PVD For Mold
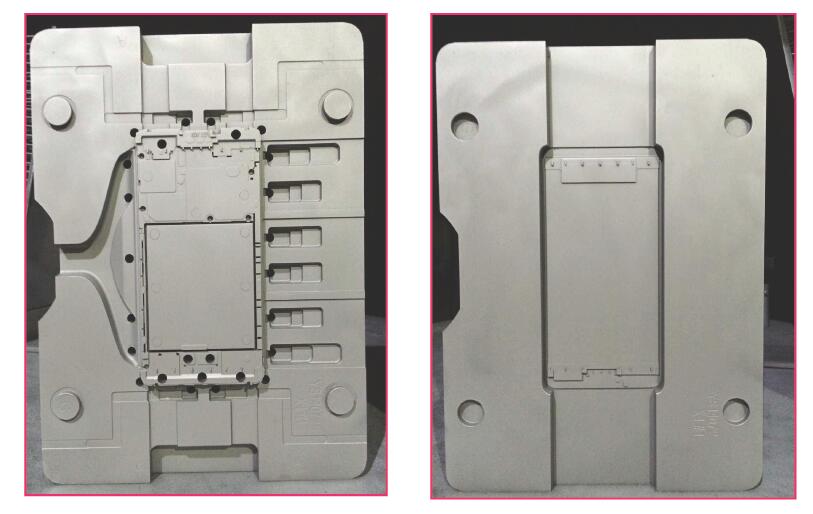
PVD coating technology is currently the most widely used and most valuable type of surface treatment technology. Without affecting the original size of the workpiece, PVD coating can be used to improve surface appearance, improve surface strength, and enhance wear resistance. And has good thermal conductivity, anti-corrosion, self-lubricating, and anti-scratch ability.
1.PVD Definition: Physical Vapor Deposition
Physical Vapor Deposition (PVD) uses physical methods to convert solid plating materials into atomic, molecular, or ionic gas-phase substances under vacuum conditions and then deposit them on the surface of the substrate to form solid thin films.
There are three basic methods of PVD: vacuum evaporation, sputter coating, and ion plating. The main difference is that the physical principles are different.
- Vacuum evaporation is to heat and evaporate the evaporation material into atoms or molecules into the gas phase under the high vacuum condition and then deposit it on the material’s surface to form a thin film coating.
- The sputtering coating bombards the target with charged particles under certain vacuum conditions so that atoms or molecules enter the gas phase at the surface, sputtering and depositing on the workpiece surface, thereby forming a coating.
- Ion plating uses gas discharge to ionize and excite the evaporated target in a vacuum containing an inert gas and deposit a coating on the surface of the base material.
Vacuum evaporation is mainly used for surface function and decorative purposes. The quality of sputtering coating and ion plating is higher. It is more firmly combined with the base material, which can form a wear-resistant enhanced film such as TiN, TiC, Al2O3, etc., on the material’s surface, mainly used for structural parts and molds.
2.PVD and Die Casting Failure
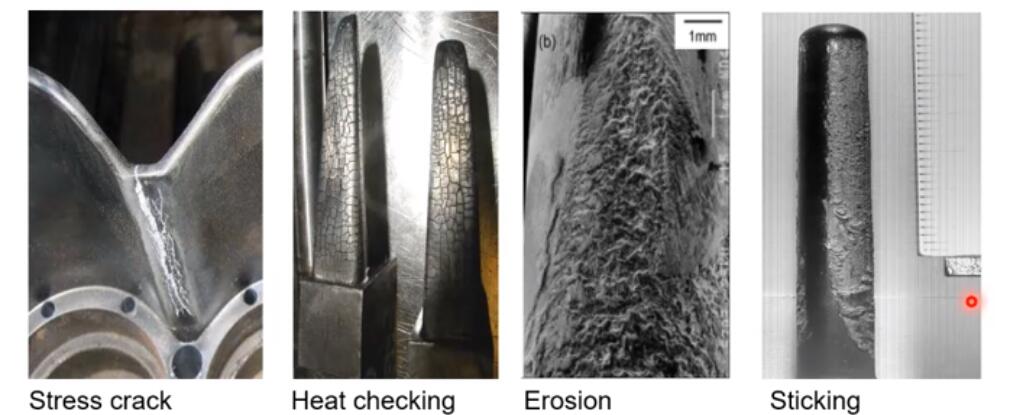
Common failures of die casting molds are shown in the figure. The specific failure reasons can be found in our previous blog.
PVD coating solutions:
- The coating has very high hardness and high wear resistance, which can greatly reduce the wear of the mold and has a good anti-erosion effect.
- Extremely high-temperature resistance, which acts as a thermal insulation layer on the surface of the mold, can well avoid the reaction between the high-temperature aluminum liquid and the matrix during the die casting process to form compounds. In addition, extremely high hardness and wear resistance can protect the mold against the violent impact and erosion of molten aluminum.
- The coating has good chemical and thermal stability, does not react with the solution, can establish a thermal barrier between the aluminum liquid and the mold base, and has excellent anti-sticking, anti-oxidation, and anti-corrosion effects.
- The coating has good toughness and can effectively resist cracking and delay the generation of mold cracks.
- The surface of the coating is smooth, which can effectively prevent the occurrence of aluminum sticking.
3.Advantages of PVD Coating:
- The bonding force between the coating and the mold base is very strong, and it is not easy to fall off.
- The coating has superior high-temperature oxidation resistance and can delay the appearance of fatigue cracks on the surface of the mold.
- The hardness of the coating is as high as HV2000-4500, and the erosion resistance is excellent.
- The production of the coating is in a vacuum environment without pollution. And automatic control of the production process.
- The thickness of the coating can be controlled by the length of the processing time. Therefore, it helps achieve the desired coating thickness.
- The comprehensive cost of the coating is low, and the average production cost of a single product is reduced by extending the life of the mold.
4.PVD production process
Pre-processing
- It is necessary to clean the oxide layer completely and aluminum alloy residue on the surface of the mold; otherwise, it will affect the bonding force of the coating.
- Check the surface for burrs and micro-cracks and remove them.
- For the sharp corners and right angles of the mold, care should be taken when cleaning the mold, and the mold structure cannot be damaged.
- For some decorative surfaces, it is necessary to communicate with the customer to confirm the processing method
- According to the characteristics of different molds, it is necessary to comprehensively use polishing and sandblasting to treat the surface of the mold
- Confirm the coating position in strict accordance with customer requirements.
PVD Equipment
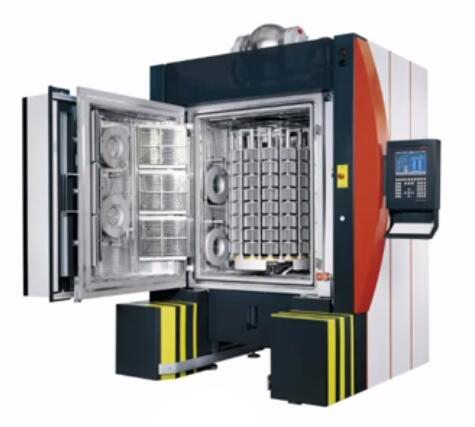
The principle of mold coating processing
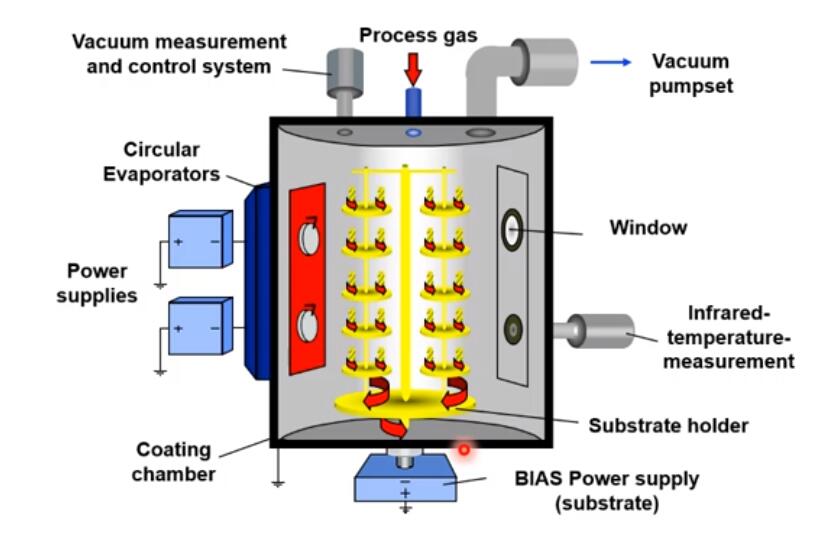
1. Using a vacuum automatic PVD coating machine, place the workpiece on the fixture in the machine.
2. The internal vacuum system starts to work, turning the inside of the machine into a vacuum state;
3. Heat the mold to a temperature of about 450°;
4. Pass in process gas, such as nitrogen or argon, to activate the mold surface.
5. The power supply works, using high current and low voltage to evaporate the target material into the machine;
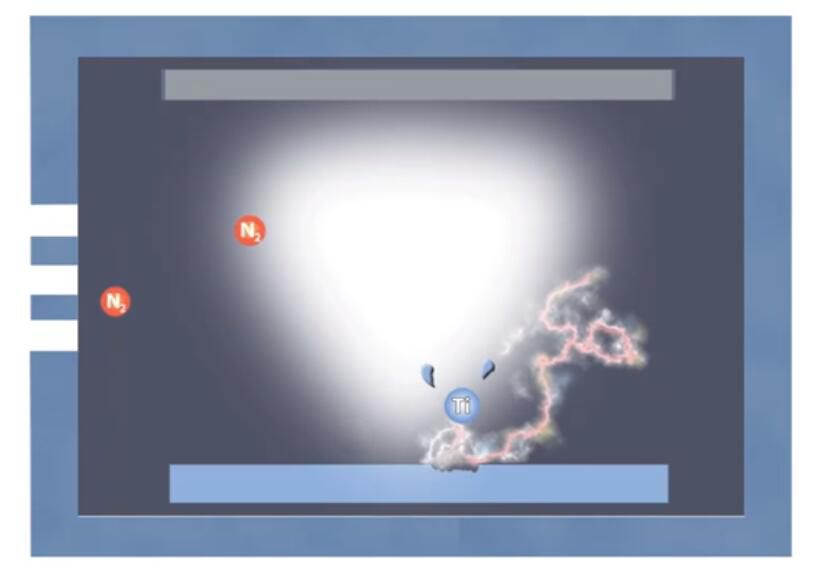
6. The workpiece is connected to a negative voltage so that the mold absorbs the evaporated target, and the negative voltage ensures a powerful bonding force between the coating and the mold base.
7. After depositing a target of suitable thickness on the surface of the mold, cool down and cool down, and the production is completed.
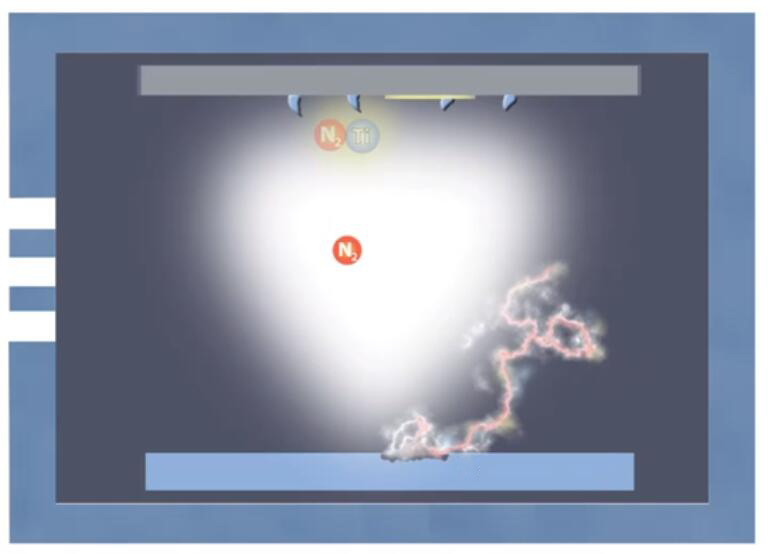
5.Coating Types and Composite Coatings
There are many types of coatings, usually including AlN, TiAlN, CrN, AlCrN, Al2O3, etc.
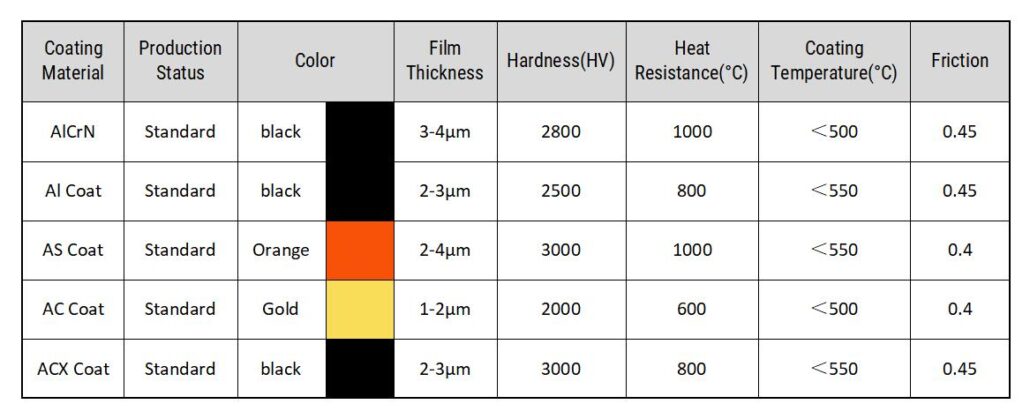
It can also do composite coatings of various materials, and it has been developed to the fourth-generation coating materials, such as composite layers: Ti-TiN-TiAlN-Al2O3
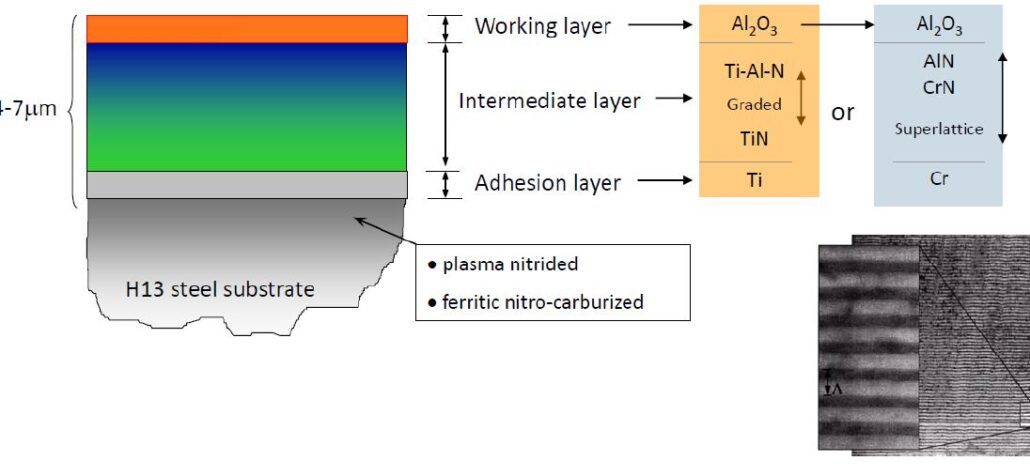
6.Coating Inspection
Wear resistance testing: the testing equipment is a ball mill.
Detection method
A grinding ball with a precisely known radius acts on the surface of the coated sample by its own gravity and rotates. During the test, the relative position of the grinding ball to the sample and the pressure applied to the sample was kept constant. The relative motion between the grinding ball and the sample and the diamond particle grinding fluid’s combined action wear out a spherical cap-shaped pit on the sample’s surface. Wear resistance was evaluated by measuring the size of the dimples.
Hardness testing
Rockwell hardness testing method. Use a diamond indenter to press into the coating surface and observe the size of the coating deformation.
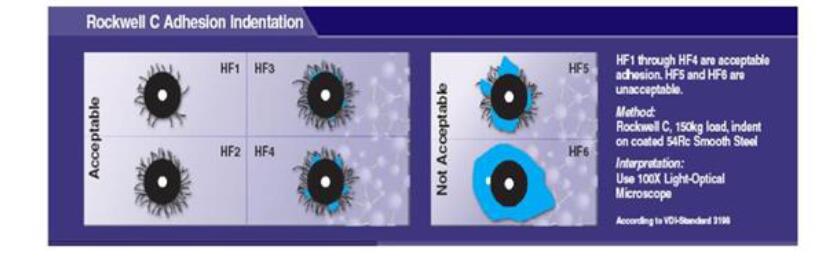
7.Cases
Case 1
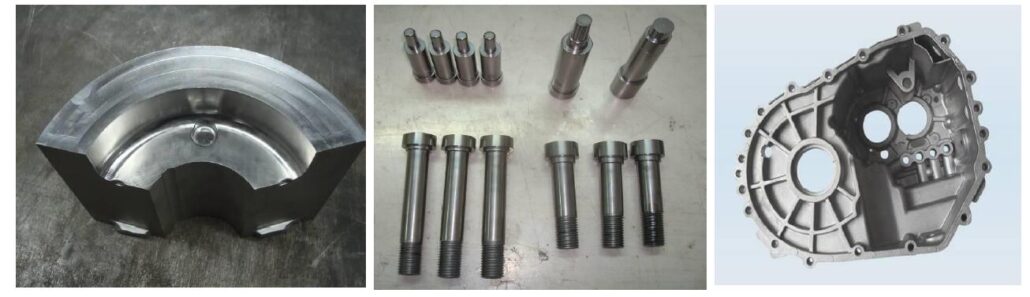
Product name: die-casting die insert and core for cylinder head of automobile air conditioner compressor
Die casting equipment: Lijin DCC500
Mould material: DH31-S
Casting material: ADC12
Working temperature: 700℃-710℃
Before coating:
Core: Die-casting 1000 times, serious sticking to aluminum, need to be removed and polished or replaced;
Inserts: about 1000pcs die-casting, the cavity has erosion marks, 5000pcs products have cracks in the cavity and need to be welded.
After coating:
Core: die-casting 9000 times, sticking to aluminum;
Inserts: die-casting 15000pcs products, the cavity has slight erosion, but no cracks, no need for repair welding; for 30000pcs products, the cavity is eroded and needs repair welding, but there are still no cracks.
Case 2
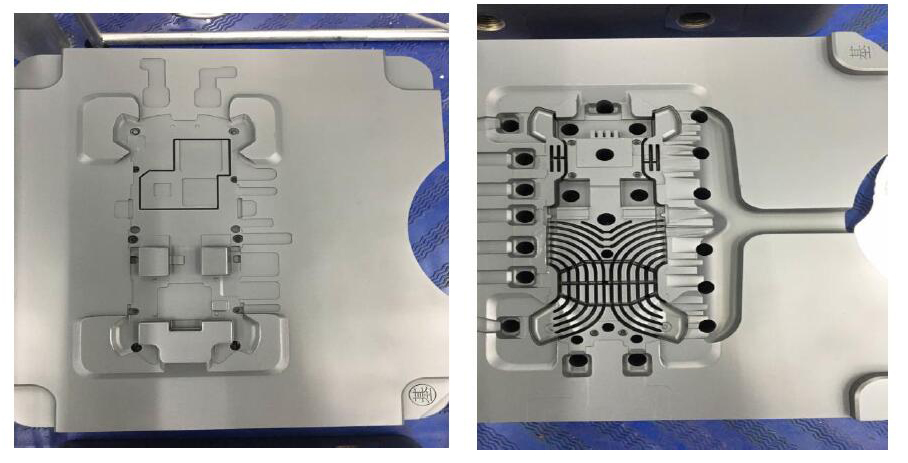
Product name: UAV mid-board
Die casting equipment: Lijin DCC280
Mould material: 8407
Processed material: pure aluminum 6 series
Working temperature: 700℃-730℃
Before coating:
Mold core: die-casting 30 times, serious sticking to aluminum, need to be removed and polished or replaced;
Axle: die casting about 100pcs, with erosion marks, 500pcs products,
The erosion is serious, and the shaft needs to be replaced.
After coating:
Core: die-casting 2000 times, sticking to aluminum, polishing, continuous production;
Axle: Die-casting 15000pcs products, mild erosion, production of 30000pcs products, serious erosion of the axis, need to replace the axis.
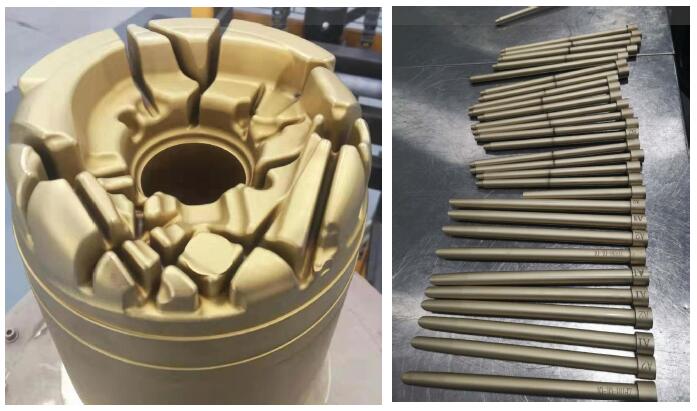
Pictured above is a special custom coating that greatly improves the anti-stick properties of aluminum.
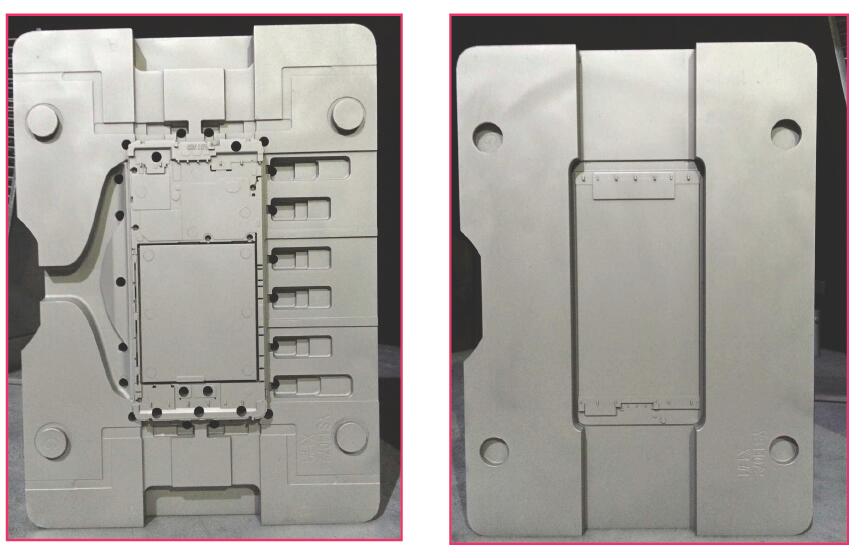
The coating used in pure aluminum die-casting reduces the use of mold release agents.
Mold PVD
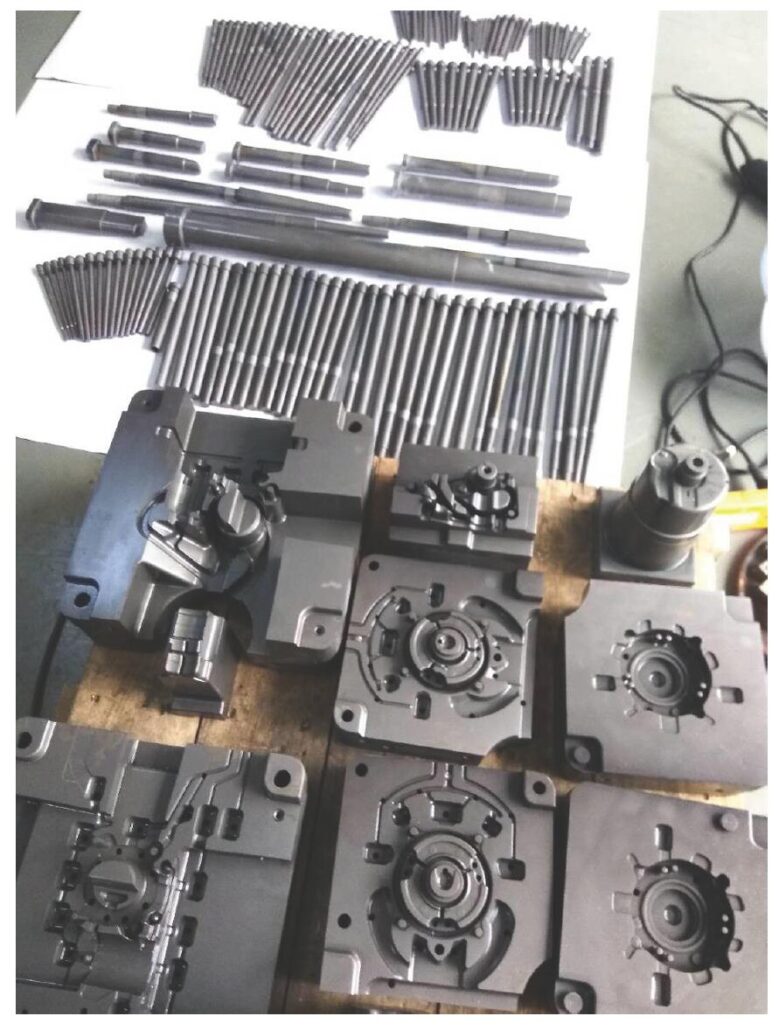
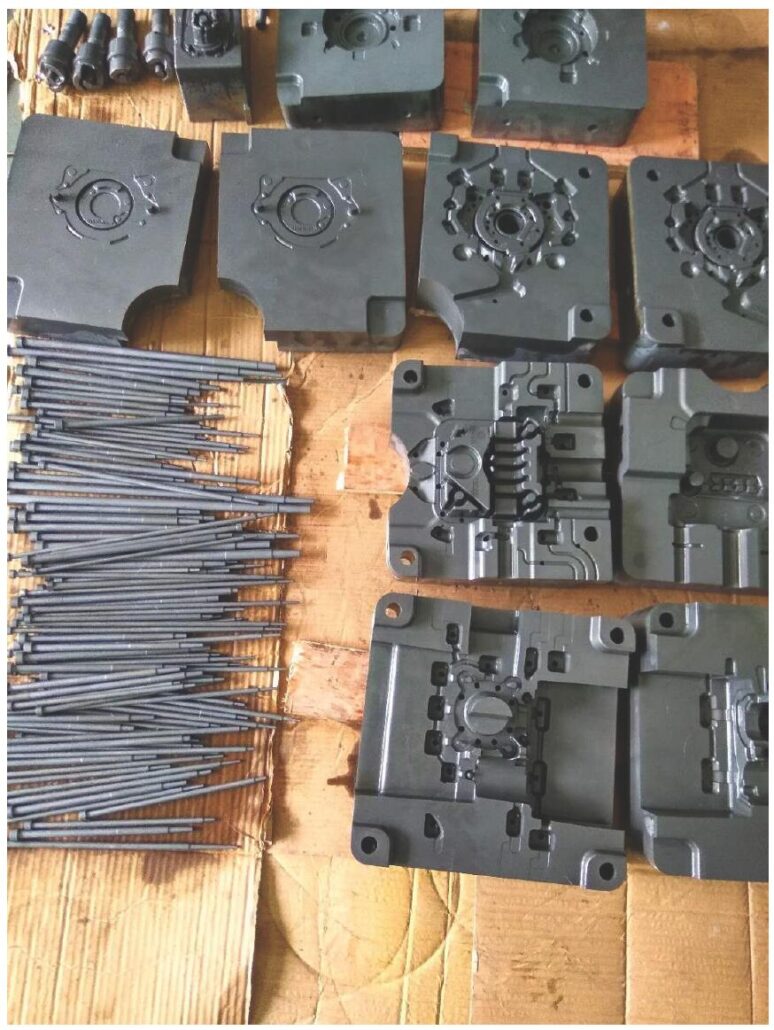
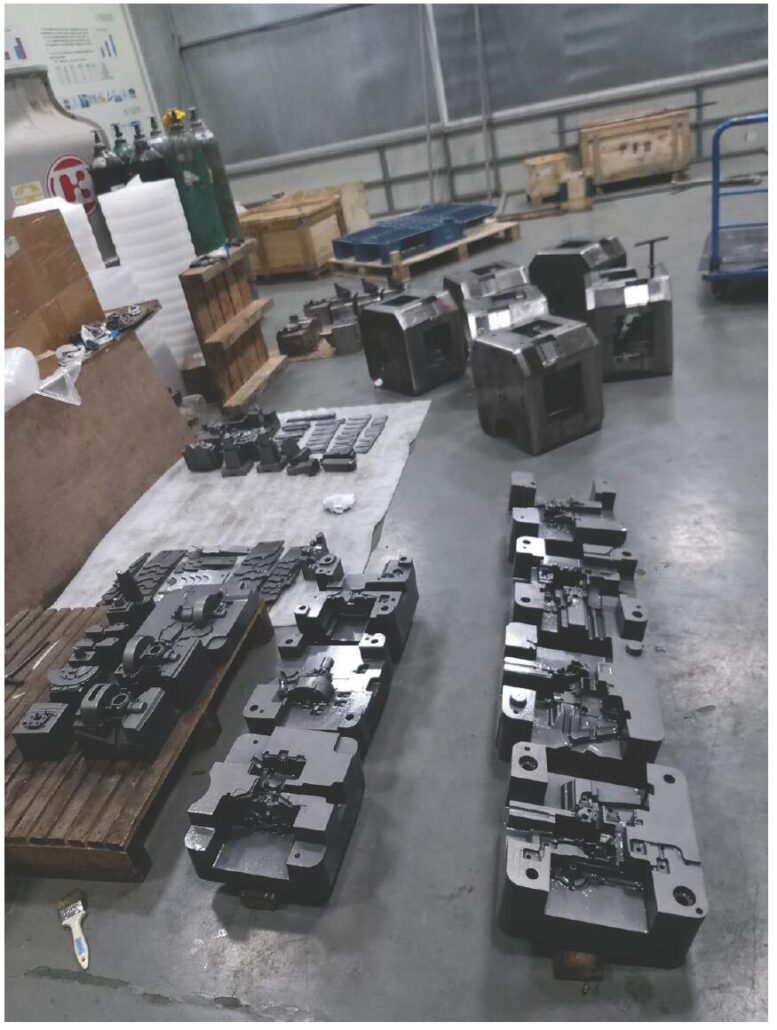