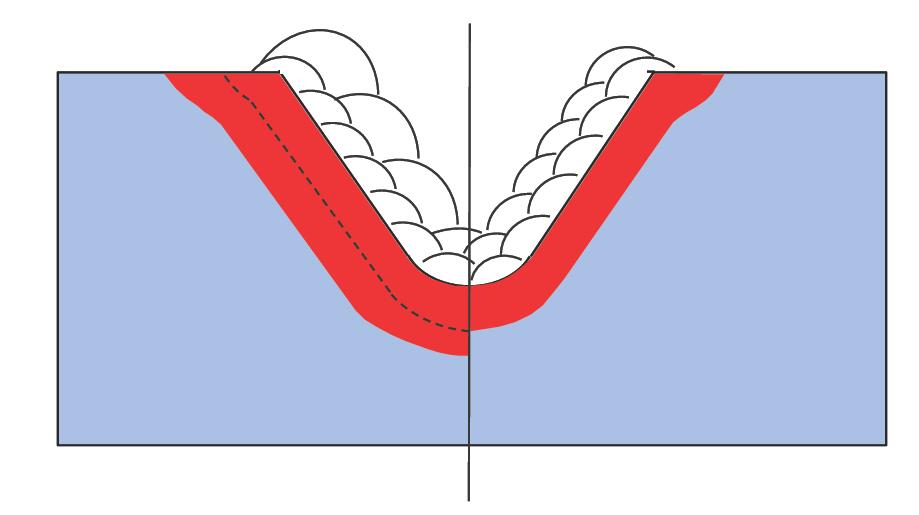
- Large and coarse weld beads will form a coarse weld structure, which is detrimental to the strength and surface quality of the weld joint.
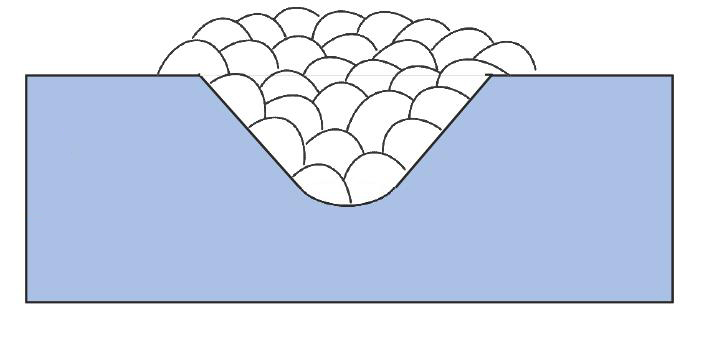
- Small and fine welding beads form a fine weld structure, which is beneficial to the strength and surface quality of the welded joint.
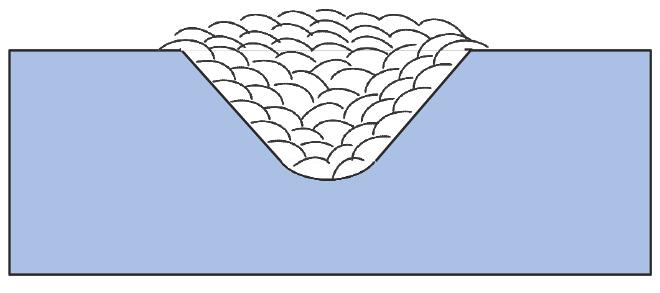
Welding steps
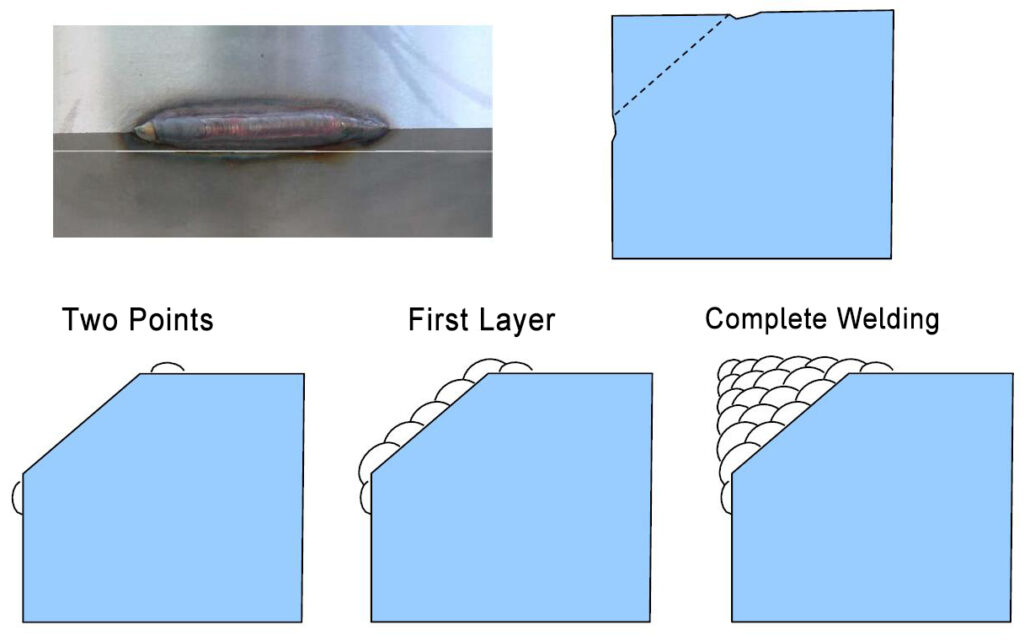
If the mold crack is large, it cannot be removed entirely by machining. A small slit can be made at the bottom of the bevel. Use softer filler material to weld in sequences 1, 2, 3, 4, 5, 6, 7. Continue to tile the upper layer with soft material.
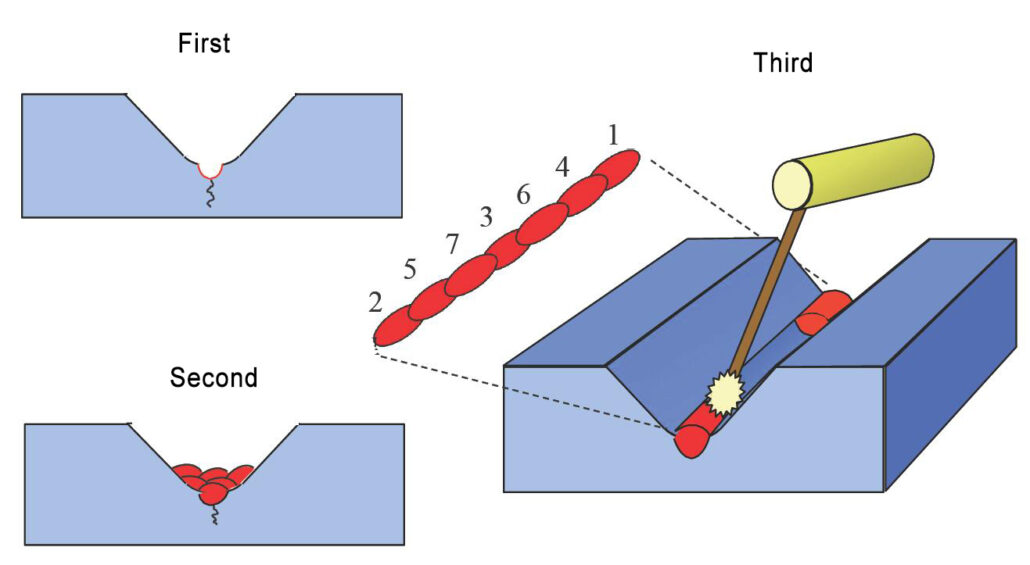
Finally, a space of 5mm is reserved for the upper layer and covered with hard welding material. Using a soft material in this way minimizes the risk of cracking.
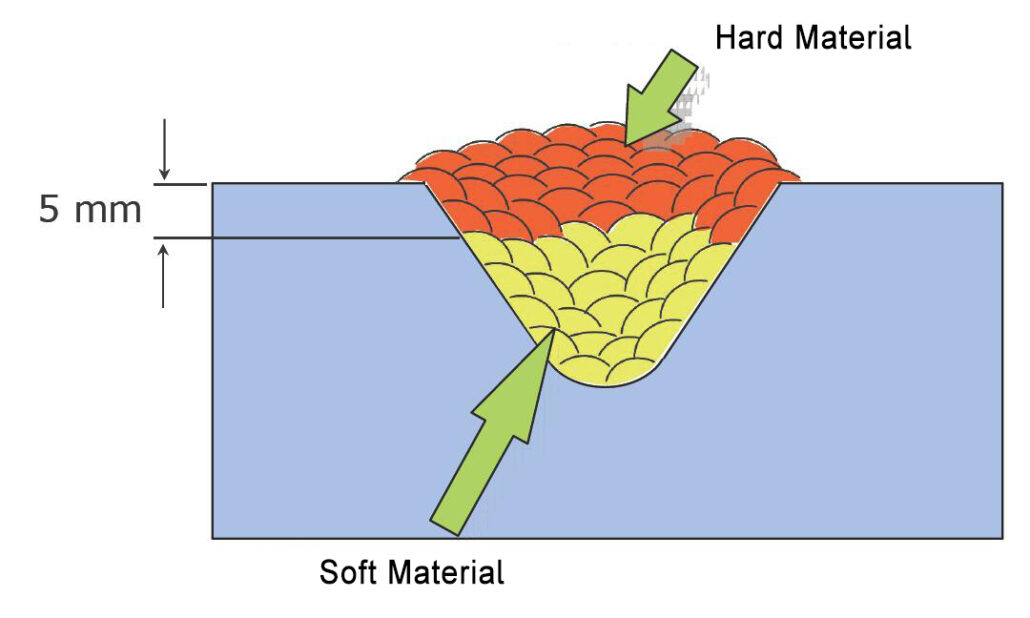
Summary
- Surface shot peening is suitable for hot cracking and sticking and can be used for simple new and old molds.
- Oxidation treatment is suitable for erosion and can be used on new molds and old molds without cracks.
- Nitriding treatment is suitable for erosion and can be used for new molds and old molds without cracks.
- PVD is suitable for erosion and aluminum sticking for the treatment of new molds.
- The coating is suitable for erosion and erosion and can be used on new and old molds
- Laser hardening treatment is suitable for erosion and sticking of aluminum and can be used for new and old molds
- Welding is suitable for hot cracks, R-angle cracks, and mold cracking and can only be used for old molds.