Recognizing and Controlling Potential Flow Defects
Several different factors can cause problems when you’re producing die casting. The most common is flow problems with the die casting process. But what are these, and why do they happen? We will explain it all in this blog post!
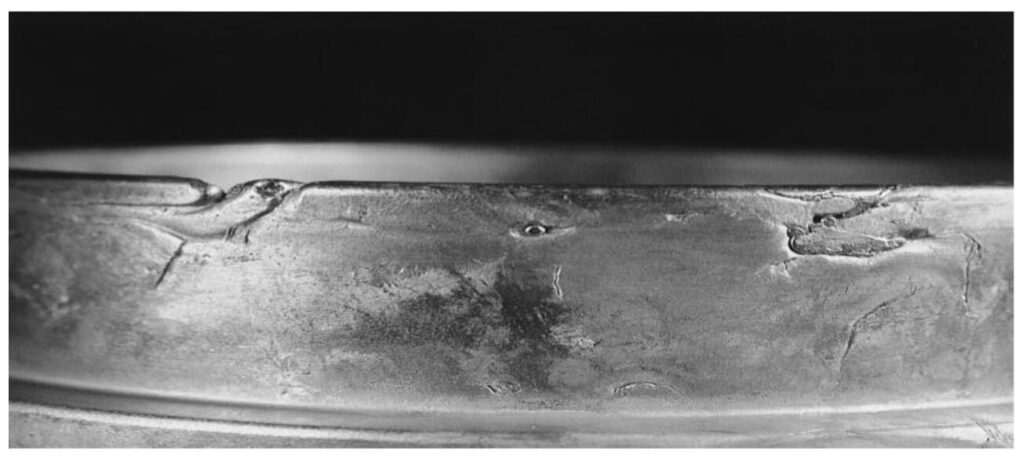
Frequently Asked Questions:
- How to understand the relationship between the fluidity of castings and surface defects?
- What process parameters affect flow defects?
- What are the proper ways to reduce and control liquidity deficiencies?
Management Measures to Control Defects:
- Without measurement and reporting, you will not improve and control defects.
- Defect reports must be established for the relevant departments. Defects are not just a departmental problem but a comprehensive problem.
- The defect report must be visible to everyone in the factory. We should put it on the bulletin board.
- Improving quality is complex, and continuous improvement reports must be established to collect feedback and control defects.
1 Die Casting Defects:
1.1 The Defects of Die Castings Can Be Divided into Two Categories:
1) Surface quality defects, mainly caused by fluidity defects;
2) Porosity.
This article will focus on analyzing and controlling surface defects.
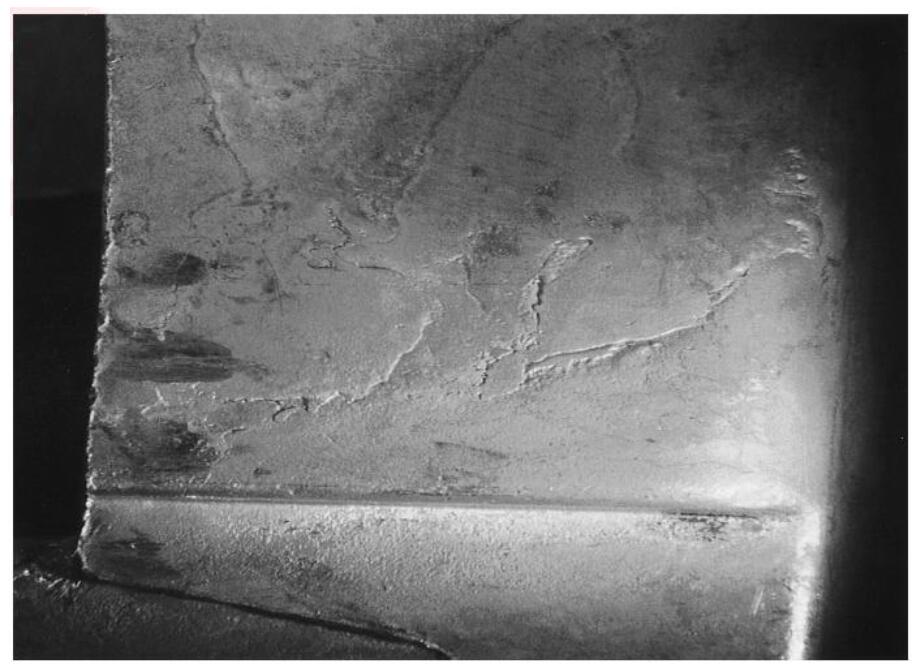
1.2. Common Names of Surface Defects:
Cold Flow. Lines Chill. No-fill Laps. Run Marks.
Cold Shut. Cold. Non-fill. Poor-fill. Lines. Misruns
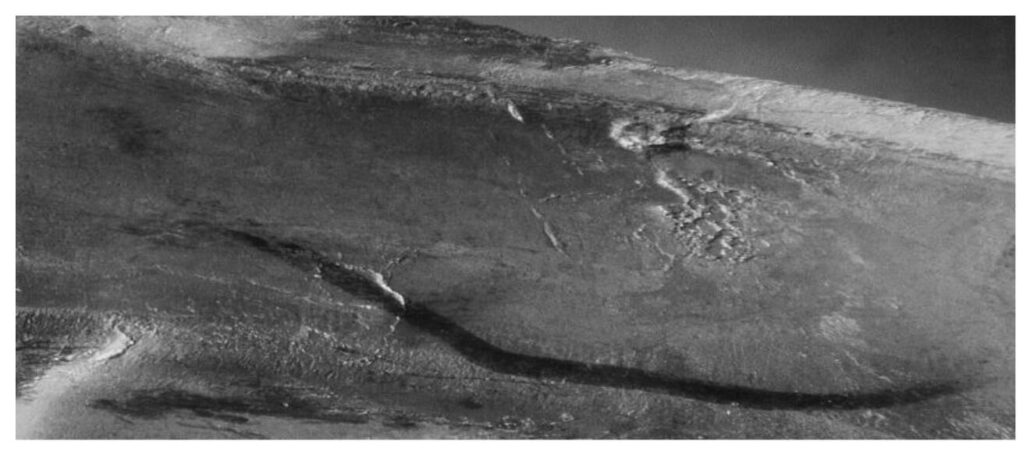
Surface Defect Peeling
Cause of formation: Because the metal flow is too cold to fuse, one metal flow runs on top of another metal flow, causing the metal to divide into several layers.
Metal flow 1 and metal flow 2 meet in the figure and are relatively thin at the point where they meet. When the surface is treated by sandblasting or machining in the later stage, it will be separated from the substrate.
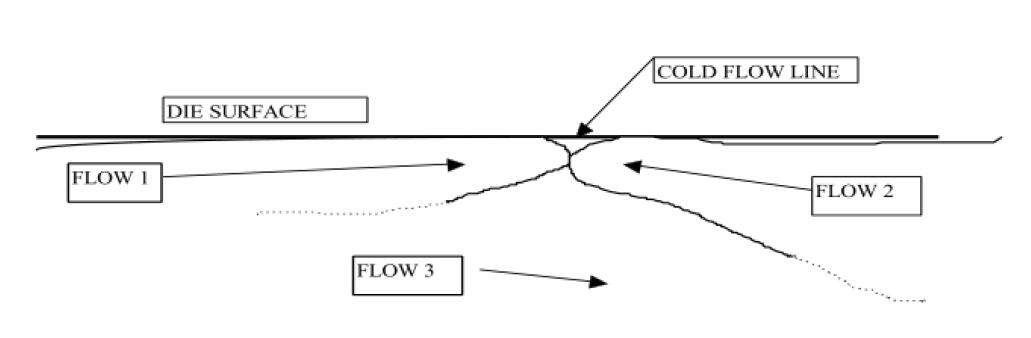
2. Factors Leading to Surface Defects
- Wall thickness
- Casting shape
- Fill time
- Fill mode (gate design)
- The temperature of the mold
- The temperature of alloy liquid
- Type of alloy
None of these 7 factors is the most critical, and none of them controls surface defects and must be comprehensively considered for analysis.
Therefore, the personnel of the whole company needs to cooperate, including workshops, designers, operators, managers, and quality control personnel, to control and improve each process link to control the occurrence of surface defects.
3. Relationship Between Wall Thickness and Surface Defects
3.1 Process Parameters:
The process parameters of thin-walled parts and thick-walled parts are very different. Thin-walled parts are more prone to cold insulation problems.
- Aluminum alloy and magnesium alloy die castings with a minimum wall thickness of about 1.5mm.
- Zinc alloy die-casting with a minimum wall thickness of about 1mm.
3.2 Relationship Between Wall Thickness and Filling Time:
Generally, the smaller the wall thickness, the shorter the filling time. For example: reducing the wall thickness from 2mm to 1.5mm reduces the filling time by 25%.
The wall thickness was reduced from 3.5mm to 3mm, and the filling time was reduced by 12%.
The thinner the wall thickness, the more difficult it is to fill, and surface defects are prone to occur.
3.3 Concerns About Thin-Walled Areas of Castings:
- When there are key quality requirements in the thin-walled casting area, the gate should first meet the thinner area and then consider other thick-walled areas. Meeting the requirements at the thin wall of the casting is often the key to determining the gate of the mold.
- The thin-walled part of the casting determines its shorter filling time, thus determining the process parameters of the product.
- The thin-walled part requires a high filling speed. Generally, the high-speed range of the theoretical filling speed is selected, and sometimes it even exceeds the highest limit.
3.4 If There Is A Thin Wall in The Casting:
- Communicate with designers in time.
- Try to keep the wall thickness uniform.
- Keep the variation of casting wall thickness within a small range.
- The PQ process window may be relatively small and strictly controlled.
- Use a very short fill time.
- It is best to fill this part directly from the gate (an auxiliary runner).
- Use a higher filling speed (within a reasonable filling speed range).
- Use a higher mold temperature.
4. The shape of Die Casting
The die casting structure will also affect the die casting process parameters. The factors we need to consider are:
- The distance of flow. (fill distance from ingate to farthest)
- The complexity of the part
- Filled dead zone. Such as cores, corners, bosses.
- Indirect filling area (different from the direct filling area)
- The maximum height of the casting or the maximum cavity depth
- Gate location selection
By analyzing the above factors, in actual production, the parameters that the operator can control are:
1. Fill time.
2. Fill mode.
3. Mold temperature.
4. The temperature of the molten metal.
5 Fill time
5.1 The Formula Given by The North American Die Casting Association:
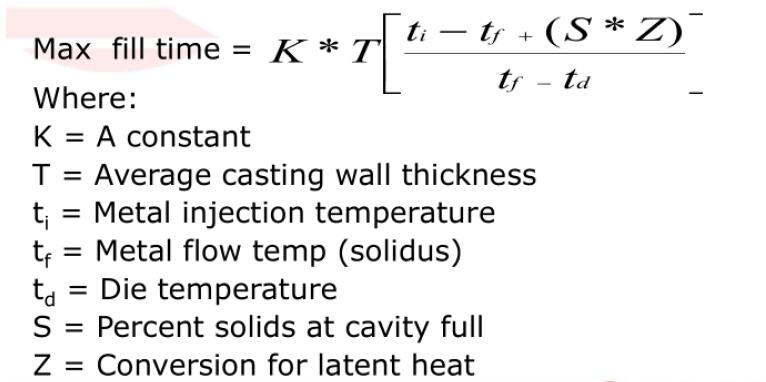
5.2 Empirical Data for Filling Time
The following table is rough empirical data for filling time, but it is suitable for most castings.
Note: If the product surface requirements are high, the above filling time is reduced by 50%.
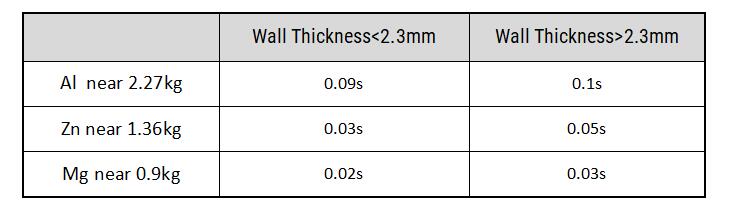
5.3 Set The Filling Time, Preferably Using The PQ Chart.
According to PQ2, the optimal filling time and filling speed can be obtained by changing the following parameters.
- Gate area.
- Punch size.
- Accumulator pressure.
- The speed of the punch.
Many factors affect the speed of the punch, which affects the filling time, which affects the quality of the surface. Common factors are:
- Punch stuck.
- Poor lubrication of the punch.
- The pressure chamber is in poor condition.
- Poor cooling of the punch.
- The pressure of the hydraulic system of the die casting machine is unstable.
- Insufficient nitrogen pressure
6 Fill Pattern
The filling pattern of the casting is determined when the gate is designed. The choice of fill mode requires careful and careful consideration. This is a very critical part of casting runner design.
Fill Pattern Design Rules:
- Use PQ diagram to determine gate size and punch size based on reasonable casting pressure, filling speed, filling time.
- Divide the casting into multiple areas. Divide the gate proportionally to ensure that each area is filled simultaneously.
- Try to choose short metal-filled routes.
- Try to avoid metal flow mixing (except at the gate).
- The gate is arranged in part with thick wall thickness to avoid shrinkage or in part with high surface quality requirements.
- Avoid the metal flow directly impacting the core, and spread the metal liquid to fill it.
- If possible, try to set the vent position opposite the gate.
- Keep the molten metal filled smoothly.
- When the alloy liquid is filled when encountering the core or the cross-sectional area becomes larger, air entrainment will be generated. Pay attention to this situation at the gate.
The table below shows the minimum and maximum gate speed settings.
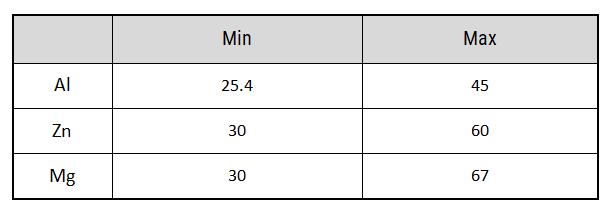
The minimum value of the velocity is based on the minimum atomized flow of the molten metal. When the gate thickness is thick, its speed may be lower.
The maximum speed, which is based on erosion, depends on the product’s shape. In some cases, the gate speed may be higher.
7 Mold Temperature
If the mold temperature is too low, it will reduce the temperature of the molten metal and increase the proportion of solid metal in the molten metal, thereby affecting the surface quality. When the proportion of condensed metal increases, the metal does not bond tightly together, resulting in flow pattern defects.
In the best state, we need to test the mold temperature after each mold, and only in this way the surface quality problem will be avoided. But it’s hard for us to do that.
- Generally, We Can Measure the Mold Temperature in Three Ways.
- Handheld thermometer.
- Infrared devices.
- Each Method Has Advantages and Disadvantages:
- Handheld thermometers are accurate but must be stopped to measure.
- The thermocouple measures the temperature inside the mold but not the mold surface temperature.
- Infrared devices are easy to use but imprecise.
The mold surface temperature is shown in the table below:
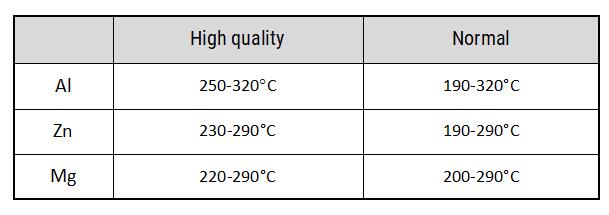
- The operator can control the mold temperature by:
- Time for mold spraying.
- The flow of waterways.
- Die casting production cycle time.
- Designers can improve the design of the cooling water circuit to change the degree of influence of the above factors on product quality. But the actual need to rely on the operator to control the above parameters.
Operating Instructions for Mold Cooling Water
- When designing the mold, give priority to setting the cooling pipeline and then consider the position of the ejector pin.
- Avoid using the same cooling line in areas that need cooler or hotter.
- The size of the cooling water pipes must match the flow requirements.
- Pay attention to whether the cooling water pipe is blocked.
- Use constant water pressure and test and control flow.
- Use computer for thermal balance analysis to optimize die casting cycle time.
8 Alloy Temperature and Surface Defects
The molten metal temperature can cause significant changes in the surface quality. If necessary, improve fluidity by increasing the temperature of the molten metal.
Generally speaking, we want to keep the molten metal temperature in a high range. If the temperature is not enough, it will cause many problems.
The general molten metal temperature is as follows:
- Zinc 420
- Aluminum 680
- Magnesium 680
For the molten metal temperature, the most important thing is to keep the holding temperature within a range of fewer than 10 degrees.
High molten metal temperature can cause some problems:
- High temperatures can cause flash, corrosion of the shot head, and gooseneck for zinc alloys. In addition, it will cause the magnesium element in the alloy to volatilize.
- High temperatures can cause flash and oxide formation for aluminum alloys—corrosion of the pressure chamber and punch, reducing the life.
Therefore, the method of increasing the molten metal temperature needs to be reasonably controlled.
9 Types of Alloys and Surface Defects
Different types of alloys result in different surface qualities.
- Among zinc alloys, Zamak 7 has the best flow and surface finish.
- The alloy is close to eutectic in aluminum alloys, with better fluidity and surface treatment.
- Eutectic alloys have a smaller crystalline range, so temperature control is very important.