Peeling of Die Casting Defects
Peeling, also known as skinning, delamination, etc., is mostly caused by obvious multi-layer metal skins on the outer surface or inside of the casting, and the occurrence parts are mostly concentrated on larger planes, arc surfaces or near corners.
After shot blasting, many die castings will appear peeling on the surface. And many die castings have appearance requirements, once there is a peeling phenomenon, it will become a waste product.
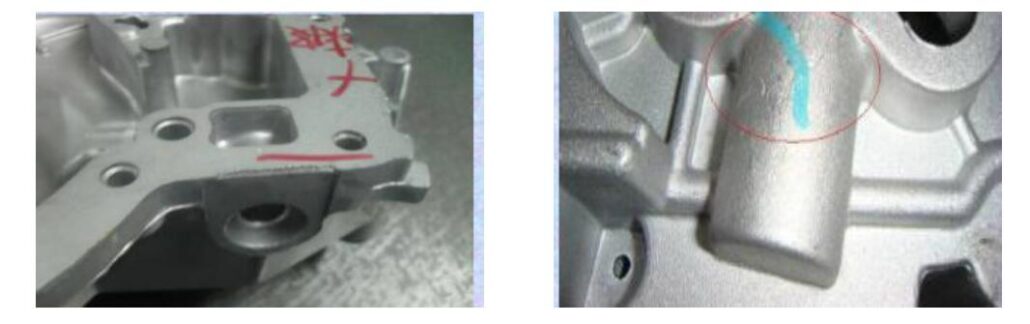
1 Peeling phenomenon
– The casting surface is separated from the casting base.
– Generally, there is no peeling after the die casting is completed, but after shot blasting, sand blasting, shot blasting, etc.
– Obvious peeling is the metal skin layer that is obviously separated from the matrix locally or there is a non-dense pockmarked metal layer on the surface of the casting;
– The insignificant peeling is formed by the accumulation of multiple thin layers. Careful observation of the casting blank shows a 2-7mm high-bright flaky surface, but no peeling defects can be seen. It will appear after shot blasting or high temperature. There are obvious peeling defects.
2 Reasons for peeling
1) When the molten metal fills the cavity, it is discontinuous or unstable.
2) The mould temperature is locally low.
3) The molten metal that enters first is solidified first and oxidised by water vapor and oil fumes.
4) The molten metal that the subsequent metal enters covers it.
The first layer of metal that causes the surface of the casting to solidify is not strong enough to bond with the casting matrix. When the surface is shot peened subsequently, the surface metal is easy to peel or even fall off. Peeling is caused by improper flow of molten metal, which is another manifestation of cold insulation.
3 Improvement measures
In view of the above four situations. We look at the specific improvement measures one by one.
3.1 The molten metal filling is discontinuous or unstable, usually due to the following reasons:
3.1.1 The gating system is unreasonable.
– Improved gate. In the case of ensuring the convenience of gate removal, appropriately increase the thickness of the gate and increase the size of the gate.
(Except for thin-walled parts, which sometimes require molten metal to be sprayed into the mould cavity as a mist.)
– Improve the angle of incidence of molten metal. As shown in the figure below, both A and B will cause the molten metal filling to be disordered. C is reasonable and can ensure the continuity of the molten metal filling.
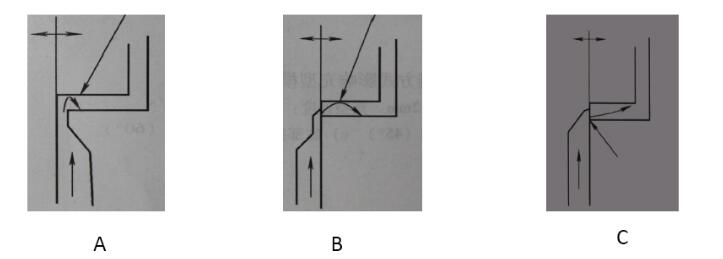
– When designing the flow channel, ensure that the cross-sectional area of the flow channel is gradually reduced, and the cross-sectional area at the rounded corners is also continuously reduced to prevent the molten metal from fluctuating violently and flowing turbulently.
– The gate should be located where the wall thickness is uniform as much as possible. In areas with large differences in wall thickness, the molten metal flow channel tends to be unstable.
– Increase the size of the slag bag or increase the number of slag bags in the peeling place.
3.2 The die casting process is unreasonable.
– The dimensional tolerance of the pressure chamber and the punch should be well matched. If the fit is not good, the forward speed of the punch will not be stable, which will directly lead to the fluctuation of the molten metal.
– The switching position of high speed and low speed should be reasonable.
Tips:
– If peeling is close to the gate: “Early” switch “High and low speed switching position”.
– If peeling is at the far end of the inner gate: “Delay” to switch “High and Low Speed Switch Position”.
Case Study:
Problem: A die casting factory recently purchased a new 500T die casting machine.
The mould was originally produced on a 400T machine. The defective product was produced on a 500T machine. It is also more serious near the mouth.
Analysis:
After the above steps, the process part is analysed, and the peeling position is obvious at the gate, which is initially determined to be caused by the unreasonable switching of high and low speed strokes.
Result:
The “high and low speed switching position” was switched early, which solved the problem of peeling.
3.2 The mould temperature is locally low
3.2.1 Mould temperature control.
– Too low mould temperature can easily cause chilling, which makes the outermost surface of the molten metal solidify in advance. You can try to increase the mould temperature.
The temperature of the aluminium alloy die-casting mould is recommended to be around 250 °C, and the temperature of the zinc alloy die-casting mould is 180-200 °C.
– Check whether the peeling part is close to the cooling water to prevent the mould from cooling too much. You can try to turn off or reduce the cooling water at the peeling part to increase the temperature of this part of the mould.
– Check whether the peeling area is oversprayed, resulting in a decrease in local temperature, reduce the spraying at the peeling area, and increase the mould temperature.
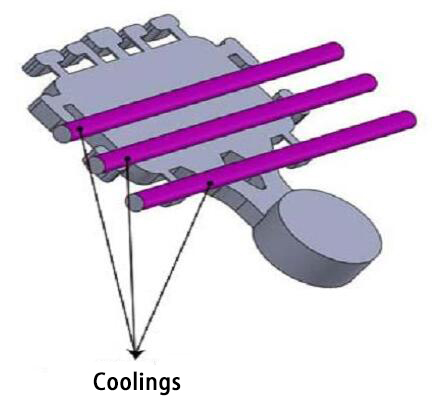
3.2.2 Temperature control of alloy liquid: Minimise the heat dissipation of molten metal.
– The automatic soup feeder can increase the residence time of the spoon in the furnace and reduce the time of other actions, which can reduce the heat loss of the molten metal, and adjust and control the temperature of the molten metal.
– After the molten metal is poured into the pressure chamber, the injection should be started immediately, within 1s. Too long waiting time will reduce the molten metal temperature.
– Increase the slow injection speed, about 0.2~0.75m/s.
3.3 The molten metal that enters first solidifies first and is oxidised by water vapor and soot
– Control the parameters of spraying, too thick spraying, excessive spraying, uneven spraying, and the generated water vapor and oil will aggravate the degree of oxidation of molten metal during filling.
– After spraying, dry the mould cavity, slider groove and parting surface with compressed air. Moisture remaining on the mould surface will react with the molten metal.
– Do not use too much of the punch lubricating granules. Otherwise, the oxidation of the molten metal will be aggravated, and a lot of oil smoke will be generated.
(The standard is that the punch is not stuck and the cake is not black.)
3.4 The molten metal that the subsequent metal enters is covered on it
3.4.1 Mainly to improve the gating system
– When only one inner gate cannot meet the filling performance requirements, multiple gates and multiple feeds can be used.
– Different parts of the casting should be filled at the same time as possible, which is achieved by controlling the length and angle of the runner.
– The less direct fill area the better.
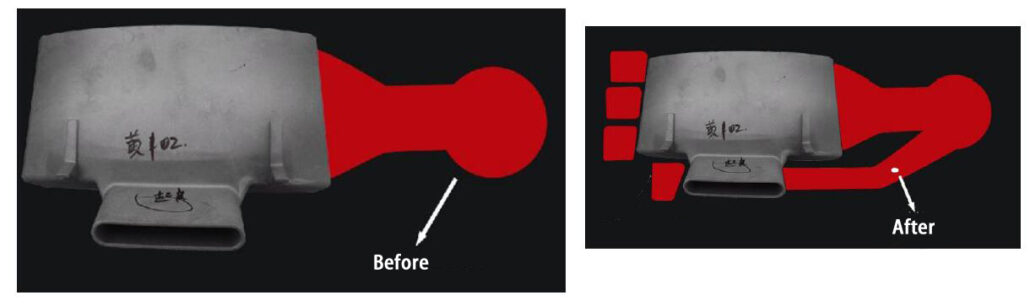
The left side of the above picture is the initial plan, which has peeling defects. On the right is the improved scheme.
4 Improvement of shot blasting and sand blasting process.
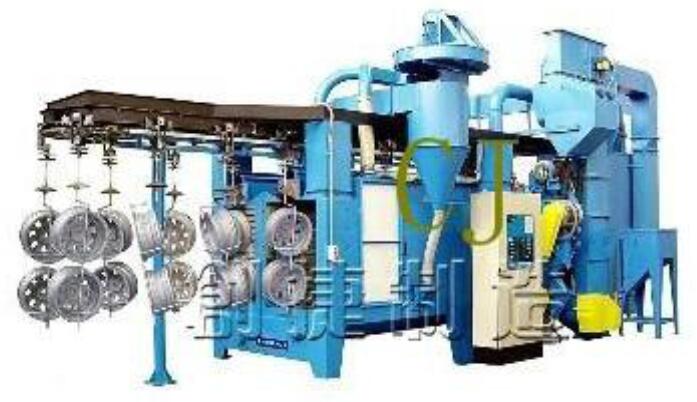
By properly improving some shot blasting parameters, the peeling phenomenon can be improved:
– Appropriately reduce the ejection speed to reduce the impact force of the steel shot on the casting;
– Appropriately reduce the shot peening time; – Use reasonable hangers to ensure that the castings are fixed during the shot peening process and prevent the castings from colliding with each other, and special fixtures can be used if necessary;
– buy steel shot of regular shape;
– Try to use a smaller size shot, such as 0.3-0.5mm shot.
Through the above steps, the peeling phenomenon can be gradually improved, and the peeling problem will be improved. The most important thing is to “practice” and gradually improve these problems through the elimination method.